Exploring Copper Foams: Properties and Diverse Applications
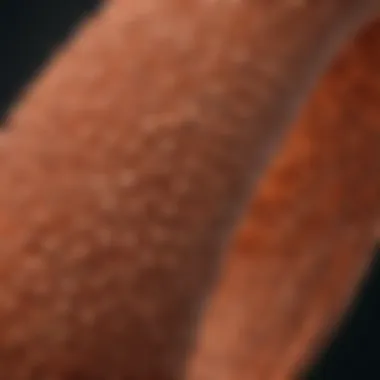
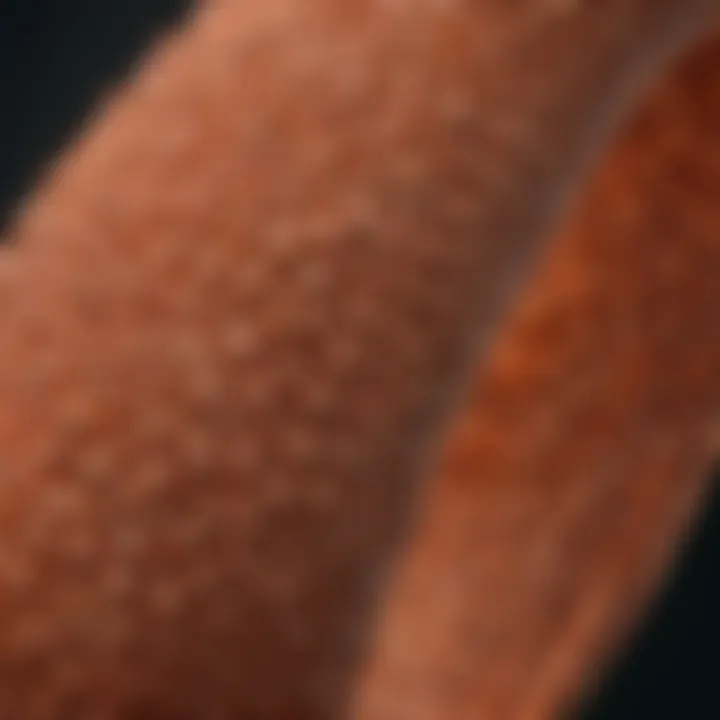
Intro
Copper foams are increasingly capturing the attention of scientists and engineers alike for good reason. This lightweight and porous material stands at the intersection of innovation and practicality, paving the way for new applications in diverse fields. From energy storage to medical devices, copper foams are not just a passing trend; they are defining a new era of material science.
The unique attributes of copper foams include their high thermal and electrical conductivity, combined with their lightweight structure, which can be utilized in a range of applications. Moreover, with antimicrobial properties, these foams are particularly relevant in healthcare and sanitation technology.
The demand for copper foams is on the rise, raising questions about how they are made, their particular properties, and the landscape of applications where they can shine. Understanding these facets is critical not only for academic research but also for practical implementations in industries that are continuously seeking better materials.
By peeling back the layers of copper foams, we can appreciate their composition, properties, and the astonishing ways they can be employed. So, let’s dive into the heart of this material.
Preface to Copper Foams
Copper foams are increasingly garnering attention in both academic and industrial landscapes, establishing themselves as materials of significant promise. This article delves into the nuances surrounding copper foams—examining their properties, manufacturing processes, and the myriad applications they support. By understanding copper foams, we can appreciate their role in advancing technology across sectors such as energy, healthcare, and transportation, among others. This section is crucial for setting the stage for a deeper exploration of this fascinating subject.
Definition and Characteristics
At its core, a copper foam is a porous structure comprised primarily of copper, characterized by its unique cellular architecture. These structures exhibit a combination of high porosity and low density, which distinguishes them from other forms of copper materials. The typical characteristics of copper foams include:
- Lightweight Design: The porous nature allows for substantial weight reduction while maintaining structural integrity.
- Excellent Thermal Conductivity: Copper foam provides efficient heat transfer properties, making it an ideal candidate for thermal management applications.
- Corrosion Resistance: Copper, by itself, has natural resistance to various corrosive environments, enhancing the longevity of the foam products.
The intricate structure of copper foams, which can consist of various pore sizes and configurations, influences their performance in practical applications.
Historical Context
The journey of copper foams began with the broader exploration of porous materials in the mid-20th century. Initial studies were mainly focused on understanding fundamental principles of porosity and its effects on physical properties. The fascinating interplay of copper’s characteristics with the requirements for lightweight, strong materials caught the attention of researchers and engineers.
The growth in demand for energy-efficient materials sparked an interest in copper foams, especially as industries began moving towards sustainability. During the late 1980s and 1990s, breakthroughs in manufacturing methods began to pave the way for a more refined production of copper foams. From fusion methods to advanced powder metallurgy techniques, the manufacturing landscape evolved, enabling the realization of tailored porosity and structural design.
As time progressed, the application of copper foams expanded beyond traditional metallurgy, finding their way into sectors like electronics, biomedical devices, and noise reduction technologies. Today, copper foams are recognized not just for their structural benefits but also for their potential in innovative applications, particularly in energy storage and environmental sustainability.
Fundamental Properties of Copper Foams
Understanding the fundamental properties of copper foams is pivotal for anyone looking to tap into the potential of this unique material. These properties shape how copper foams can be utilized in various applications and industries, from energy solutions to construction enhancements. Each property has its own significance and, together, they build a robust profile of copper foams that appeals to researchers and professionals alike.
Physical Properties
Density
When we talk about density in the context of copper foams, we are looking at how much mass is packed into a certain volume. This key aspect can significantly affect the performance of copper foams in applications that require specific weight requirements. For example, a lower density makes copper foams lightweight, an essential characteristic for aerospace components where every gram counts. But don’t let that characteristic fool you; despite being lightweight, many variants maintain a solid strength that makes them functional and practical.
A unique feature of density is its relationship with the open-cell and closed-cell structures of foam. In open-cell copper foams, the density varies with the size and arrangement of the pores, which can be tailored to specific needs. This adaptability is a main reason why some industries favor copper foams.
Porosity
Porosity is another cornerstone of copper foams. It refers to the amount and size of voids within the foam structure. High porosity translates to more open spaces, which can be crucial for applications needing good airflow, like filters or sound absorption. Moreover, high porosity is beneficial for enhancing reactivity in applications such as catalysis.
On the downside, increased porosity can sometimes lead to decreased mechanical strength. The key here is finding the right balance depending on the intended usage. A unique feature of porosity is that it can be precisely controlled during manufacturing. Therefore, producers can craft foams to achieve the necessary performance metrics desired for specific applications.
Conductivity
When discussing copper foams, it is impossible to overlook their electrical conductivity. Copper is an excellent conductor of electricity, and this property extends into its foam forms as well. In many electrical applications, this conductivity is an invaluable asset, allowing for innovative designs that traditional solid copper might not facilitate.
Conductivity is crucial in energy storage systems, where electric current impacts the overall efficiency. Yet, there’s a trade-off; the more porous a foam is, generally, the lower its conductivity might become. Therefore, consideration must be given to the design specifications to ensure that the foam can effectively transmit electricity as needed while still providing other beneficial features.
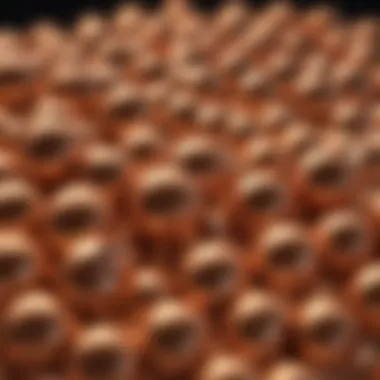
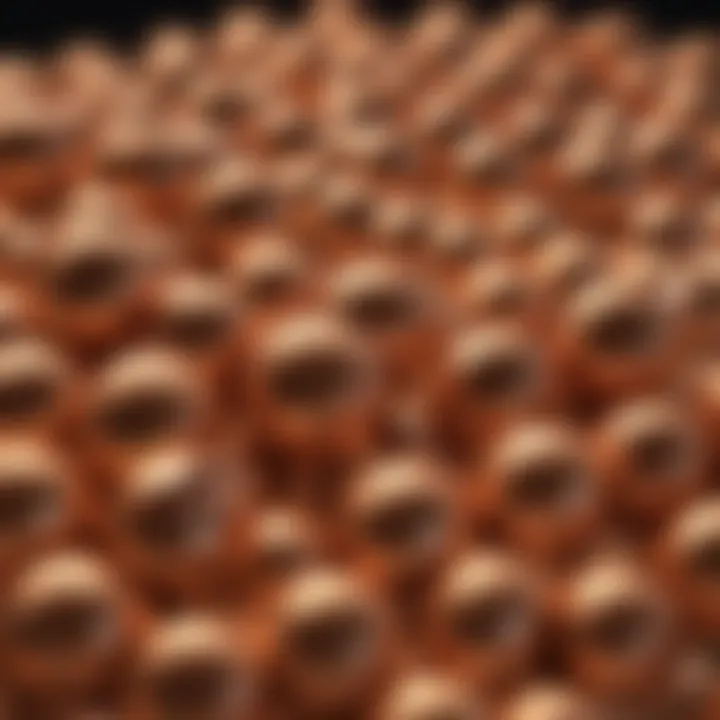
Mechanical Properties
Tensile Strength
Tensile strength refers to the resistance of copper foams to being pulled apart. This property is vital for applications subjected to stress, as it determines how much force the foam can withstand before deforming. A high tensile strength is essential in applications where structural integrity is key, like in the automotive or aerospace sectors.
What’s more interesting is how tensile strength can vary depending on the foam's density and porosity. An ingeniously designed foam can provide not only the necessary strength but also maintain a reasonable weight. This adaptability makes copper foams a popular option for engineers looking for innovative materials.
Compressive Strength
In contrast to tensile strength, compressive strength is about how much force copper foams can handle when being pushed together. This property is particularly important when considering applications like building materials, where the foam must withstand loads over time. In essence, higher compressive strength provides a better solution for lasting durability.
Copper foams can be engineered to have high compressive strength without significantly increasing their weight, thus balancing performance and efficiency. This aspect opens doors for their use in structural components, as it allows for the design of stronger, lighter materials.
Elastic Modulus
Elastic modulus measures how much a material will deform under stress. A high elastic modulus implies that the foam will not easily bend, which can be crucial in applications needing rigidity. Copper foams can be tailored to achieve varying elastic modulus values, depending on the specific needs of the application.
A notable feature of elastic modulus in copper foams is its ability to contribute to energy absorption. This can be critical for impacts, making copper foams advantageous choices for dynamic applications, such as cushioning materials.
"The fundamental properties of copper foams not only highlight their versatility but also their potential across industries - from energy to construction."
In summary, the physical and mechanical properties of copper foams create a compelling case for their use in various applications. Whether it is density, porosity, conductivity, or mechanical strength, each property plays a distinct role in determining the suitability of copper foam for a specific purpose. This comprehensive understanding is critical for anyone looking to engage with this innovative material.
Manufacturing Techniques for Copper Foams
Manufacturing copper foams is a crucial aspect that influences their properties and potential applications. This section will delve into various techniques, explaining their implications for the final material characteristics. Understanding how these foams are made not only highlights the ingenuity involved but also points to the benefits and considerations for different applications. Each manufacturing method offers unique advantages and challenges, which can affect factors such as cost, scalability, and material quality. Exploring these methods equips researchers and industry professionals to make informed decisions in both the development and application of copper foams.
Powder Metallurgy Methods
Powder metallurgy serves as a foundation for many copper foam manufacturing processes. This technique revolves around compacting and sintering metal powders to create porous materials. For copper foams, the process can be broken down into a few essential steps:
- Preparation of Metal Powder: High-purity copper powders are generally chosen due to their desirable properties, such as excellent conductivity and corrosion resistance.
- Compaction: The powdered metal is compacted under high pressure to form a green body. The density achieved in this step influences the foam’s porosity and strength.
- Sintering: This involves heating the compacted powder in a controlled atmosphere, promoting particle bonding while achieving the desired porosity.
One of the key benefits of this method is the ability to tailor the porosity and density of the final product based on the application requirements. However, the process can be sensitive to environmental conditions, and ensuring optimal sintering can be a significant challenge.
Electrochemical Techniques
Electrochemical methods present an innovative route to produce copper foams, leveraging the principles of electrolysis. In this approach, a copper electrode is immersed in an electrolyte solution, and an electric current is applied. Here’s how it typically unfolds:
- Electrolyte Selection: A suitable electrolyte is crucial for effective foam formation. Common choices include copper sulfate solutions.
- Current Application: By controlling the electric current, copper ions are reduced at the electrode surface, resulting in the formation of a copper foam structure.
- Morphology Control: Adjusting parameters like current density and time can modify the foam's morphology, allowing for bespoke properties tailored for specific uses.
This technique excels in producing highly uniform and intricate foam structures that are difficult to achieve with traditional methods. However, the complexity of managing electrochemical conditions can be a drawback. Continuous research is ongoing to refine these methods to enhance reliability and efficiency.
Additive Manufacturing Approaches
Additive manufacturing (3D printing) is making waves in many fields, and copper foams are no exception. This method allows for precise control over the material's geometry and structure. Here’s a glimpse into how additive techniques are utilized:
- Material Preparation: Specialized copper powders or filaments are used, often blended with other materials to optimize performance.
- Layer-by-Layer Construction: The printer deposits material layer by layer, enabling complex design architectures that can’t be achieved through traditional methods.
- Post-Processing: Once the structure is printed, further treatments might be required, such as sintering, to improve mechanical properties and conductivity.
The greatest strength of additive manufacturing lies in customization. It facilitates the creation of highly specialized designs tailored for specific applications, such as in aerospace or biomedical fields. However, the equipment and expertise required can be a barrier for smaller operations.
The choice of manufacturing method significantly impacts the properties and applications of copper foams, showcasing the balance between complexity, cost, and material characteristics.
Applications of Copper Foams
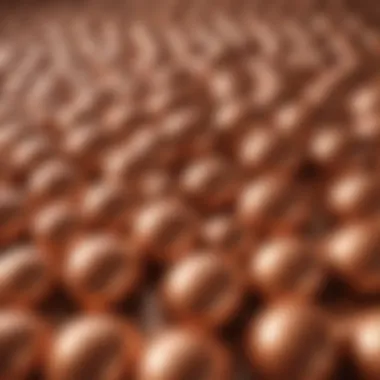
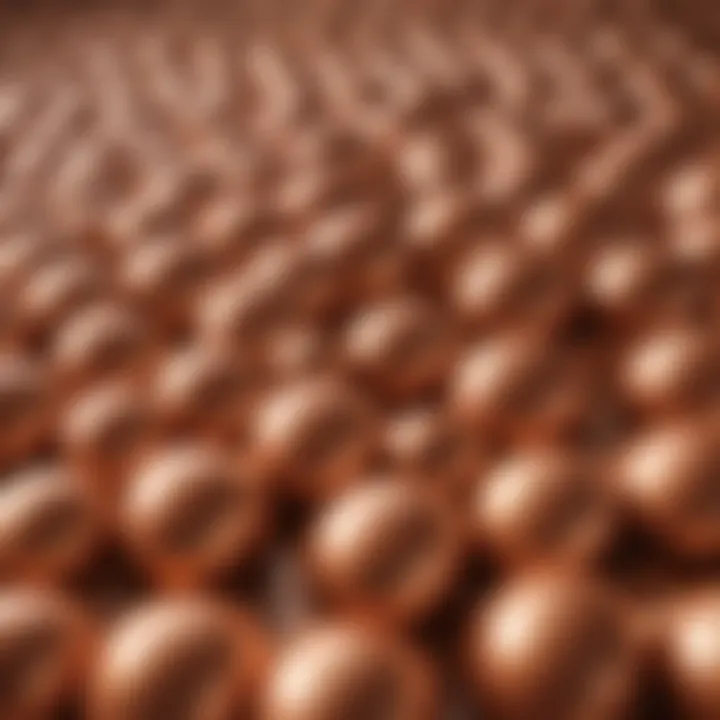
Copper foams are carving out a significant niche in various sectors thanks to their unique properties. From energy storage to sound absorption, these materials have proven to be incredibly versatile. Their lightweight structure, high thermal conductivity, and excellent mechanical properties make them prime candidates for applications in cutting-edge technologies. Understanding these applications can shed light on why copper foams are being increasingly integrated into various industries. Below, we’ll unfold some specific applications of copper foams and their individual significance.
Energy Storage Systems
Batteries
When discussing batteries, one must appreciate the role copper foams play in enhancing the performance of energy storage solutions. The porous structure of copper foam significantly increases the surface area, which can lead to improved charge/discharge rates. This characteristic is not only essential for battery efficiency but also for increasing the overall capacity of the battery itself. The incorporation of copper foams can help in achieving lighter battery designs while maintaining performance levels, a win-win scenario for manufacturers and users alike.
However, it’s worth noting that while copper foam enhances certain battery aspects, trade-offs can exist. For instance, while they improve thermal efficiency, the material's cost, and manufacturing complexities can be considerable. Thus, developers must weigh these factors when considering copper foams in battery production.
Supercapacitors
Likewise, supercapacitors benefit greatly from using copper foams. A standout characteristic of supercapacitors is their ability to deliver rapid bursts of energy, making them especially useful for applications that require quick power. The architecture of copper foam supports this need beautifully, enhancing the effective surface area available for charge storage. This particular element allows for faster ion transport, resulting in quicker charging times compared to traditional energy storage devices.
Nevertheless, while supercapacitors demonstrate considerable energy density when integrated with copper foams, they tend to fall short in terms of overall energy capacity compared to batteries. Thus, practitioners often need to design systems that utilize both batteries and supercapacitors in tandem for optimal results.
Heat Exchangers
Copper foams also play a pivotal role in heat exchanger applications. The high thermal conductivity of copper combined with its porous nature allows for superior heat transfer capabilities. This is crucial in many industrial settings, such as HVAC systems and electronic cooling solutions. The structure facilitates enhanced fluid flow and thermal exchange, leading to improved energy efficiency in systems that rely on heat transfer.
Moreover, the lightweight characteristic of copper foams allows for a reduction in weight constraints, making them easier to implement in various designs. Yet, one must consider that while implementing copper foams may lead to improved performance, managing corrosion in certain environments remains an ongoing challenge.
Antimicrobial Applications
In recent years, the antimicrobial properties of copper have drawn attention, and when combined with the structure of copper foams, the result is a potent material for applications in healthcare and sanitation. The porous nature provides a larger surface area for interaction with microbial agents, making copper foams effective in eliminating harmful bacteria and viruses. This quality makes them ideal candidates for use in hospital settings, public transport, and food processing facilities.
However, it is crucial to ensure that the foams are properly treated or coated to maintain their effectiveness over time, as wear and tear can influence their antimicrobial properties.
Sound Absorption Materials
Lastly, a noteworthy application of copper foams is in sound absorption. The structure of copper foams allows them to trap sound waves, making them excellent candidates for acoustic panels in recording studios or as part of insulation systems in buildings. Their ability to attenuate airborne noise without adding significant weight makes them an attractive choice for architects and builders aiming for noise reduction without compromising structural integrity.
Nonetheless, one considers the cost-effectiveness of using copper foams for this purpose, given that alternative materials might offer cheaper solutions. As the market evolves, finding ways to integrate or substitute copper foams while retaining their beneficial properties remains a topic of ongoing exploration.
Overall, the applications of copper foams showcase their versatility and extraordinary potential across various sectors. As innovations continue, integrating these materials could pave the way for groundbreaking advances in technology and sustainability.
Environmental Considerations
The discussion surrounding copper foams extends beyond their immediate uses and properties, leading to significant reflections on environmental implications. As industries increasingly turn their focus towards sustainable development, the relevance of evaluating the environmental footprint of materials like copper foams can't be overstated. This section sheds light on the sustainability of copper, as well as its recycling potential, illustrating how these factors contribute to a cleaner and more responsible use of resources.
Sustainability of Copper
When considering materials for future technologies, sustainability plays a vital role. Copper, a naturally occurring metal with an ancient pedigree, offers a range of sustainable advantages. For starters, it is an abundant element, widely available within the Earth's crust. Also, copper foams, due to their unique structure, often allow for reduced material use in applications without compromising functionality. This arrangement can be beneficial in meeting the modern industry's demands for lightweight yet durable materials.
Copper's inherent properties extend its lifespan, contributing towards sustainability. Its excellent conductivity makes it essential in electrical applications, meaning lifetime durability and low maintenance are key aspects to consider. When it comes to waste management, copper has a well-consolidated profile: it's fully recyclable. This recyclability ensures that at the end of its life cycle, copper can be processed and repurposed, reducing waste and encouraging circular economies. The reliance on copper foam in clean energy technologies further expresses its sustainable nature, exemplifying a forward-thinking approach in industries where environmental impact is under scrutiny.
Recycling Potential
Recycling is often touted as a linchpin in efforts to minimize waste and conserve resources. The recycling potential of copper, specifically in foam form, is remarkably high. As a metal that retains its properties, copper can be repeatedly recycled without losing its integrity. This is a massive plus when one considers the general life cycle of a product.
The recycling process involves collecting scrap metal, which can either come from industrial scraps or consumer products. With appropriate techniques, the production of copper foams can be ramped up using recycled materials, significantly lowering the environmental burden associated with primary extraction. Indeed, some estimates suggest that nearly 80% of the copper ever mined is still in use today, underscoring the effectiveness of recycling practices.
"Copper’s life cycle is a testament to recycling’s vital role in sustainable industry."
In practical terms, effective recycling programs for copper foams not only contribute to reducing the demand for virgin materials but also lower energy consumption associated with manufacturing. This transition toward utilizing recycled materials in production processes underscores the urgent need for a recycling infrastructure capable of handling modern demands.
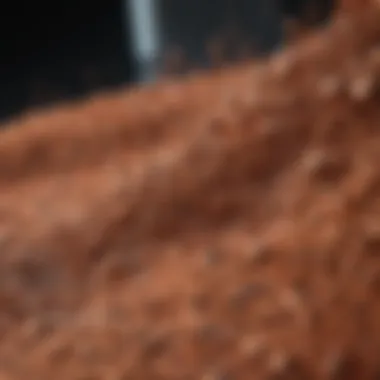
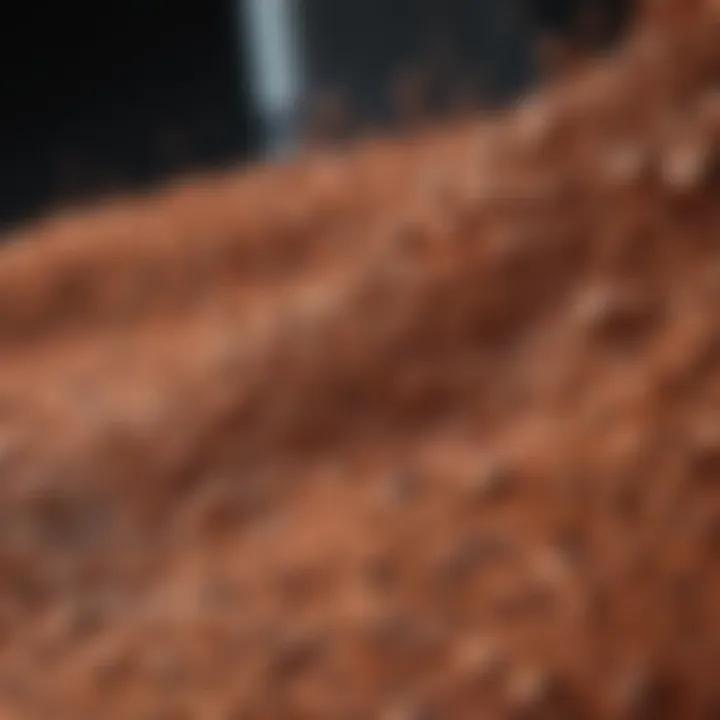
In summary, the importance of environmental considerations in the context of copper foams links closely with sustainability and recycling. As industry players evaluate materials based on environmental impact, copper, especially in its foam form, stands out as a prime candidate. It aligns with the tide of responsible production and consumption, additionally highlighting an effective framework for addressing future resource challenges.
Current Research Trends in Copper Foams
The field of copper foams has recently seen a surge in research interest, gripping the attention of scientists and industry professionals alike. The exploration of current trends serves as a litmus test for the future potential of these innovative materials. As we probe deeper, it becomes clear that a few specific elements are gaining traction in research circles, showcasing not only the inherent benefits of copper foams but also addressing broader considerations that echo throughout various industries.
Advances in Manufacturing Techniques
Recent advancements in manufacturing methods for copper foams are shaping the landscape significantly. Traditional production techniques, such as powder metallurgy, have been refined, allowing for greater control over the foams' microstructures. New strategies, including novel forms of additive manufacturing, are emerging. These methods enhance the ability to create foams with precise porosity and specific mechanical properties tailored for distinct applications.
A few noteworthy techniques include:
- Selective Laser Melting (SLM): This technique allows for high customization and complex geometries, making it an invaluable asset in industries such as aerospace and biomedical.
- Sintering Techniques: Enhanced sintering processes further promote structural integrity and uniformity in the materials produced.
Moreover, with the onset of incorporating nanotechnology, researchers are examining how nanoscale particles can be used to enhance the thermal and mechanical properties of copper foams. This could lead to the development of foams that are not only lightweight but also have superior thermal conductivity.
Innovative Applications Under Investigation
As the research into copper foams progresses, several innovative applications are under investigation, highlighting their versatility.
- Energy Efficiency Technologies: Ongoing studies focus on utilizing copper foams in thermal management systems. Their high thermal conductivity makes them ideal for heat sinks in electronic devices, potentially revolutionizing cooling systems in high-performance environments.
- Biomedicine: The use of copper foams in medical implants is gaining ground. Their porous structure may facilitate tissue ingrowth, promoting better integration with the body. Research is also looking at their antimicrobial properties, which could reduce infection rates in surgical settings.
- Green Technologies: Copper foams are being considered for their role in catalyst support for fuel cells, thereby contributing to cleaner energy solutions.
- Acoustic Applications: Emerging studies are exploring the use of copper foams for sound dampening materials in vehicles and buildings, providing a dual benefit of aesthetic enhancement and functional noise reduction.
"The continued exploration of applications beyond traditional uses is crucial for unlocking the complete potential of copper foams in modern technology."
Future Perspectives on Copper Foams
As the world moves toward sustainability and innovative materials, copper foams are carving out a niche that deserves attention. The future of copper foams not only encompasses the ongoing refinement of their properties and applications but also the broader implications related to market dynamics and potential breakthrough discoveries. This section explores critical elements regarding economic trends and the unexplored fields where copper foams might thrive.
Market Trends
Current market trends are painting a promising future for copper foams. The demand for lightweight yet strong materials in sectors like aerospace, automotive, and electronics is on the rise. As businesses seek greener solutions, copper foams, with their recycling potential, are appealing for new product developments.
Some of the significant trends include:
- Sustainability Demand: There is a growing consumer preference for environmentally friendly products. The intrinsic recyclability of copper foams aligns with this trend.
- Growth in Energy Storage Solutions: As the demand for batteries and supercapacitors surges, copper foams offer a pathway to more efficient energy storage systems.
- Technological Advancements: Innovations in manufacturing techniques are broadening the scope of applications for copper foams, driving further market expansion.
Moreover, the competitive landscape is evolving, with startups and established companies racing to pioneer new applications for copper foams. The interplay between innovation and market demand indicates strong growth potential in upcoming years.
Potential for New Discoveries
Looking ahead, the potential for new discoveries in copper foams is vast and varied. Ongoing research continues to uncover unique properties and applications that could revolutionize industries.
For instance, researchers are investigating:
- Customizable Foam Structures: Tailoring the porosity and structure of copper foams may lead to specific applications in fields like medicine, where controlled release systems can be developed.
- Advanced Antimicrobial Properties: With copper noted for its antimicrobial benefits, there's potential for developing enhanced coatings or materials that utilize copper foams for health-related applications.
- Integration with Renewable Technologies: The interaction of copper foams within fuel cells and other renewable energy technologies is a subject ripe for exploration.
"The landscape of copper foam research is rapidly evolving, with its implications reaching far beyond initial applications. The possibilities are virtually limitless."
Ending
The significance of copper foams in contemporary material science cannot be overstated. With their unique properties and diverse applications, copper foams represent a cutting-edge frontier poised to impact various industrial and scientific domains. Through this article, we have gathered a wealth of information that underscores the intricate composition and versatile nature of copper foams.
One of the primary benefits discussed is their excellent thermal and electrical conductivity. This is key in applications like batteries and supercapacitors, where efficient energy transfer is crucial. Additionally, the lightweight characteristics combined with mechanical strength make them ideal for use in structural applications, such as lightweight heat exchangers.
"Copper foams not only enhance functionality but also pave the way for sustainable solutions in energy management and other fields."
In our exploration of environmental considerations, we highlighted the sustainability of copper as a material and its recyclability, which is particularly relevant in an age where environmental impacts are critically evaluated. As industries seek to reduce their carbon footprint, copper foams hold promise as a material that fosters both innovation and eco-friendliness.
The ongoing research trends suggest a vibrant future for this material as well. From advances in manufacturing techniques to innovative applications, the potential for new discoveries seems vast. Understanding these trends is essential for students, researchers, educators, and professionals who aim to stay ahead in a rapidly evolving field.
Ultimately, as we look to the future, the versatility and promise of copper foams signal a shift towards more advanced materials that not only meet current demands but also anticipate future needs, ensuring their relevance in various applications. The insights provided in this article not only enlighten but also serve as a foundation upon which future explorations can be built, inviting a closer look at how we can optimize the use of copper foams in real-world scenarios.