The Role and Mechanics of Fractionation Columns
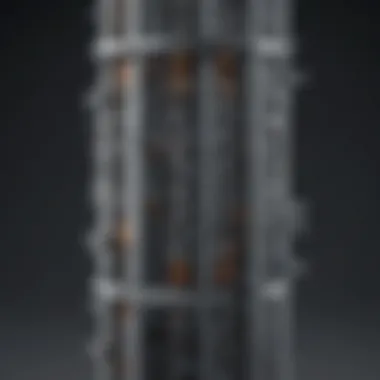
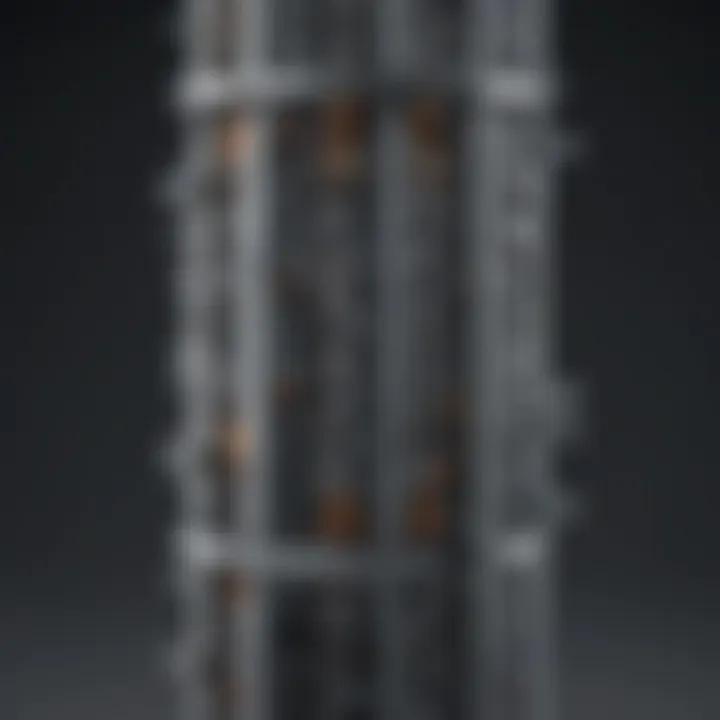
Intro
Fractionation columns are at the heart of many scientific processes, acting like the unsung heroes behind the scenes. They allow for the separation of complex mixtures into their distinct components, an essential task in both chemistry and biotechnology. But what really goes on in these tall, cylindrical structures? One could think of them as the intricate spiderwebs that catch the elusive molecules we seek to separate. Understanding how they operate is not just a matter of theoretical knowledge; it's about grasping their relevance in scientific research and industrial applications.
In the simplest terms, a fractionation column helps to separate substances based on varying physical or chemical properties, such as boiling points. This essential separation allows chemists and engineers to isolate desired compounds for further study or commercial use. Without fractionation columns, scientists would find themselves mired in chaos, unable to pull apart the intricate tapestry of molecules that make up their materials.
By delving into the workings of these columns, one can appreciate their importance beyond just their mechanical function. They’re integral to ensuring purity and precision, impacting everything from pharmaceuticals to environmental monitoring. As we peel back the layers, we will uncover the types of fractionation columns, their design considerations, and the latest advancements that make these devices more efficient than ever.
In this article, we aim to provide a well-rounded look at the process and significance of fractionation columns, ensuring that students, researchers, and professionals alike come away feeling informed and inspired.
Prolusion to Fractionation Columns
Fractionation columns sit at the heart of numerous industrial and laboratory processes. They function as intricate tools designed to separate mixtures based on distinct physical or chemical properties. Understanding their role is pivotal for anyone delving into chemistry or biotechnology fields, where the need for precise separation is often critical for successful outcomes.
First and foremost, the essence of fractionation columns is to streamline operations that involve complex mixtures. Such columns enhance the efficiency of separation processes, saving both time and resources. For example, in the chemical industry, the ability to isolate specific components from mixtures like crude oil can lead directly to valuable products such as gasoline, diesel, or lubricating oils. Simply put, without these fractionation columns, many of the conveniences we take for granted might not exist.
Additionally, the consideration of how these columns function can shed light on broader scientific concepts. By examining fractionation techniques, students and researchers alike can grasp fundamental principles, such as thermodynamics and phase equilibria. This context is invaluable not only in academic pursuit but also in practical applications across various industries.
Definition and Function
To define fractionation columns, they can be understood as vertical structures that facilitate the separation of liquid mixtures into individual components. Deep inside the column, a series of physical processes unfold. These involve vaporization, condensation, and the interaction of different substances within the column structure. The ultimate goal is to exploit the differences in boiling points, vapor pressures, or affinities for a stationary phase, depending on the specific type of column used.
While their construction can vary—some being more complex with packed beds or trays—every fractionation column's function revolves around achieving high separation efficiency. They can handle wide-ranging applications, from purifying chemical products to concentrating valuable compounds in biotechnological processes.
Historical Context
The roots of fractionation columns trace back to the early days of chemical engineering. Their development often mirrored advancements in understanding mixtures and separations methods. The first notable fractionation apparatus is attributed to distillation techniques used by ancient alchemists in search of creating elixirs or purifying substances.
As science progressed, the need for improved methods for separation rose during the industrial revolution. The burgeoning chemical industry laid the groundwork for modern fractionation techniques. Pioneers in the field, such as Robert Boyle and later, the development of fractional distillation, have helped shape our current understanding and methods employed today.
Fast forward to the 20th century, and significant strides in mechanical engineering, materials science, and chemical thermodynamics enabled the fine-tuning of these columns. Today, fractionation columns exist in various forms, each with unique strengths catered to specific applications, reflecting the rich history of a discipline that balances art and science.
Operational Principles of Fractionation
Understanding the operational principles of fractionation is crucial for grasping how fractionation columns work in various applications. These columns play an indispensable role in the separation of substances based on their different properties, allowing researchers and manufacturers to obtain pure components efficiently. The mechanisms behind this process are not just academic; they impact the efficiency, cost, and performance of a wide range of industrial applications.
Basic Mechanism
The fundamental mechanism of fractionation hinges on the idea of equilibrium between phases. When a mixture is introduced into a fractionation column, the components begin to separate based on their relative volatilities. Simply put, substances with lower boiling points will tend to vaporize before those with higher boiling points.
This separation occurs through repeated vaporization and condensation cycles, effectively allowing lighter components to rise through the column while heavier substances remain lower down. The packed sections or plates within the column facilitate these interactions, providing surface area for vapor and liquid phases to contact.
- Vapor Phase Ascendancy: As the mixture heats up, vapors ascend while interacting with the descending liquid.
- Fractional Collection: Collectively, fractions condense at different heights, allowing the operator to withdraw purified materials.
- Repeatability: The process can be repeated, increasing purity levels with each cycle.
Understanding these elements helps in configuring columns for different substances and further provides insights into how to optimize separation by adjusting temperature and pressure.
Thermodynamic Aspects
Delving deeper, the thermodynamic considerations are pivotal for the efficiency of fractionation processes. At the heart of this lies the concept of relative volatility, which defines how easily a component can transition from liquid to vapor compared to others in the mixture.
Thermodynamic principles dictate the following factors:
- Temperature Gradient: A carefully controlled temperature gradient is essential. It ensures that heavier components are sufficiently cooled to remain liquid while lighter components can vaporize.
- Pressure Impact: Adjusting the pressure within the column can enhance the separation efficiency. Higher pressures may lead to increased boiling points, thus affecting the volatility of components.
- Enthalpy and Heat Transfer: The heat transfer through the column not only affects separation but also implicates energy consumption. Striking the right balance is fundamental for economic viability.
A well-designed fractionation process is a dance of thermodynamics; every move must be calculated to ensure purity and efficiency in separations.
By grasping these operational principles and thermodynamic dynamics, professionals can enhance the functionality of fractionation columns, adapt designs to specific separation challenges, and ultimately drive advancements in various scientific and industrial domains.
Types of Fractionation Columns
When diving into the intricacies of fractionation columns, it's essential to understand the different types available. Each kind serves a unique purpose, and knowing their features assists in selecting the right one for specific contexts. The various types can significantly impact efficiency, performance, and outcomes in both laboratory and industrial settings.
Continuous vs. Batch Columns
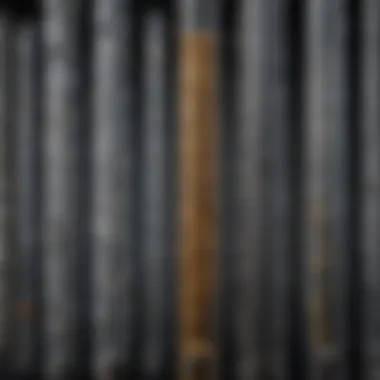
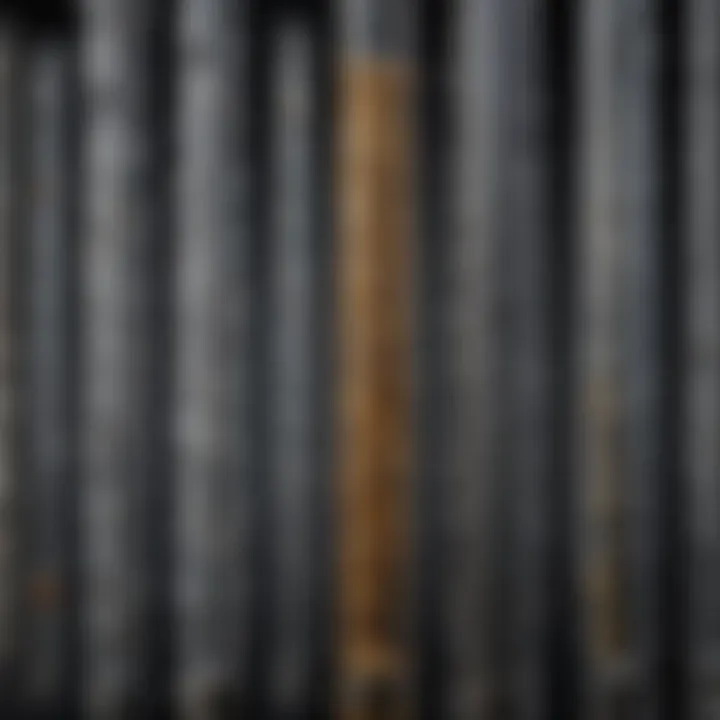
Continuous fractionation columns operate nonstop, allowing for a seamless flow of feed material through the system. This design is particularly advantageous for large-scale processes where constant output is required. For instance, in the petrochemical industry, these columns are indispensable for continuously separating hydrocarbons, thus streamlining production and reducing downtime.
On the other hand, batch columns operate through discrete cycles. The process involves feeding a specific amount of material, then allowing it to undergo separation before cleaning and resetting for the next round. This approach is often favored in smaller-scale operations or when dealing with diverse feedstocks, such as in the pharmaceutical industry where precise control of the separation process is paramount.
Understanding these differences can influence the decision-making process of engineers and scientists working in separation technologies.
Packed Columns
Packed columns are renowned for their efficiency in various applications. These columns contain packing material, which creates a large surface area for vapor-liquid contact. The improved mass transfer capabilities make them ideal for separating components with close boiling points, enhancing the overall separation efficiency.
A prime example is in the production of high-purity ethanol where packed columns help eliminate impurities effectively. The choice of packing material can significantly affect the column's performance, which is why selecting materials with appropriate characteristics for specific processes can yield better results. As such, this type of column remains a staple in both chemical and biotechnological applications due to its adaptability.
Capillary Columns
Capillary columns, with their minute diameters, offer superb separation of volatile components. Commonly found in gas chromatography, they excel in resolving complex mixtures with minimal sample size. The narrow design increases the efficiency of separation due to shorter paths for the analytes to travel.
Moreover, capillary columns can be coated or treated to enhance selectivity, making them indispensable in efforts to analyze environmental samples or in forensic investigations. While their scale might be smaller than other types of columns, their precision and effectiveness should not be underestimated.
Laboratory vs. Industrial Columns
There’s a distinct divide between laboratory columns and industrial columns. The former are typically designed for smaller-scale applications, often allowing for experimentation and method development. They focus heavily on precision and flexibility, accommodating various designs tailored to specific research needs.
Conversely, industrial columns are built for robustness and capacity. They are engineered to handle larger volumes and operate continuously under harsher conditions. For instance, a large chemical plant may implement an industrial column system designed to efficiently separate thousands of liters of product daily. This shift from laboratory to industrial use underscores the scaling challenges often encountered as techniques transition from research to real-world application.
In summary, understanding the types of fractionation columns helps to understand their functional capacities and applications. This knowledge is crucial for students, researchers, and professionals who decide on the best column type for their specific separation needs. Each categorization sheds light on its unique advantages and the considerations one must bear in mind when designing and implementing these systems.
Application Areas
Understanding the application areas of fractionation columns enriches one’s perspective on their utility in diverse scientific and industrial fields. Fractionation columns are not just structures; they are pivotal instruments that drive numerous processes related to the separation of components. Their effectiveness relates directly to the distinct properties of the substances involved, making their understanding fundamental to various practices in chemistry, oil refining, and biotechnology.
Chemical Industry
In the realm of the chemical industry, fractionation columns stand out as a cornerstone for numerous operations. These columns are vital for separating chemical mixtures, which often contain compounds with different boiling points. For example, during the production of ethylene from natural gas liquids, fractionation columns effectively segregate ethane from other hydrocarbons. This separation allows for the production of high-purity chemicals necessary for further synthesis and application.
One of the key benefits within this sector is the improvement in yield and product quality, achieved through efficient separation processes. As raw material costs sometimes fluctuate heavily, ensuring a clean separation can significantly lower costs later on, making the operation more economically viable. Moreover, advancements in automation technologies that integrate AI are being incorporated. This tech helps optimize the fractionation process, reducing human error and fine-tuning operational parameters.
Oil Refining
The oil refining industry also heavily depends on fractionation columns to arrive at various product grades from crude oil. Distillation is one such critical process that begins here. Crude oil has a cocktail of complex hydrocarbons, and the fractionation column breaks it down into fractions—like gasoline, diesel, kerosene, and more—based on boiling point differences. The effectiveness of distillation can determine the quality and quantity of the refined products, which has a cascading effect on pricing and market stability.
Additionally, the operational efficiency of these columns in oil refineries drives energy savings, which can directly affect production costs. Given the massive scale of oil production, even marginal improvements in efficiency can translate into substantial economic benefits. The regulatory landscape focused on emissions further emphasizes the need for these columns to not just be effective but also environmentally conscious.
Biotechnology Processes
In the multifaceted world of biotechnology, fractionation columns play an essential role in the purification of biomolecules. Whether it's isolating proteins from cell cultures or separating plasmids during genetic engineering, these columns exemplify precision in obtaining high-purity product fractions. For instance, in pharmaceutical applications, fractionation can help produce essential drugs by isolating bioactive compounds from natural sources or synthesizing them through fermentation processes.
Moreover, particular methods, such as liquid-liquid extraction, leverage the principles of fractionation to separate biomolecules on a micro or nano scale. With the increasing demand for biopharmaceuticals, the importance of advanced fractionation methods in ensuring quality and yield cannot be overstated. The industry's ongoing research into miniaturization and hybrid column designs reflects an innovative approach aimed at increasing efficiency while reducing the overall footprint and resource consumption.
The significance of fractionation columns across these sectors can’t be understated. Their design and operational efficiency directly correlate to both the cost-effectiveness and quality of the end products.
Design Considerations for Fractionation Columns
Designing an effective fractionation column isn't just a walk in the park; it requires careful thought and consideration of several factors that collectively dictate its performance. The efficiency of separation processes hinges on well-planned design approaches. Several elements come into play here.
Material Selection
The materials used in the construction of fractionation columns directly influence their functionality and durability. The appropriate choice of material involves assessing various factors:
- Chemical Compatibility: The selected material should withstand the chemical environment it will face during operation. For instance, stainless steel is often favored in the chemical industry due to its resistance to corrosion and degradation under aggressive conditions. In contrast, glass columns might be employed when observing reactions is necessary, as they provide visual accessibility.
- Thermal Conductivity: This is crucial, especially when temperature control is necessary for efficient separation. Materials with good thermal properties help maintain optimal thermal gradients, which is vital for maximizing separation efficiency.
- Mechanical Strength: Depending on the application, some columns may be subject to significant pressure. Materials like titanium prove useful in high-pressure applications due to their strength.
- Cost: Economic considerations can’t be overlooked. While some materials might offer superior performance, they may also come with a hefty price tag. Balancing performance and cost is an essential task for designers.
Choosing the right material isn’t merely about preference; it’s about ensuring that the column operates safely and effectively under its specific conditions.
Column Dimensions and Efficiency
When it comes to dimensioning a fractionation column, various aspects need thorough evaluation to guarantee peak performance:
- Height-to-Diameter Ratio: This ratio affects the efficiency of mass transfer. A higher ratio can lead to better separation, but it might also require more materials, increasing costs.
- Tray or Packing Design: The internal design, whether it's trays or packing, significantly impacts performance. Each design type has its unique attributes; trays facilitate larger volume flows, while packing may enhance surface area, thereby increasing contact between vapor and liquid.
- Throughput: Understanding the expected throughput is crucial. If a column is designed for a low throughput but operates at high flow rates, inefficiencies arise, resulting in poor separation.
- Pressure Drop Considerations: The design must minimize pressure drops, as excessive pressure loss can lead to energy inefficiencies and overall operational costs.
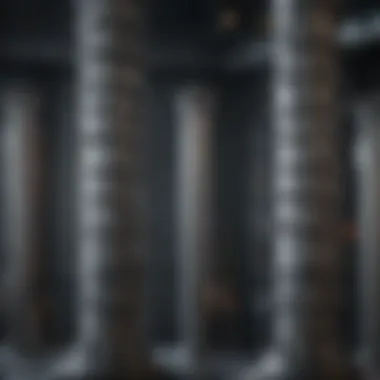
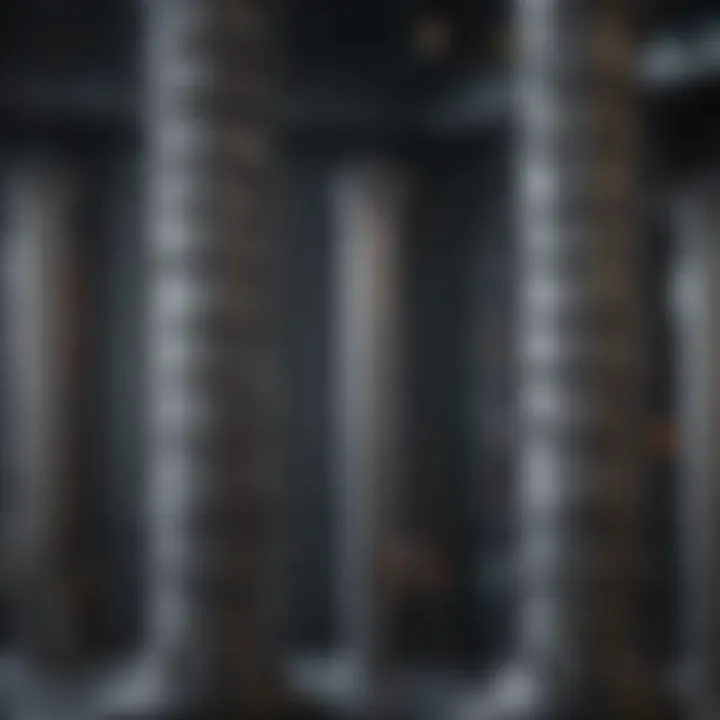
Considering these design elements is paramount. Not only do they impact the operational effectiveness of fractionation columns, but they also correlate with the longevity and sustainability of the processes they support.
Advancements in Fractionation Technology
The field of fractionation technology has seen noteworthy progress over the last few decades. These advancements not only enhance the operational efficiency but also broaden the spectrum of applications for fractionation columns across various industries. Staying abreast of these developments is crucial for researchers and professionals aiming to optimize their processes and improve yield.
High-Throughput Techniques
In the arena of fractionation, high-throughput techniques represent a pivotal shift in how separations are conducted. These methodologies allow for processing larger volumes of samples in a shorter time frame, thereby facilitating rapid experimentation and analysis. For instance, in laboratories where time is of the essence, high-throughput systems permit scientists to conduct numerous experiments in parallel, maximally utilizing available resources.
Key benefits of high-throughput techniques include:
- Increased Efficiency: By using automation and parallel processing, these systems minimize manual intervention. This significantly reduces the chances of errors and improves reproducibility.
- Cost Reduction: Higher throughput means less time is spent on each separation, which can translate to reduced operational costs. Furthermore, using fewer resources for a greater output enhances profitability.
- Innovative Design: Modern high-throughput fractionation columns are designed with enhanced flexibility and modularity. This offers researchers the ability to tailor setups based on their specific needs without significant overhauling of existing equipment.
Nanotechnology in Fractionation
Nanotechnology's infusion into fractionation processes introduces a novel dimension. By manipulating materials at the nanoscale, researchers can profoundly impact the separation efficiency of fractionation columns. For example, nanoparticles can be integrated into the packing material of a column, which enhances surface area, ensures optimal interactions with the substances being separated, and dramatically increases separation performance.
Consider the following implications of utilizing nanotechnology within fractionation:
- Improved Selectivity: Nanoparticles can impart unique properties that enhance the separation process. This enables finer distinctions between components based on their molecular characteristics, thus achieving higher purity levels.
- Enhanced Capacity: The introduction of nanomaterials can augment the capacity of separation columns. This allows for a greater amount of material to be processed without substantial increases in size or energy costs.
- Smaller Footprints: Nanotechnology often leads to a reduction in the size of equipment required. Compact designs not only save space but can also lessen the overall environmental footprint.
- Cost Savings Over Time: Although the initial investment in nanotechnology can be higher, the long-term benefits, including reduced downtime and material waste, can provide significant savings.
"Advancements in nanotechnology can redefine the capabilities of fractionation, opening doors to applications previously deemed impractical."
In summary, the infusion of nanotechnology into fractionation marks a substantial progression. It not only amplifies efficiency but also presents unmatched opportunities for innovation and broader application in areas ranging from pharmaceuticals to biochemical analyses.
Challenges and Limitations
Understanding the challenges and limitations of fractionation columns is critical for anyone involved in processes that hinge on separation techniques. It is not merely about the cutting-edge designs or advancements in technology; it is often these very challenges that dictate the efficiency, scalability, and overall effectiveness of operations in both laboratory and industrial contexts. Failing to recognize these limits can lead to operational bottlenecks, increased costs, and inefficiencies that can ripple through the entire process.
Scaling Up Processes
Scaling up laboratory processes to industrial levels presents its own set of difficulties. In a lab, fractionation columns can be adjusted and optimized for smaller volumes, making it easier to fine-tune parameters like temperature and pressure. However, when transitioning to large-scale production, maintaining the same levels of efficiency becomes a Herculean task. It’s not a simple case of multiplying values; instead, the dynamics change entirely. The increased volume can lead to alterations in heat and mass transfer, creating unforeseen challenges. Factors such as non-ideal flow patterns or discrepancies in temperature profiles can affect separation efficacy.
Moreover, maintaining purity becomes a tightrope walk as throughput increases. Striking a balance between speed and separation quality is essential. As the saying goes, "you can't have your cake and eat it too." Sometimes, brilliance in design might falter when exposed to the unforgiving nature of larger volumes. Understanding these scaling challenges is paramount for researchers who aim to transition successful lab experiments into commercially viable solutions.
Energy Consumption
Another significant limitation of fractionation processes is energy consumption. It is perhaps a reality that is rarely highlighted but impacts the economic viability of fractionation technologies immensely. These processes often consume considerable amounts of energy to maintain the requisite temperatures and pressures. The implications here are two-fold – not only do high energy requirements contribute directly to production costs, they also escalate the carbon footprint associated with such operations.
In fact, energy efficiency is becoming a key point of consideration among researchers and engineers. Many establishments are searching for new methods to enhance energy efficiency in their columns. For example, conducting an energy audit can reveal areas where you might be 'bleeding' energy. Transitioning to more efficient heat exchangers or utilizing waste heat recovery systems could be game changers.
"Energy efficiency often represents the largest single opportunity for both economic and environmental improvement in fractionation processes."
As we navigate the complexities associated with energy consumption, it is crucial to consider advancements in technology, such as real-time monitoring systems and AI applications. These innovations can help monitor energy use and suggest optimizations that can lead to significant savings. However, implementation often requires capital investment, which can hinder adoption.
In summary, both scaling up processes and managing energy consumption pose significant challenges in the realm of fractionation columns. Recognizing and addressing these limitations can pave the way for more sustainable practices and better performance in both laboratory and industrial applications.
Environmental Considerations
In today’s world, the push towards sustainable practices in industrial processes cannot be overstated. Fractionation columns, while essential for separating mixtures in fields such as chemistry and biotechnology, are under scrutiny for their environmental impact. These towers of science often consume substantial amounts of energy and can generate significant waste. Let's delve deeper into why environmental considerations play a critical role in the operation of fractionation columns, examining both the sustainable design efforts and waste management strategies that can mitigate negative effects.
Sustainability in Design and Operation
Sustainability in design and operation of fractionation columns ensures that while achieving effective separation processes, environmental degradation is minimized. Engineers and researchers are constantly trying to make these systems more efficient, tweaking designs that optimize performance while reducing energy consumption.
For instance, the integration of energy recovery systems can drastically cut down the overall energy needs. Instead of relying solely on traditional energy sources, such as natural gas or electricity, systems can be redesigned to capture and reuse energy expelled during separation. This not only lowers operating costs but also lessens the carbon footprint of the operation, addressing both economic and environmental concerns.
Additionally, materials selection plays a vital role. Utilizing environmentally-friendly materials or recyclable components in the construction of these columns can further enhance sustainability. Choosing materials that exhibit longer lifespans through durability can also reduce waste. Also, treating exhaust emissions and operating within stricter environmental guidelines enhances both the ecological footprint and regulatory compliance.
Waste Management Strategies
Another pivotal aspect of environmental considerations revolves around waste management strategies. With the operational processes of fractionation columns yielding by-products, developing effective management strategies is essential to ensure minimal environmental impact.
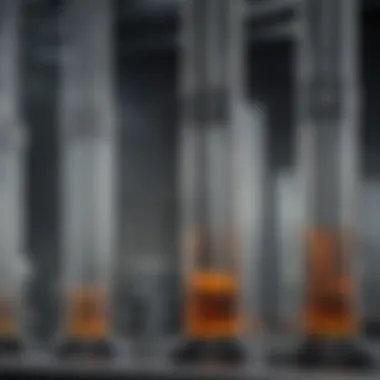
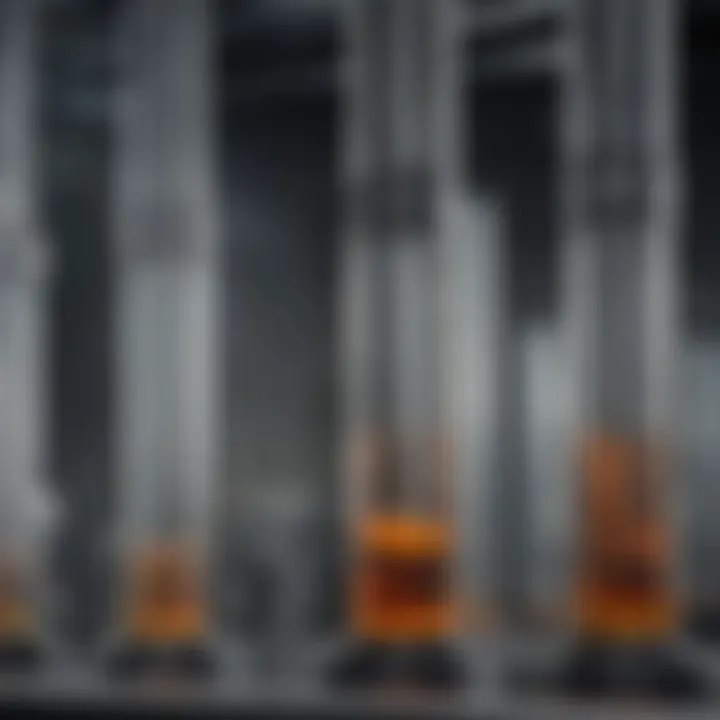
Some key strategies include:
- Zero-Liquid Discharge (ZLD): This method aims to eliminate all liquid waste, ensuring that water and solvent evaporation and condensation processes lead to usable by-products rather than waste.
- Recovery Systems: Implementing systems that can recover solvents or valuable reagents from the waste stream not only prevents environmental pollution but contributes to the economic viability of processes by recapturing costs associated with raw materials.
- Streamlining Processes: By optimizing the separation parameters, operators can reduce the volume of waste generated. For example, adjusting temperatures and pressures in separation processes can maximize efficiency, leading to reduced waste production.
"The shift toward sustainable practices in fractionation operations is not merely an option but increasingly a necessity in the context of environmental accountability."
Economic Implications
The economic implications surrounding fractionation columns are quite substantial, impacting both the financial aspects of industries where they are prevalent, and the broader themes of sustainability and efficiency in operational processes. As these components are pivotal in separating mixtures, it's not just about how effectively they function, but also about how they influence the bottom line of organizations harnessing their capabilities. Understanding the economic facets brings to light considerations that steer decision-making and innovation in fractionation technology.
Cost-Effectiveness of Fractionation Methods
In the realm of separation processes, the cost-effectiveness of various fractionation methods stands out as a critical factor. The investment in such systems often requires a careful balance between upfront costs and long-term savings. Several elements fundamentally affect their economic viability:
- Initial Investment: The price tag on sophisticated fractionation columns can be hefty, especially for high-throughput or specialized designs. However, the choice of materials and scale can greatly determine the starting financial outlay.
- Operational Efficiency: Once installed, the efficiency of a fractionation column can yield significant savings. Notably, systems that minimize energy consumption or reduce waste can provide sponsors with a lasting economic edge. For instance, fractionation columns fitted with energy-recovery units have shown to bring down energy costs dramatically.
- Processing Time: Shorter processing time correlates with lower operating costs, which is why industries seek columns that maximize throughput without compromising separation quality. In this context, more advanced designs can be worth their salt, leading to a faster turnaround, thus improving profit margins.
- Product Quality: Higher purity levels and separation efficiency translate to better-quality end products, which can command higher market prices. Therefore, the correlation between functioning and fiscal performance cannot be understated.
Considering these points can help organizations derive not just immediate financial benefits but can also enhance their competitive stance in the market.
Market Trends in Separation Technologies
As technology evolves, so does the market landscape for separation methods, particularly in fractionation columns. A few notable trends currently shaping the industry include:
- Automation and Control Technologies: The growing utilization of automated systems enhances precision, requiring less manual oversight, and thus reducing human error. Companies leveraging such systems often find they benefit from greater consistency and reduced operational costs.
- Eco-Friendly Materials: As sustainability takes the front seat, there's an increasing pivot towards materials that are more environmentally friendly. This is not only a trend spurred by consumer demand but also one that can yield economic advantages by complying with regulations and reducing waste treatment costs.
- Integration of Machine Learning: Artificial intelligence is being enlisted in monitoring and optimizing processes in real-time, facilitating proactive adjustments. This can lead to lower operational costs and improve resource allocation.
- Globalization of Supply Chains: With industries expanding across borders, the availability of different technologies from a wider array of suppliers is changing dynamics. This globalization promotes competition and can drive prices down, benefitting consumers who seek cost-effective solutions.
Through understanding these trends, stakeholders can better navigate the waters of fractionation technology, making decisions informed by market signals and operational realities.
"The economic landscape of fractionation columns is as dynamic as the technologies they employ, pushing companies to remain adaptive and resource-efficient."
Future Perspectives
As we gaze into the horizon of fractionation technology, it's clear that its potential is anything but exhausted. The dynamics of separation processes are evolving at a pace that’s, frankly, a bit dizzying. With emerging technologies constantly reshaping the landscape, understanding these developments is crucial not just for academics but also for industries relying on separation methodologies. What we can expect in the future hinges largely on innovations that promise not only to enhance efficiency but also to reduce costs and environmental impacts.
Emerging Technologies
The future of fractionation columns is tied closely to several exciting technologies that are making waves. Among these, micro- and nanotechnology are critical game-changers. By miniaturizing systems, researchers can create micro-fractionation columns that significantly improve resolution and performance while using lesser reagents. Imagine a setup that can effectively separate compounds with minimal sample sizes. This can lead to breakthroughs, especially in pharmaceuticals, where precision is everything.
Moreover, membrane distillation seems to be another promising avenue; integrating it into fractionation processes could further enhance purity while minimizing the energy footprint. The flexibility that these technologies offer allows for adaptability in various scenarios, transforming how chemists and biotechnologists think about separation.
Role of AI in Enhancing Fractionation Processes
Artificial intelligence is increasingly creeping into the laboratory and the heart of many industrial processes, and fractionation is no different. The integration of AI algorithms can transform the efficiency of fractionation columns dramatically. For instance, consider predictive maintenance: using machine learning models, operators can anticipate failures in column systems before they occur, significantly reducing downtime.
Additionally, AI can optimize operational parameters, adjusting temperature and pressure in real time for maximum yield. (It doesn’t just stop there; this could pave the way for the creation of self-optimizing fractionation systems, where the algorithm learns from each operation cycle and improves subsequent runs.)
Furthermore, the utilization of AI can streamline data analysis in real-time, allowing researchers to quickly interpret results and adjust methodologies, saving both time and resources. This ripple effect can enhance not just productivity but also the overall sustainability of processes.
The melding of emerging technologies like micro-fractionation and AI into fractionation processes signifies a shift toward more sophisticated and efficient separation methodologies, making them not only smarter but also more environmentally friendly.
In summary, the future of fractionation columns is electrifying. With the infusion of cutting-edge technologies, both emerging and established, there is an unparalleled opportunity to refine separation processes. Understanding these advancements will be pivotal for those in research and industry, defining how we handle the intricacies of materials and chemicals in the years ahead.
Closure
The importance of the concluding segment in this article lies in summarizing the crux of the discussions around fractionation columns and highlighting their multifaceted role. It acts as a bridge, connecting various aspects covered in the article—from the fundamental principles to the applications and future directions. This section encapsulates critical elements such as operational principles, design considerations, and technological advancements, making it essential for readers to grasp the overarching significance of fractionation columns in scientific and industrial realms.
By concluding effectively, readers are reminded that fractionation columns are not merely technical apparatuses; they are pivotal in a variety of processes across numerous fields. Whether in chemical engineering, biotechnology, or environmental science, these columns serve as linchpins in the effort to separate components efficiently and sustainably.
Summary of Key Points
In retrospect, several key points have emerged throughout the article:
- Fundamental Understanding: Fractionation columns operate on the principles of separation based on different physical or chemical properties of substances.
- Diverse Types: Various types exist, including continuous, packed, and capillary columns, each suited for specific applications.
- Technological Advances: Innovations such as nanotechnology have significantly enhanced the efficiency of fractionation processes.
- Economic and Environmental Impact: The design and operation of these columns also emphasize sustainability, cost-effectiveness, and adaptability to changing market demands.
Overall, the breadth of applicability and the evolving nature of fractionation technology underscore its importance in both research and practice.
Final Thoughts and Future Research Directions
As we look ahead, the future of fractionation columns appears promising. In particular, further research is anticipated in the following areas:
- Integration with AI: Exploring artificial intelligence applications could lead to smarter, more efficient fractionation processes that optimize output and minimize energy consumption.
- Enhanced Material Use: Future studies may seek alternative materials that could withstand harsher conditions or reduce environmental impact.
- Scale-Up Challenges: Addressing the complexities of scaling up laboratory successes to industrial applications will remain a significant focus, ensuring that advancements transition effectively into large-scale operations.
Conclusively, as challenges and opportunities evolve in the landscape of scientific separation, the role of fractionation columns will continue to be critically important. Researchers, engineers, and industry professionals must collaborate to harness their full potential for future applications.