Comprehensive Guide to Finned Tube Heat Exchangers
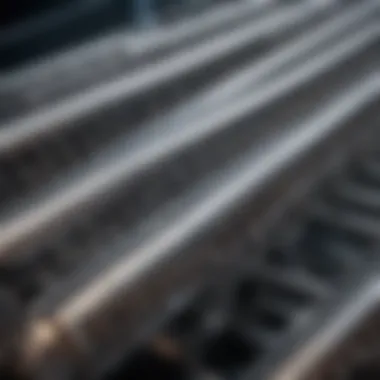
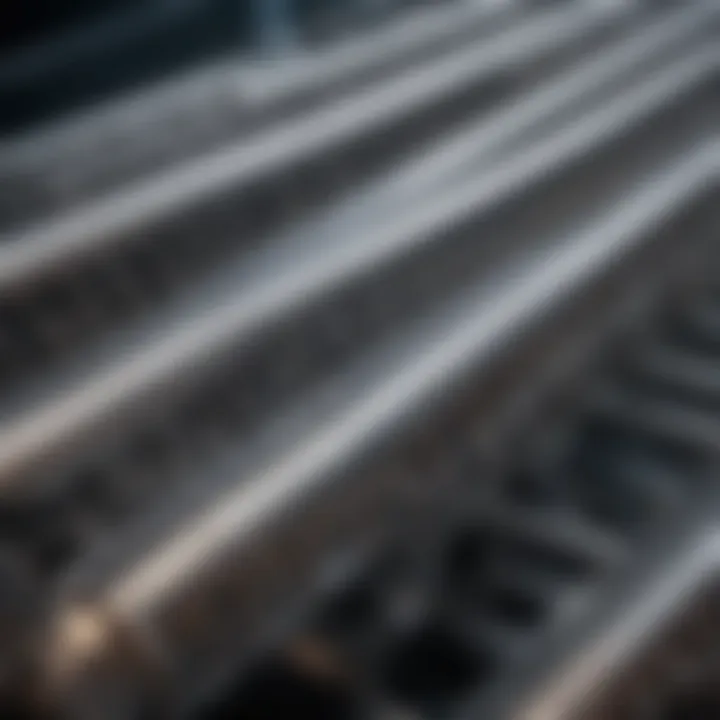
Intro
Finned tube cross flow heat exchangers are integral components in various thermal management systems. Their ability to efficiently transfer heat makes them valuable in applications across multiple industries, from power generation to HVAC. Understanding their design and operational mechanics is crucial for engineers and researchers who aim to enhance efficiency and effectiveness in heat transfer processes.
The structure of finned tube cross flow heat exchangers significantly impacts performance. By increasing the surface area for heat exchange, fins improve the heat transfer rate, making these systems stand out compared to traditional heat exchangers. Examining their design principles, operational mechanics, and applications will lay the groundwork for understanding their role in energy management.
The following sections present a comprehensive analysis of finned tube cross flow heat exchangers, emphasizing their benefits, limitations, and maintenance requirements. This article is designed to provide insights for professionals engaged in thermal management, equipping them with the knowledge to optimize heat exchanger performance in various settings.
Prologue to Heat Exchangers
Heat exchangers are pivotal components in numerous industrial applications. Their primary function is to transfer heat between two or more fluids, which can be essential for processes like heating, cooling, and energy recovery. Understanding heat exchangers, especially finned tube cross flow heat exchangers, is crucial for optimizing thermal systems in various industries.
Definition and Functionality
A heat exchanger is a device designed to efficiently transfer heat from one medium to another, often without mixing the two fluids. This functionality is critical in catering to energy needs while maintaining the desired temperature of processes. The effectiveness of these devices can greatly influence energy consumption. Properly designed heat exchangers help to reduce energy costs and environmental impact, thus becoming increasingly important in today's world.
Types of Heat Exchangers
Heat exchangers come in various forms, each suited for specific applications. The most common types include:
- Shell and Tube Heat Exchangers: These consist of a series of tubes, one set containing the hot fluid while the other holds the cold fluid. Its design is advantageous in applications requiring high-pressure operations.
- Plate Heat Exchangers: Made up of numerous thin plates stacked together, this type is known for its compact design and high efficiency, especially in low to medium pressure scenarios.
- Finned Tube Heat Exchangers: These are characterized by the presence of fins on the tubes, which increase the surface area for heat transfer. Their design maximizes heat exchange between fluids, making them suitable for a variety of thermal processes.
Shell and Tube Heat Exchangers
Shell and tube heat exchangers are widely used in industrial settings due to their resilience and efficiency. These exchangers can handle high pressures and temperatures, which is essential in chemical and petrochemical applications. A key characteristic of shell and tube designs is their ability to be easily cleaned, ensuring operational efficiency.
One unique feature is their modular nature; they can be configured in various ways to suit specific thermal requirements. However, they tend to occupy more space compared to other types, and maintenance can be labor-intensive.
Plate Heat Exchangers
Plate heat exchangers provide a compact solution for heat transfer, making them a popular choice in various industries, including food processing and HVAC. The thin plates increase the surface area, enhancing the heat transfer effectiveness. This design allows for easier maintenance and cleaning, which is a significant advantage.
However, they are more susceptible to fouling in certain conditions, and their pressure handling capacity is limited when compared to shell and tube models. These factors need consideration when selecting a heat exchanger type for specific applications.
Finned Tube Heat Exchangers
Finned tube heat exchangers are designed with extended surface areas due to fins attached to the tubes. This design improves the heat transfer efficiency significantly, crucial in applications where space is a constraint. The finned surface increases contact area, allowing more heat to be transferred within a compact structure.
They are particularly beneficial in air conditioning and refrigeration systems because the fins allow better performance at lower fluid flow rates. Nonetheless, a potential drawback is the increased likelihood of fouling due to the complex geometry, which can lead to maintenance challenges.
Overall, understanding these types of heat exchangers and their respective benefits and drawbacks is crucial. Each type handles heat transfer differently, with varying efficiencies and applications in modern thermal management systems.
Principles of Cross Flow Heat Exchange
The dynamics of heat exchange are vital to the effective operation of finned tube cross flow heat exchangers. Understanding these principles allows engineers and operators to design systems that optimize efficiency and performance. The study of cross flow mechanics uncovers various pathways of thermal interaction and conveys the importance of optimizing these interactions for better energy transfer.
The Concept of Cross Flow
Cross flow refers to the configuration where two fluids move perpendicularly to each other. In finned tube heat exchangers, one fluid typically flows inside the tubes while the other flows across the tubes. This arrangement promotes effective thermal transfer as it enhances the mixing of the fluid, thus improving energy exchange efficiency. Cross flow designs tend to require less space than parallel flow designs, making them suitable for applications where space is limited.
The effectiveness of heat exchange in cross flow systems stems from the turbulent flow that increases heat transfer rates. This turbulence leads to more uniform temperature distributions as the fluids interact with one another, ultimately allowing for higher temperatures to be achieved with lower energy inputs.
Heat Transfer Mechanisms
Heat transfer in finned tube cross flow heat exchangers can be categorized primarily into three mechanisms: conduction, convection, and radiation. Each plays a distinct role in the overall heat transfer process.
Conduction
Conduction is the process where heat is transferred through a material without any movement of the material itself. In the context of finned tube heat exchangers, this occurs as heat moves through the walls of the tubes from one fluid to another. The key characteristic of conduction is its efficiency in solids; metals with high thermal conductivity, like copper or aluminum, are often choice materials for the tubes.
The benefit of conduction in this system is that it facilitates rapid heat transfer between the fluids across the tube walls. However, it is limited to the surface area of the tube and can reach a saturation point. This highlights the need for an adequate design to maximize surface area exposure, which can be enhanced by using fins.
Convection
Convection involves the transfer of heat through the movement of fluids. In finned tube heat exchangers, this occurs both inside the tubes and across the external finned surface. The leading characteristic of convection is that it combines the effects of conduction and fluid dynamics. This makes it particularly effective in heat exchangers, where the flow characteristics of the fluid can significantly alter the exchange rate.
Convection is a beneficial choice for finned tube systems because it capitalizes on the movement and mixing of fluids to enhance heat transfer. The unique feature of forced convection, where a pump encourages fluid movement, can lead to improved thermal efficiency. However, it depends heavily on the velocity of the fluid and the design of the heat exchanger, which must be optimized.
Radiation
Radiation is the transfer of energy through electromagnetic waves. In heat exchanger systems, it is the less significant contributor to the overall heat exchange compared to conduction and convection, especially for liquids. The key characteristic of radiation is that it does not require a medium, as heat can be transferred through vacuum spaces.
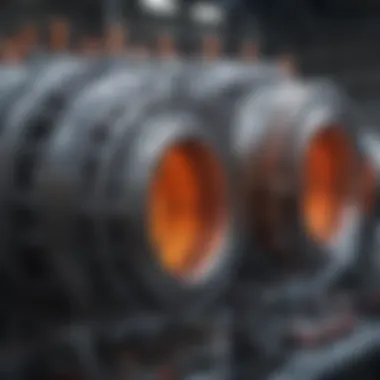
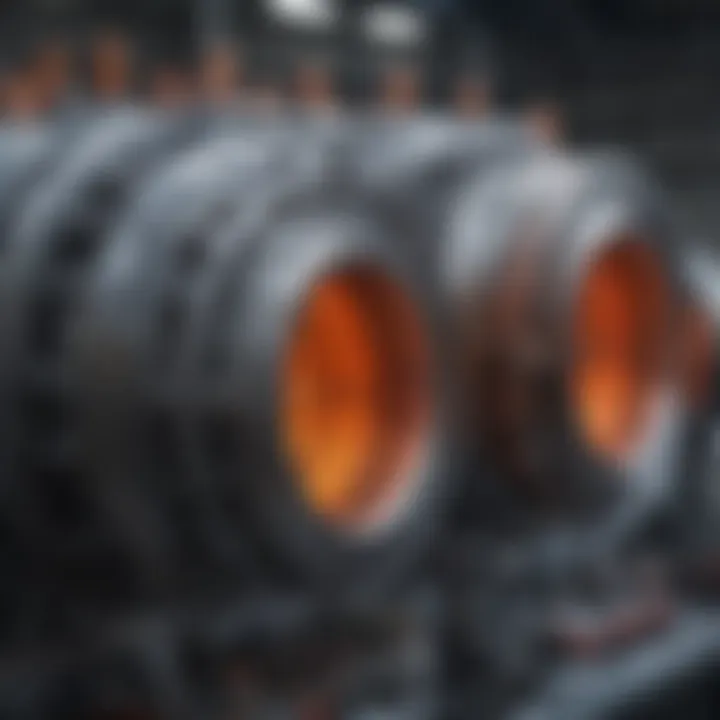
While radiation is usually not the main mechanism at work in finned tube heat exchangers, it becomes relevant in high-temperature operations where radiant heat can play a role. The advantage here lies in its ability to transfer heat across a distance without direct contact, but it typically poses challenges in terms of managing heat loss and maintaining efficiency.
Understanding these mechanisms allows for more informed decisions in design and application, enhancing the overall effectiveness of heat exchangers.
Each of these mechanisms contributes to the overall functioning of finned tube cross flow heat exchangers, underscoring the necessity of careful design to exploit their full potential.
Design of Finned Tube Heat Exchangers
The design of finned tube heat exchangers is pivotal to maximizing their efficiency in thermal management applications. Engineers must focus on multiple factors, such as geometric considerations and material selection, to enhance operational performance. The design's complexity lies in balancing heat transfer effectiveness and structural integrity while addressing specific operational needs. Understanding the nuances of design fosters better performance outcomes and helps to mitigate potential operational challenges.
Geometric Considerations
Tube Patterns
Tube patterns refer to how the tubes are arranged in the heat exchanger. The influence of tube patterns on the overall heat transfer capability cannot be understated. Choosing efficient patterns like staggered or triangular arrangements can promote better fluid flow and increased surface area for heat exchange. This allows for a more optimal temperature gradient to be maintained across the tubes, enhancing the heat transfer process significantly. A major characteristic of these patterns is their ability to manage dead zones or stagnant fluid, which can lead to inefficiencies. While staggered patterns offer increased heat transfer efficiency, they may introduce complexities in cleaning and maintenance due to the intricacies in arrangement.
Fin Orientation
Fin orientation plays a critical role in maximizing heat dissipation. Typically, fins could be horizontal or vertical, which directly affect airflow and thermal performance. A well-designed fin orientation can guide airflow effectively, enhancing the convective heat transfer coefficient. The key advantage lies in improved space utilization. However, if not optimized, fin orientation could lead to uneven heating and localized thermal inefficiencies. Each orientation presents distinct benefits, making this aspect important to address in the design phase.
Spacing and Dimensional Ratios
Spacing and dimensional ratios refer to the distance between fins and the dimensions of tubes in the heat exchanger. This aspect directly influences the heat transfer surface area and fluid flow dynamics. A well-thought-out spacing can prevent fouling, which is a crucial factor in maintaining efficiency. In many designs, tighter spacing is seen as beneficial due to the increased surface area; however, risks of fouling can increase too. Therefore, designers must strike a balance. Evaluating the application requirements will help determine optimal dimensional ratios.
Material Selection
Material selection impacts durability, cost, and thermal efficiency in finned tube heat exchangers. Choosing appropriate materials ensures that the exchanger can withstand the operational environment, enhancing lifespan and performance. Factors such as corrosion resistance, thermal conductivity, and mechanical strength are paramount in this selection.
Corrosion Resistance
Corrosion resistance is crucial for extending the life of finned tube heat exchangers. Materials with high corrosion resistance like stainless steel or specialized alloys are often selected. The resistance to corrosive elements significantly helps in maintaining structural integrity. This choice becomes pivotal when the heat exchangers are installed in abrasive or chemically aggressive environments. On the downside, selecting high-performance materials can lead to higher initial costs.
Thermal Conductivity
The thermal conductivity of materials selected for heat exchangers is essential for efficient heat transfer. Materials like copper and aluminum, known for their high conductivity, enable effective thermal performance. The key characteristic here is the ability of these materials to quickly absorb and transfer heat between the two fluids. However, thermal efficiency must be balanced with cost and weight considerations. For instance, while copper offers superior thermal conductivity, it's often more expensive than alternatives.
Mechanical Strength
Mechanical strength is another vital element in material selection. The heat exchangers are subject to various stresses during operation, including temperature fluctuations and pressure variances. Selecting materials with high mechanical strength ensures that they can withstand these conditions without failure. Steel is commonly chosen for its robustness, but it may increase the overall weight of the system. The focus should be on ensuring that chosen material meets the design and operational requirements without compromising on safety.
The design of finned tube heat exchangers must prioritize efficiency and durability through careful consideration of geometric arrangements and material properties to achieve optimal performance.
Thermal Performance Analysis
Thermal performance analysis is crucial in the context of finned tube cross flow heat exchangers. Understanding how these systems transfer heat is essential for optimizing efficiency and effectiveness in their applications. This section will go into detail on the overall heat transfer coefficient and the effectiveness-NTU method, two key elements in assessing thermal performance.
Overall Heat Transfer Coefficient
The overall heat transfer coefficient represents the efficiency with which heat is transferred between two fluids in a heat exchanger. It is affected by several factors, including the thermal conductivity of the materials involved, the flow arrangement, and the type of heat transfer surface, such as fins in finned tube heat exchangers.
This coefficient can be viewed as an aggregate measure that includes the contributions from conduction, convection, and sometimes radiation. Each of these thermal resistance components should be minimized to ensure optimal heat transfer. Understanding the overall heat transfer coefficient is important because it directly influences the design and analysis of heat exchangers.
- Key Factors Influencing the Overall Heat Transfer Coefficient:
- Material Properties: The thermal conductivity of the materials used in construction impacts the rate of heat transfer.
- Flow Configuration: Cross flow arrangements enhance mixing, improving convective heat transfer.
- Surface Area: The area available for heat transfer is significantly increased by using fins.
It’s essential for engineers to calculate this coefficient accurately to design systems that function effectively under various operating conditions. A high overall heat transfer coefficient indicates a well-functioning heat exchanger that can manage thermal loads efficiently.
Effectiveness-NTU Method
The effectiveness-NTU method is an analytical approach used to evaluate the performance of heat exchangers. Here, effectiveness is defined as the ratio of the actual heat transfer to the maximum possible heat transfer. It provides a measure of how effectively a heat exchanger performs relative to the maximum potential. The number of transfer units (NTU) is a dimensionless quantity representing how well heat is exchanged between the fluids.
This method is especially useful for complex systems where precise calculations may be challenging. The relationship between effectiveness and NTU allows engineers to assess the performance characteristics without needing to know the exact inlet and outlet temperatures of the fluids.
- Benefits of Effectiveness-NTU Method:
- Simplicity: It simplifies the analysis of heat exchanger behavior under different operating conditions.
- Versatility: It can be used for both counterflow and crossflow configurations, making it adaptable.
- Design Guidance: It offers insights that can guide design decisions, helping to optimize thermal performance.
Applications of Finned Tube Cross Flow Heat Exchangers
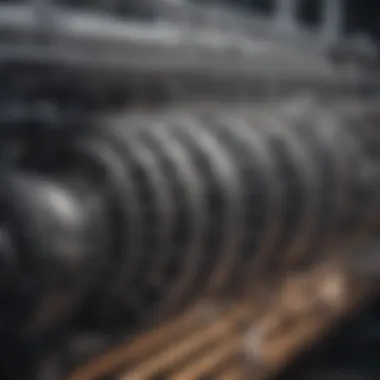
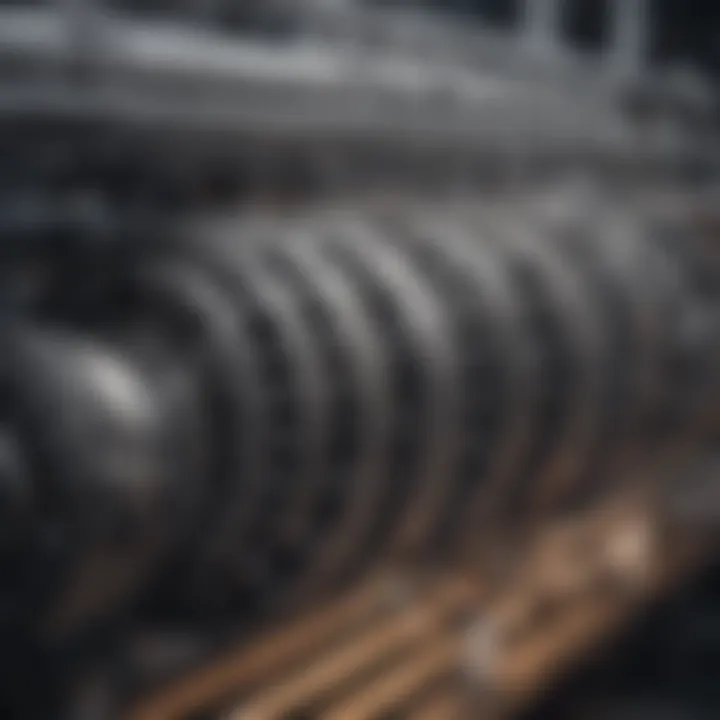
Finned tube cross flow heat exchangers are critical in a wide array of thermal management scenarios. Their versatile applications show their adaptability and efficiency in many industries. Understanding these applications proves useful for professionals and researchers who are exploring cost-effective and high-performance heat transfer solutions.
Industrial Uses
HVAC Systems
HVAC systems are essential in maintaining controlled indoor climate conditions. Finned tube cross flow heat exchangers enhance heat transfer in these systems, ensuring efficient operation. The important characteristic of HVAC systems is their ability to regulate temperature and humidity levels effectively. This capability makes them suitable for residential, commercial, and industrial applications.
The unique feature of HVAC systems using finned tubes is their capacity to optimize airflow around the heat exchanger surfaces. This results in improved thermal performance. One advantage of using finned tube designs in HVAC is reduced energy consumption. However, a disadvantage can be the potential for dust buildup, which may require regular cleaning and maintenance.
Power Generation
Power generation relies on efficient thermal management to optimize energy output. Finned tube cross flow heat exchangers play a significant role in this process. Their key characteristic is the enhanced heat transfer efficiency, which directly impacts energy conversion rates.
For power generation facilities, the unique feature of finned tube exchangers is their ability to handle high pressure and temperature. This leads to better performance in steam cycles and other processes. The advantages include higher efficiency and sustainability of energy production. However, the design complexity can lead to increased initial costs, which should be considered in economic evaluations.
Process Industries
In process industries, such as chemical manufacturing and oil refining, precise temperature control is vital. Finned tube cross flow heat exchangers are utilized for heating and cooling tasks. The primary characteristic here is their durability in harsh operating conditions.
A unique feature of using finned tube heat exchangers in these industries is their capability to manage viscous fluids effectively. This can enhance the overall efficiency of the processes involved. The benefits include consistent product quality and reduced energy costs. On the downside, installation can be complex, which may lead to increased expenditures.
Emerging Applications
Renewable Energy Systems
Renewable energy systems are increasingly employing finned tube cross flow heat exchangers for their effective heat transfer capabilities. Their importance lies in promoting energy sustainability and reducing reliance on fossil fuels. A key characteristic of these systems is their eco-friendly nature.
The unique feature of renewable energy applications is their adaptability to various energy sources, such as solar and geothermal. This versatility allows for better integration into existing infrastructure. One significant advantage is the reduction in greenhouse gas emissions compared to conventional energy systems. However, variations in performance based on environmental factors can pose challenges.
Data Centers
Data centers face high cooling demands due to their continuous operation of servers. Finned tube cross flow heat exchangers are employed to efficiently manage this heat. Their critical role here is maintaining optimal temperatures to ensure reliable functioning of IT equipment.
A distinct feature of finned tube designs in data centers is the ability to provide high capacity cooling in a compact form factor. This makes them suitable for spaces where real estate is limited. The advantages include enhanced cooling performance and energy efficiency. Nonetheless, maintaining clean fins becomes crucial to preserve efficiency, adding to the operational responsibilities of data center management.
Advantages of Finned Tube Designs
Finned tube designs offer significant benefits, particularly in the context of heat exchangers. These advantages are critical for engineers and researchers aiming to optimize thermal management systems across various applications. A comprehensive understanding of these benefits can lead to improved efficiency and cost-effectiveness in heat transfer operations, emphasizing their importance in the larger discussion of heat exchanger technologies.
Improved Heat Transfer Efficiency
One of the primary advantages of finned tube heat exchangers is their ability to enhance heat transfer efficiency. The fins increase the surface area available for heat exchange, facilitating greater heat transfer between the tube and the surrounding medium. This is particularly valuable in applications where space is limited and maximizing heat exchange is essential.
Moreover, the design allows for several configurations of fin shapes, sizes, and materials, which can be tailored according to the specific requirements of the application. For instance, using extended surface fins can augment the convective heat transfer coefficient, resulting in improved overall performance.
This increased efficiency directly translates to energy savings and can lead to reduced operational costs. Additionally, in many industrial applications, the superior heat transfer performance means smaller equipment sizes, which can save space and material costs.
Compact Design
Finned tube heat exchangers also feature a compact design that is advantageous in several respects. Their ability to provide effective thermal transfer in a smaller footprint can be crucial in industries where real estate and installation space are at a premium. This compactness allows for a more efficient layout in heating, ventilation, and air conditioning (HVAC) systems, power plants, and various process industries.
The streamlined design allows for easier integration into existing systems without needing significant modifications. Space-saving benefits also enhance scalability, making it easier for manufacturers to accommodate increased production demands without expanding their facility significantly.
"Optimizing heat exchange efficiency while minimizing space usage is key in modern industrial applications. Finned tube designs excel in both respects."
By understanding these advantages, stakeholders can make more informed decisions regarding the design and implementation of thermal management systems.
Limitations of Finned Tube Cross Flow Heat Exchangers
Finned tube cross flow heat exchangers are known for their efficiency and versatile applications. However, they also have specific limitations that warrant attention. Understanding these limitations is crucial for engineers and designers when choosing the right heat exchanger for a particular application. It helps to minimize inefficiencies that may arise during operation. In this section, we will explore two primary limitations: the potential for fouling and cost implications.
Potential for Fouling
Fouling is a significant issue in heat exchangers, including finned tube designs. It refers to the accumulation of unwanted materials on heat transfer surfaces. This can include dust, algae, corrosion products, and other deposits. As fouling builds up, it creates a barrier that reduces the effective heat transfer area. This can lead to a decline in thermal performance and require more frequent maintenance interventions to clean the surfaces.
When fouling occurs in a finned tube cross flow heat exchanger, several aspects are affected:
- Reduced Efficiency: The heat transfer rate decreases, which may lead to less efficient energy use.
- Increased Energy Costs: As the exchanger becomes less effective, pumps may need to work harder, raising operational costs.
- Maintenance Challenges: Cleaning fouled surfaces can be labor-intensive and might require the unit to be shut down, impacting productivity.

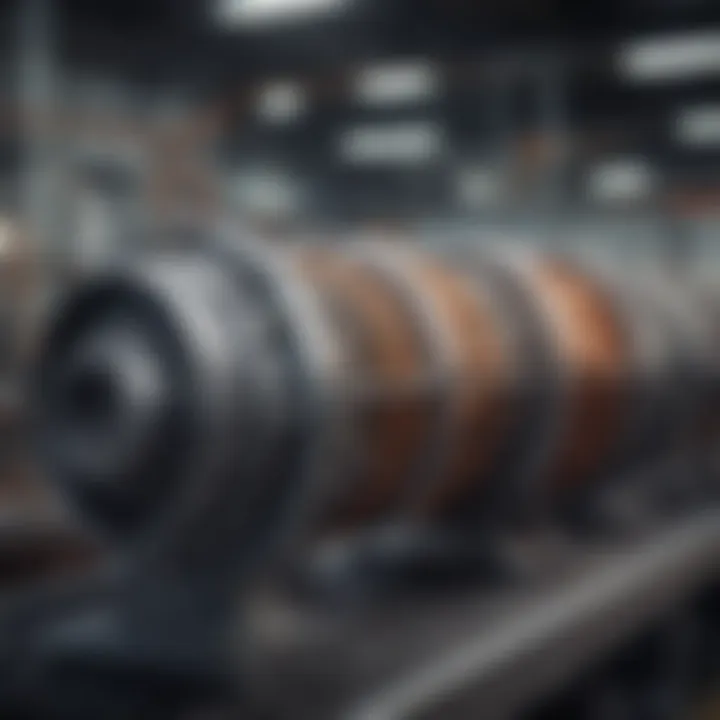
Regular monitoring is essential to detect fouling early. Using filtration systems can help mitigate the buildup of contaminants. In some cases, the use of coatings or specific material choices can also reduce fouling tendencies.
Cost Implications
The cost associated with finned tube cross flow heat exchangers can be both direct and indirect. Understanding these cost elements is essential for making informed decisions regarding their implementation.
- Initial Investment: The upfront costs of finned tube designs can be higher compared to other heat exchanger types. This is due to the complexity of the design and the materials used.
- Maintenance Costs: As mentioned before, maintenance is crucial. The costs associated with regular cleaning, parts replacement, and potential downtime can add up.
- Operational Expenditures: If fouling or inefficiencies occur, it leads to increased energy consumption. This can significantly elevate operating costs over time.
- Long-Term Performance: While finned tube heat exchangers can offer improved efficiency when clean, their long-term performance can be impacted by fouling, leading to potentially higher lifecycle costs.
Ultimately, when contemplating the use of these heat exchangers, it is essential to weigh these limitations against their benefits.
Maintenance and Operational Considerations
The maintenance and operational considerations of finned tube cross flow heat exchangers are essential for ensuring their longevity and optimal performance. These aspects not only contribute to the efficiency of the heat exchanger but also play a significant role in safety and reliability. Regular maintenance helps to prevent unexpected breakdowns and prolongs the life of the equipment.
Regular Maintenance Protocols
Regular maintenance protocols should include inspection and cleaning schedules designed for the specific operating conditions of finned tube heat exchangers. High fouling rates in certain industries may require more frequent cleaning. Also, inspecting for leaks or corrosion are vital operations. These steps help to verify that the heat exchanger is functioning at optimal levels. Inadequate maintenance can lead to reduced heat transfer efficiency and increased energy costs.
Here are some key practices in maintenance:
- Routine Inspections: Conduct regular checks to identify signs of wear and tear early.
- Cleaning Regimes: Employ appropriate cleaning methods such as chemical cleaning or physical brushing to remove deposits.
- Leak Testing: Implement protocols to test for leaks, ensuring that the integrity of system is maintained.
Performance Monitoring Techniques
Performance monitoring techniques play a critical role in assessing the functionality of finned tube heat exchangers. These techniques help operators to evaluate the heat exchange efficiency and identify potential issues that require immediate attention.
Temperature Measurements
Temperature measurements serve as a key indicator of the heat exchanger's performance. These measurements help in monitoring input and output temperatures. They provide essential data for the calculation of heat transfer rates, which is central to assessing efficiency. Accurate temperature measurements are beneficial because they are relatively easy to implement and offer real-time data.
- Key Characteristic: Temperature measurements are done using thermocouples or infrared sensors.
- Advantages: They provide a clear indication of thermal performance and help pinpoint areas needing maintenance.
- Disadvantages: However, reliance on a single point measurement can miss temperature variations across the system.
Pressure Drop Assessments
Pressure drop assessments are another important monitoring technique. They provide insights into the flow characteristics within the heat exchanger. A significant increase in pressure drop can indicate fouling or other operational issues that may need addressing.
- Key Characteristic: The pressure drop is measured across specific sections of the heat exchanger.
- Advantages: It provides a direct assessment of flow resistance and efficiency of the system.
- Disadvantages: Additionally, pressure drop assessments can sometimes require complex calculations and may not always indicate the cause of inefficiencies.
Future Trends in Heat Exchanger Technology
Heat exchangers are critical components in many industries, from HVAC to process engineering. Understanding future trends in heat exchanger technology is vital for progress. As research and development advance, several specific elements emerge which could reshape design and function.
Innovations in Materials
Innovative materials are changing the landscape of heat exchanger design. Traditional materials like carbon steel and copper are being enhanced or replaced with alternatives that have better thermal properties or durability. For instance, titanium and high-grade stainless steels offer improved corrosion resistance.
Additionally, aluminum alloys present excellent thermal conductivity and lightweight characteristics. The choice of materials is not just about performance. It also affects the overall lifecycle cost and environmental impact. As technology evolves, recyclable and more sustainable materials gain precedence.
"The selection of advanced materials can enhance energy efficiency, leading to operational cost savings over time."
Smart Heat Exchangers
Smart technology integration presents an exciting trend in heat exchanger systems. Incorporating sensors and IoT (Internet of Things) connectivity allows real-time monitoring of performance. These systems can analyze data, optimize flow rates, and adjust operational parameters. Thus, smart heat exchangers can alleviate issues like overheating or inefficient energy use.
Furthermore, predictive maintenance strategies can be deployed. These reduce downtime and ensure longevity of systems.
The benefits of smart technology extend beyond monitoring. They support energy conservation efforts, aligning with global trends toward increased efficiency and reduced carbon footprints. As more companies recognize the financial benefits, the adoption of smart heat exchangers will likely expand.
Ending
The conclusion section of this article serves as a pivotal segment that distills the extensive examination of finned tube cross flow heat exchangers. Highlighting the essence of this topic is crucial since it consolidates the insights drawn from various sections. In doing so, it allows engineers, researchers, and industry professionals to reflect on the significance of the discussed concepts.
Recap of Key Insights
As we reflect on the main points from the article, several critical insights emerge. The design characteristics of finned tube cross flow heat exchangers, such as geometric considerations and material selection, play a vital role in their thermal performance. A recurring theme is the emphasis on maximizing heat transfer efficiency while minimizing potential fouling risks.
In addition, the comprehensive application spectrum demonstrates their relevance across multiple sectors, including HVAC systems, power generation, and renewable energy. Understanding the limitations, whether they be associated costs or maintenance challenges, illuminates the path for more informed decision-making among practitioners.
Implications for Future Research
The landscape of heat exchanger technology is evolving, and future research must address ongoing challenges and explore innovative solutions. This includes investigating advanced materials that offer improved thermal conductivity and corrosion resistance. Additionally, as the industry moves towards smart technologies, engaging in studies that integrate IoT for real-time monitoring will be essential. Future research could also focus on the optimization of designs to enhance efficiency and reduce operational costs further. Such explorations will not only keep pace with technological advancements but also align with global sustainability goals.
"The integration of innovative materials and smart technology will shape the future of finned tube heat exchangers, leading to improved performance and sustainability."
In summary, the conclusion encapsulates the essence of finned tube cross flow heat exchangers, emphasizing their critical role in thermal management solutions across various industries. It supports the notion that continued exploration and study in this field are necessary for sustained advancements.