Kevlar Reinforced Carbon Fiber: Properties and Applications
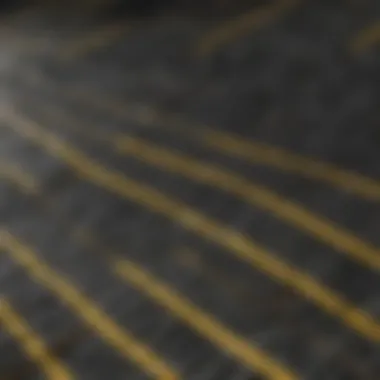
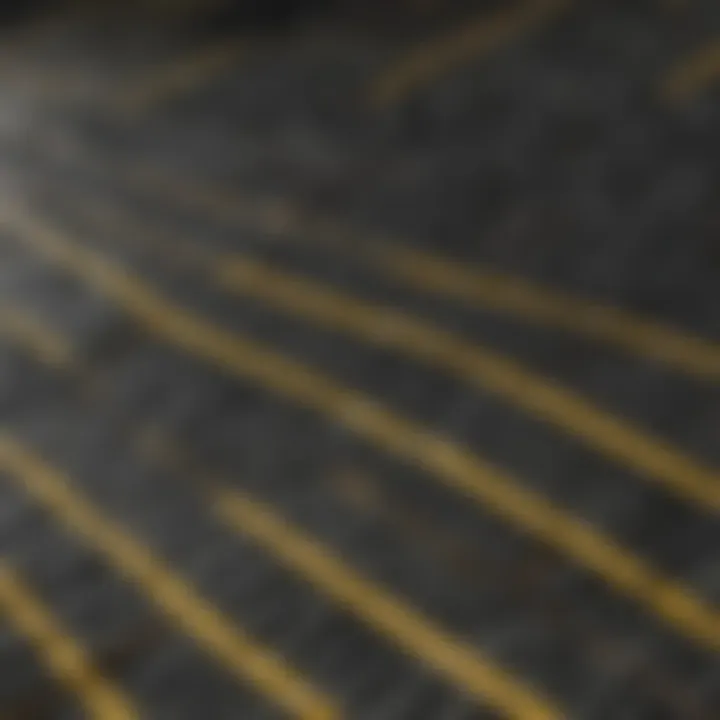
Intro
When we think about strength and durability in materials, two names often come up in conversation: Kevlar and carbon fiber. Both are celebrated in their own right. Kevlar is renowned for its unparalleled strength and resilience, while carbon fiber is prized for its lightweight and stiff properties. When these two materials are combined, the result is a high-performance composite that sets the bar high in various applications.
The combination of Kevlar with carbon fiber creates a material that does not just meet industry standards, but often excels beyond them. This article will dive deep into the properties, tensile strengths, and uses of Kevlar reinforced carbon fiber. From aerospace engineering, where both weight and safety are crucial, to protective gear that needs to withstand high-impact scenarios, this composite offers a wide range of advantages and challenges worth exploring.
We aim to present a comprehensive analysis, providing insights that are beneficial for students, researchers, and professionals alike. The focus will be on understanding how this composite material can impact technology and safety in day-to-day applications, showcasing its significance in modern industry.
Research Overview
Summary of key findings
This article highlights a few critical insights into Kevlar reinforced carbon fiber, including:
- The exceptional strength-to-weight ratio, making it ideal for applications in sectors where both are paramount.
- Enhanced durability and impact resistance compared to traditional materials.
- Its growing role in manufacturing high-performance protective gear, particularly in personal safety equipment.
Such findings indicate that the integration of these two materials not only boosts performance but also opens doors for innovation in various industries.
Importance of the research in its respective field
In a world where technology is constantly evolving and safety standards are being redefined, the study of stronger, lighter materials becomes crucial. The importance of this research lies in illustrating how Kevlar reinforced carbon fiber is not just a material but a game-changer. By helping industries achieve better safety measures and efficiency, it plays a key role in shaping the future of engineering and manufacturing. The implications of understanding these composites can influence everything from design strategies to performance ratings in critical applications.
Methodology
Description of the experimental or analytical methods used
The methodology for examining Kevlar reinforced carbon fiber involves both theoretical analysis and experimental testing. From tensile strength tests to flexural tests, researchers often focus on quantifying the performance metrics of this composite material. Some techniques include:
- Tensile Testing: To measure how much force the material can handle before breaking.
- Thermal Analysis: To understand how temperature variations affect performance.
Sampling criteria and data collection techniques
When collecting data on Kevlar reinforced carbon fiber, specific criteria are used to ensure that results are reliable and applicable to various industries. The samples must reflect real-world applications, often sourced from manufacturers that specialize in high-performance materials. Methods for data collection usually involve:
- Controlled Laboratory Environments: To eliminate external variables that could skew results.
- Field Testing: To simulate real-life scenarios and understand how the material behaves in different conditions.
By applying such rigorous methodologies, the research provides a robust understanding of the benefits and hurdles associated with Kevlar reinforced carbon fiber, laying the groundwork for further innovations in material science.
Foreword to Kevlar Reinforced Carbon Fiber
When diving into the realm of composite materials, Kevlar reinforced carbon fiber stands out like a beacon. This unique fusion is not just a technical marvel but embodies a shift in how industries approach material selection. With a blend of resilience from Kevlar and the lightweight properties of carbon fiber, these composites are tailored for high-performance applications across various fields such as aerospace, automotive, and personal protection gear. Understanding this synthesis isn’t merely academic; it helps in appreciating how these materials revolutionize engineering solutions and enhance safety.
Definition and Composition
At its core, Kevlar reinforced carbon fiber is a composite material that incorporates Kevlar fibers into a carbon fiber matrix. Kevlar, known for its exceptional tensile strength and cut resistance, lends durability to the lighter carbon fibers. Together, they create a material that is not only strong but also remarkably light. This combination is crucial since weight savings can lead to improved fuel efficiency in aerospace applications or enhanced performance in sports equipment.
The composition typically involves weaving strands of Kevlar into layers of carbon fiber, which are then bonded with a resin. This layering process can be adjusted to meet the specific needs of different applications. Moreover, the resin serves a dual purpose: it acts as a binder while also providing protection against environmental factors, ensuring longevity in various conditions. The interplay of these elements results in a versatile material suitable for high-end applications, making it a game changer in the composite materials space.
Historical Development of Composite Materials
The story of composite materials traces back several decades, with a significant leap in innovation occurring in the late 20th century. Initially, traditional materials such as steel and aluminum dominated the market. However, as industries evolved, the need for stronger, lighter materials became evident.
The introduction of carbon fiber in the 1960s marked a pivotal moment, especially in aerospace, where reducing weight is key for efficiency. Around the same time, Kevlar was unveiled by DuPont, creating ripples in the fields of safety and protection.
Together, these developments paved the way for the continuous integration of Kevlar into carbon fiber applications. Early usage included aerospace components; today, it's deeply entrenched in the creation of bulletproof vests, automotive parts, and various consumer goods. As the manufacturing processes improved, so did the performance characteristics of these composites. From rudimentary layers to complex designs, we now witness an era where innovation and technology converge to expand the use cases for Kevlar reinforced carbon fiber.
"Composite materials, such as Kevlar reinforced carbon fiber, are reshaping industries by merging the best characteristics of their components to create enhanced products."
Combining knowledge from history with advancements in material science has made it possible to not only meet but exceed the expectations of modern engineering. Such understanding helps stakeholders—from manufacturers to consumers—appreciate both the possibilities and realities involved in using Kevlar reinforced carbon fiber.
Material Properties of Kevlar Reinforced Carbon Fiber
Understanding the material properties of Kevlar reinforced carbon fiber is crucial for a variety of industries where both strength and durability are paramount. This combination showcases unique characteristics that cater to demanding applications, transforming the way we approach design and engineering. Not only does the integration of Kevlar enhance the overall mechanical properties of carbon fiber, but it also enables innovations across numerous sectors. The ensuing sections will delve deeper into specific elements of this advanced composite material, covering essentials such as mechanical strength, weight-to-strength ratio, and its resistance to extreme conditions.
Mechanical Strength and Durability
One defining feature of Kevlar reinforced carbon fiber is its exceptional mechanical strength. When compared to traditional materials like steel or aluminum, this composite evokes a strong allure in applications demanding resilience. For example, consider the construction of high-performance vehicles or aircraft. Here, the combined properties of Kevlar and carbon fiber allow for structures that can withstand not just the wear and tear of time, but also sudden impacts.
Durability in any material is often assessed by its performance under varied conditions. Kevlar itself is known for its resistance to deformation, while carbon fiber typically showcases impressive tensile strength. Together, they form a material that resists cracking, bending, and even fatigue over extended periods of usage. Whether it's a carbon fiber bicycle frame or Kevlar-imbued body armor, the result is a product that lasts far longer than many alternatives.
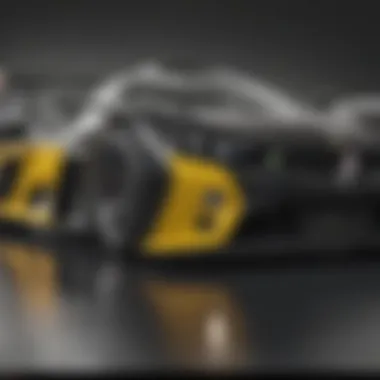
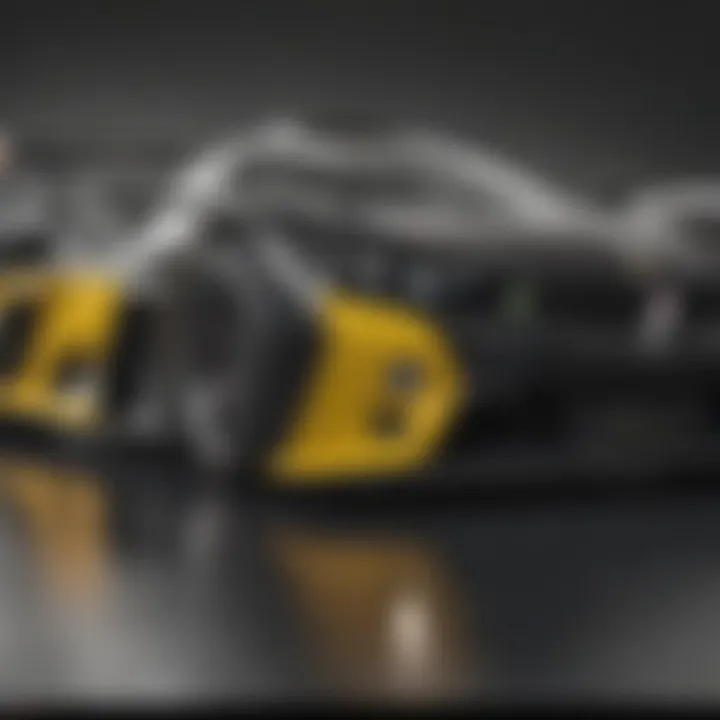
"The resilience of Kevlar reinforced carbon fiber under stresses that would compromise other materials makes it a go-to choice across critical applications."
Weight-to-Strength Ratio
One cannot overlook the remarkable weight-to-strength ratio of Kevlar reinforced carbon fiber. In sectors where weight is a crucial factor—like aerospace and automotive engineering—this composite material shines like a beacon. Lighter materials mean better fuel efficiency or quicker speeds, hence the growing interest in aviation and motorsports in utilizing this technology.
Imagine an aircraft made from conventional metals. While strong, the extra weight incurs higher fuel costs and limits performance. Now picture the same aircraft, but with sections designed using Kevlar reinforced carbon fiber. The aircraft not only reduces its overall weight significantly but maintains or even enhances its structural integrity. This translates to planes that can take to the skies with higher payloads or improved agility,
Key benefits of this exceptional ratio include:
- Improved fuel efficiency
- Enhanced logistics in manufacturing
- Greater payload capacities in transportation
Thermal and Chemical Resistance
Another significant aspect worth considering is the thermal and chemical resistance of Kevlar reinforced carbon fiber. In numerous working environments, materials are regularly exposed to harsh chemicals or high temperatures. Thus, the ability to retain integrity under such conditions is invaluable.
Kevlar itself has a high melting point and does not easily degrade in the presence of many solvents, making it ideal for protective gear in hazardous workplaces. When fused with carbon fiber, which also boasts notable thermal properties, the composite enhances its applicability in numerous fields. Industries such as automotive manufacturing exploit this by using them in components subjected to high-stress scenarios, like brake discs or engine cases.
In summary, the thermal stability and chemical resistance of Kevlar reinforced carbon fiber make it suitable for various applications, ensuring safety and performance even in extreme environments. The marriage of these two materials creates a composite that does not just meet standards, but often exceeds them, showcasing a blend of innovation and practical utility.
Manufacturing Techniques for Kevlar Reinforced Carbon Fiber
Understanding the manufacturing techniques for Kevlar reinforced carbon fiber is crucial, as these methods dictate the final characteristics of the product, affecting its performance and usability across various applications. Each technique offers its own merits and challenges, making the choice of the right approach a significant factor in the quality of the end product. Let's take a closer look at the main methods employed in producing this composite material.
Lay-Up Process
The lay-up process, often viewed as classical in composite manufacturing, involves arranging layers of Kevlar and carbon fiber materials in specific orientations relative to each other. This technique allows for great customization since the manufacturer can control fiber direction, which can significantly enhance the strength in desired areas based on the application.
- Procedure: The first step is preparing the mold, often made from aluminum or glass. Once it's ready, layers of fibers are laid down, usually mixed with a resin system, which acts like the glue holding everything together.
- Benefits: This method is flexible and can produce large or complex shapes. Furthermore, it allows for quality control at each step since the operator can visually inspect the layers being applied.
- Considerations: However, one downside is that the manual nature of this method can lead to variability in quality, particularly if left to less experienced hands. Also, it can be time-consuming, calling for someone with a keen eye to ensure optimal layering and minimal defects.
Prepreg Manufacturing
Prepreg manufacturing refers to the use of pre-impregnated materials, where the fibrous base is already coated with a resin system before the actual laying down process begins. This preparation can allow for greater uniformity and consistency in the composite product.
- Procedure: Prepreg materials are stored refrigerated to prevent curing before they're used. Once ready, the material is cut and placed into the mold, and then undergoes a curing process under heat.
- Benefits: One notable advantage is the reduced risk of air entrapment, which can affect the strength of the final product. By using prepregs, manufacturers can also achieve better control over the resin content, leading to enhanced mechanical properties.
- Considerations: While this method provides higher quality results, it can be more expensive due to the initial purchase of the materials. Additionally, the need for refrigeration can add logistical challenges during transport and storage.
Resin Transfer Molding
Resin transfer molding (RTM) is a closed-molding process that injects resin into a mold containing the fiber materials. This process allows for a controlled infusion of resin, which can lead to a uniform product.
- Procedure: In RTM, the mold is first loaded with fibers arranged according to design requirements. Then, the resin is injected under pressure, ensuring it fully saturates the fibers before curing.
- Benefits: This method can produce intricate parts with good surface finish and enhanced mechanical properties. The closed-mold system reduces the risk of volatile emissions, promoting a cleaner production environment.
- Considerations: On the downside, the machinery needed can be costly, and the process may require high levels of precision in terms of timing and pressure control. Improper approach can lead to incomplete resin infiltration, which might weaken the structure.
In short, the selection of a specific manufacturing technique can dramatically influence the performance and reliability of Kevlar reinforced carbon fiber products. Understanding these options enables producers to tailor their approach according to the specific demands of their end-use applications.
Applications in Aerospace and Automotive Industries
The significance of Kevlar reinforced carbon fiber in aerospace and automotive sectors cannot be overstated. As these industries increasingly seek materials that enhance efficiency while maintaining strong safety standards, this composite is becoming a game changer. The interplay between lightness and strength intrinsic to Kevlar reinforced carbon fiber allows manufacturers to create components that improve overall vehicle performance, fuel efficiency, and passenger safety.
When speaking about the aerospace industry, the demand for materials that withstand extreme conditions while being lightweight is critical. On the other hand, automotive applications benefit equally from reduced weight, which can translate directly into better fuel economy and handling for vehicles. The continuous evolution of this material addresses several key elements:
- Strength-to-Weight Ratio: This characteristic is something both sectors value highly. A lighter material, like Kevlar reinforced carbon fiber, reduces the load on engines and contributes significantly towards fuel savings.
- Durability: The longer lifespan of components made from this composite means lower replacement costs, both in aerospace and automotive contexts. Moreover, the inherent resistance to corrosion enhances its attractiveness.
- Safety Features: Under rigorous conditions, Kevlar's toughness can often be the difference between minor damage and catastrophic failure, thus improving safety for passengers and cargo in airports and on roads.
Aircraft Components
Within the realm of aviation, aircraft components made from Kevlar reinforced carbon fiber play an integral role. From the wings to the fuselage, these materials not only meet stringent safety requirements but also significantly lighten the aircraft's total weight. The reduced weight allows airlines to increase fuel efficiency, which is a growing environmental concern in today’s world.
For instance, parts of the aircraft landing gear are frequently constructed from this composite, providing the necessary strength to handle high impact forces while remaining lightweight. The lighter components can also facilitate quicker climbs and longer ranges, which are essential in competitive airlines.
Some of the notable benefits of using Kevlar reinforced carbon fiber in aircraft components include:
- Resilience to Environmental Stress: These materials handle fluctuations in temperature and moisture very well, ensuring that the aircraft maintains its structural integrity.
- Reduced Maintenance Cost: Since these composites resist wear and tear better than traditional materials, operators face lower maintenance costs over the aircraft's life span.
Automotive Body Panels
In the automotive realm, every kilogram matters, especially with the drive for electric vehicles and fuel-efficient models picking up steam. Automotive body panels constructed from Kevlar reinforced carbon fiber offer manufacturers the ability to produce not just lighter vehicles, but ones that have enhanced performance.
The use of this composite allows for the flexibility of design, encouraging manufacturers to innovate without compromising strength. Additionally, when discussing collision resistance, body panels made from Kevlar reinforced carbon fiber can absorb and dissipate energy from impacts more effectively than many traditional materials.
Some notable aspects regarding automotive body panels are:
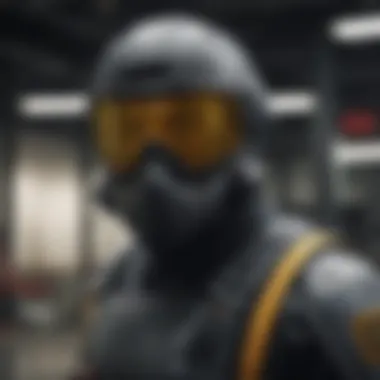
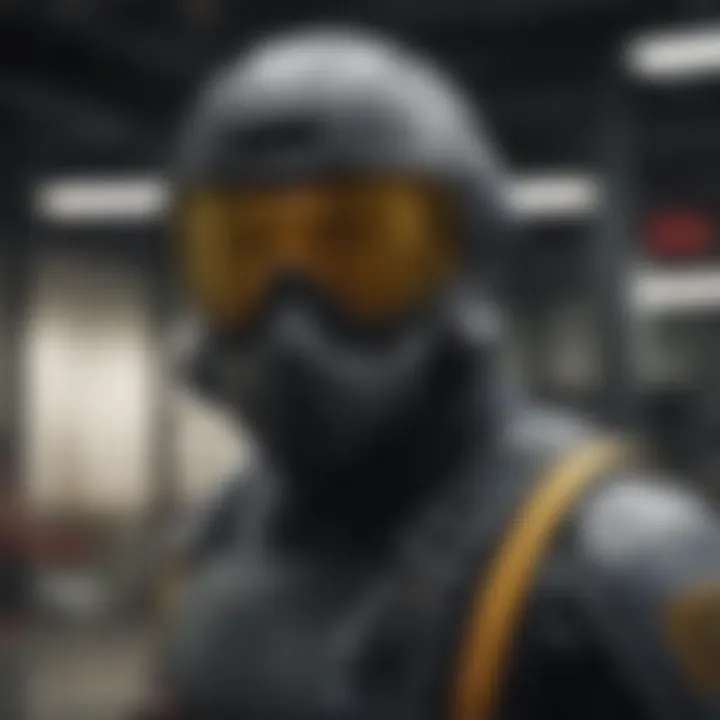
- Cost-Efficiency in Production: Mass production of parts can lead to economies of scale, especially as technology improves and the processes become more refined.
- Customization Potential: The molding capabilities allow for intricate designs, meaning manufacturers can cater to consumer preferences without sacrificing safety or performance.
In the competitive landscape of aerospace and automotive industries, the integration of Kevlar reinforced carbon fiber is not merely an advantage; it is becoming a necessity for future-ready designs and products.
Overall, the applications of Kevlar reinforced carbon fiber in these sectors mirror the urgency for innovation and safety, making this material an invaluable asset for tomorrow's engineering challenges.
Role in Protective Gear and Clothing
In the realm of protective gear and clothing, Kevlar reinforced carbon fiber stands as a beacon of innovation. The fusion of Kevlar’s remarkable strength with the lighter nature of carbon fiber creates materials that not only provide safety but also enhance performance in demanding environments. This integration is more than just a trend; it speaks volumes about how advancements in material science can directly impact human safety and functionality.
Bulletproof Vests
When it comes to personal protection, bulletproof vests are perhaps the most recognized application of Kevlar reinforced carbon fiber. These vests are engineered to absorb and dissipate the energy from projectiles, significantly reducing the risk of injury. The unique combination of materials offers an impressive balance between protection and comfort.
- Strength: Kevlar’s superior tensile strength ensures that these vests can withstand substantial impacts.
- Weight: The lightweight nature of carbon fiber enhances wearability. A soldier or law enforcement officer can operate without being bogged down by heavy gear, which is crucial during high-stress situations.
- Flexibility: This composite material allows for a greater range of motion, which can be life-saving in critical scenarios. The vests are designed for both safety and agility, allowing for easy movement without compromising on protection.
Using bulletproof vests made from Kevlar reinforced carbon fiber can lead to higher officer confidence and safety in various operations. However, it’s vital to continuously explore improvements in this field, such as advancements in layering techniques or additional protective properties against other threats.
"The choice of materials in personal protective gear significantly affects not only safety ratings but also the comfort and functionality for the wearer."
Sports Equipment
Kevlar reinforced carbon fiber is also making waves in the sports industry, where safety and performance are paramount. From helmets to body armor in contact sports, these materials are redefining standards. Key elements in this application include:
- Impact Resistance: Helmets made with Kevlar reinforced carbon fiber offer enhanced protection against blunt force trauma. This is a game changer in sports like football and cycling where head injuries are a serious risk.
- Durability: Gear such as pads and protective coverings benefits from the ruggedness of Kevlar, ensuring longevity, even under strenuous conditions.
- Lightweight Designs: Athletes require gear that doesn’t hinder their performance. The lightweight feature of carbon fiber helps athletes maintain agility while staying safe.
This combination of safety and performance enhancement transforms the landscape of sports equipment, making it not only a necessity but a competitive advantage. As research continues into the properties of these materials, we can expect to see even more innovative applications in protective gear, pushing boundaries of what is possible in safety technology.
Influence on Performance and Safety
The role of Kevlar reinforced carbon fiber in influencing performance and safety cannot be overstated. In a world where industries constantly seek materials that stand up to demanding environments, this composite material shines brightly. The unique blend of Kevlar’s high tensile strength and carbon fiber’s lightweight nature creates a product that not only excels in performance but also significantly enhances safety across various applications.
Impact Resistance Analysis
When it comes to impact resistance, Kevlar reinforced carbon fiber stands out. This material effectively absorbs energy during an impact, making it a superior choice in environments where the risk of collisions or falls is prevalent. Whether utilized in aerospace applications, where structural integrity during flight is critical, or within protective gear, the ability to withstand sudden stress is essential.
For example, in the aerospace industry, the FAA sets stringent standards for impact tolerance in aircraft components. Kevlar’s inherent ability to distribute force throughout its structure provides these components with the necessary durability to endure the rigors of flight. Similarly, in protective gear, the layered structure of Kevlar REINFORCED with carbon fiber can significantly reduce the chances of serious injury in the event of a projectile or blunt force impact.
"Impact resistance is not just a feature; it's a necessity in applications that demand the best in safety standards."
Fatigue and Wear Testing
Testing for fatigue and wear is another critical factor to understand when discussing Kevlar reinforced carbon fiber. Over time, repeated cycling of stress can lead to material fatigue, which is particularly concerning in components that experience continuous loading and unloading. Most notably in the automotive sector, where vehicles face vibrations, shocks, and various dynamic forces, materials must be capable of maintaining their strength over their entire life cycle.
Research indicates that Kevlar combined with carbon fiber exhibits superior fatigue life compared to traditional materials. This advantage means that manufacturers can design components that not only perform exceptionally under strain but also ensure reliability and significantly reduce maintenance costs. For instance, when used in components such as suspension systems, the reduced wear and extended lifespan directly translate into enhanced vehicle safety and performance.
Additionally, specialized testing methodologies, such as fatigue tests simulating extreme environments, help ensure that products can sustain their integrity over time. By implementing thorough testing regimes, manufacturers can provide data-driven assurances regarding the longevity and safety of their products.
In summary, the integration of Kevlar reinforced carbon fiber results in materials that not only meet but often exceed performance and safety benchmarks in diverse fields, ranging from aerospace to personal protective equipment. As research continues to unfold, the exciting prospects for further innovations in this composite material hold tremendous promise for even greater advancements in safety and efficiency.
Environmental Considerations
Understanding the ecological impact of materials is crucial today, especially with the rampant push for sustainability across industries. The section on environmental considerations in the context of Kevlar reinforced carbon fiber investigates important aspects of its manufacturing and lifecycle. This exploration reveals not just the benefits, but also the challenges that accompany the integration of this composite material into a greener economy.
Sustainability of Raw Materials
The raw materials used in Kevlar reinforced carbon fiber play a significant role in its environmental footprint. Kevlar, a synthetic fiber created from aromatic polyamide, and carbon fiber, derived from polyacrylonitrile, both have their own ecological consequences. While they provide superior strength and durability, their production processes can be quite energy-intensive.
One of the primary discussions around sustainability pertains to the sourcing of these raw materials. Efforts are underway to seek more eco-friendly alternatives or to develop bio-based raw materials that reduce reliance on petroleum-based feedstocks. Utilizing renewable resources not only lessens greenhouse gas emissions but also supports a circular economy. That's the key — having these materials traceable and produced responsibly, helps to minimize any adverse environmental impact.
- Benefits of sustainable raw materials:
- Reduced carbon emissions during production
- Potential for lower overall energy consumption
- Support for environmentally friendly practices in industries
On the flip side, the transition to sustainable materials often requires sizable investments and may not always provide immediate cost savings. Stakeholders must balance the inherent benefits against the economic viability of adopting green practices. It’s a tough nut to crack, but industries need to prioritize this for long-term prosperity.
Recycling Challenges
While the advantages of Kevlar reinforced carbon fiber are clear, the path to recycling presents its own set of hurdles. The dichotomy of its strength and durability means that when end-of-life products made from this composite are disposed of, they often end up in landfills due to the complexity of recycling processes. The question then becomes — how do we recover value from these materials at the end of their useful life?
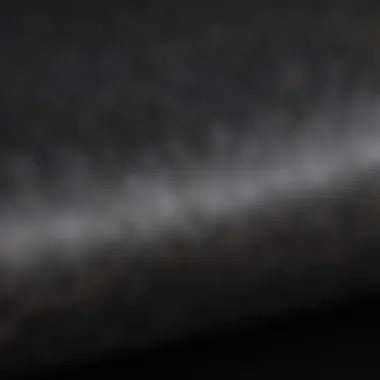
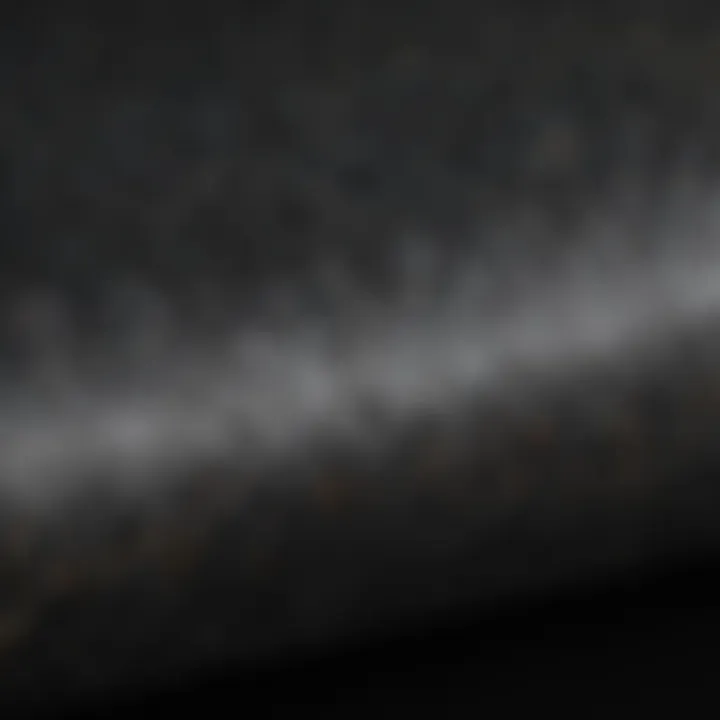
Recycling Kevlar and carbon fiber is far from straightforward. Unlike materials like aluminum or glass, which can be remelted and reshaped with relative ease, the fibers used in composites pose distinct challenges. Current methods often lead to a loss of material integrity, which makes reuse impractical for many applications. Moreover, the mixed-component nature of composites complicates recycling, as separating materials without damage is not a walk in the park.
"Innovations in recycling technology are desperately needed to convert these composites back into usable materials, helping to close the loop in the lifecycle of Kevlar reinforced carbon fiber products."
Let's list some of the critical challenges in recycling:
- Separation Difficulty: The composite's structure makes it hard to separate distinct materials for recycling.
- Limited Facilities: Not all recycling centers are equipped to handle high-tech composites.
- Economic Factors: The cost of recycling is sometimes higher than producing new materials, discouraging recycling efforts.
To counter this, researchers and companies are exploring novel techniques, including chemical recycling processes and recycling-friendly designs that might allow easier dismantling at the end of life. As these innovations unfold, the potential for Kevlar reinforced carbon fiber to contribute more positively to the environment may improve significantly, echoing broader trends in sustainability.
Future Innovations in Composite Materials
The realm of composite materials is on the brink of significant transformations, particularly with Kevlar reinforced carbon fiber. As industries continually seek materials that not only fulfill the demands of strength and lightness but also cater to sustainability, the pursuit for innovation in composites becomes critical. This section delves deep into the emerging trends in composite materials, highlighting the impacts, benefits, and considerations that accompany these innovations.
Nanocomposite Developments
Nanocomposites bring a revolutionary twist to the traditional composite materials landscape. By integrating nanoscale elements into Kevlar reinforced carbon fiber, manufacturers can enhance the overall performance of these composites beyond what was previously envisioned.
- Enhanced Mechanical Properties: When nanoparticles are added, there's a noticeable improvement in mechanical strength and stiffness, often changing the game for aerospace and automotive applications.
- Weight Reduction: Despite the added components, the overall weight remains minimal, which is crucial for performance-oriented sectors.
- Design Versatility: Nanoscale modifications allow for greater flexibility in design. Engineers have more room to experiment with shapes and functionalities that were once impossible.
These advancements are not merely academic. For instance, within the aerospace industry, using nanocomposites could translate into lighter and more fuel-efficient aircraft, ultimately leading to reduced operational costs and lower carbon footprints.
Smart Materials Integration
Smart materials represent another leap forward. Selling point of smart materials is their ability to respond dynamically to changing environmental conditions. This property can be incorporated into Kevlar reinforced carbon fiber, resulting in materials that not only resist impacts but can also alert users to stress or wear.
- Self-Sensing Ability: Integrating sensors directly into the fiber structure enables real-time monitoring of structural integrity. This can greatly enhance safety in critical applications, such as military gear or high-performance vehicles.
- Adaptive Properties: Materials that can adapt their rigidity based on temperature or pressure promote not just safety but also comfort. Think about sports equipment, which can provide supportive characteristics when under strain and become more compliant under lighter loads.
- Energy Harvesting: Imagine gear that not only protects but also generates energy. Smart materials can harness kinetic energy from movements and convert it into usable power.
"The future of composite materials lies not only in their strength or lightweight characteristics but in their ability to sense, adapt, and recover in real-time."
Case Studies on Successful Implementation
The utilization of Kevlar reinforced carbon fiber in real-world scenarios showcases its transformative impact across various industries. Case studies serve as crucial references, providing insights into the effectiveness of this composite material. They highlight practical applications, the challenges faced, and the lessons learned which, in turn, can inform future developments and innovations. These studies not only underscore the significant benefits of this material—like its strength, weight efficiency, and durability—but also reveal considerations that must be taken into account when implementing such technologies.
In the area of aerospace and automotive, case studies illustrate the journey from conception to practical application, shedding light on the methodologies and outcomes of projects that utilize Kevlar reinforced carbon fiber.
"By analyzing real-world applications, we gain tangible evidence of the advantages and limitations of Kevlar reinforced carbon fiber, allowing for more informed decisions in future research and engineering."
Aerospace Projects
Aerospace applications of Kevlar reinforced carbon fiber have made significant strides in enhancing the performance and safety of aircraft. A notable example would be the use of this material in the construction of fuselage components for modern aircraft. Companies like Boeing and Airbus have explored the potential of combining these materials to reduce weight while retaining structural integrity. This innovation results in lower fuel consumption and improved overall efficiency.
One fascinating case is the use of Kevlar composites in the Boeing 787 Dreamliner. The lightweight nature of the material allows for larger windows and improved aerodynamics, factors that contribute to greater passenger comfort and operational savings. The studies performed on the 787 reveal several benefits:
- Reduced empty weight leads to increased payload capacity.
- Enhanced fuel efficiency results in decreased operational costs.
- Improved performance in severe weather conditions due to robust material properties.
On the flip side, challenges surrounding environmental sustainability and production costs have surfaced. The aerospace industry is well aware of the need for responsible practices, making it a primary concern moving forward.
Automotive Innovations
The automotive industry also showcases the effectiveness of Kevlar reinforced carbon fiber in various applications. Manufacturers are increasingly recognizing the potential of integrating this composite into their vehicle designs for performance improvements. For instance, McLaren has been lauded for its pioneering applications of carbon fiber in car construction, incorporating Kevlar for added toughness.
A prime example is the McLaren P1, which employs a unique blend of carbon fiber and Kevlar for its lightweight chassis. The benefits of using this composite material are evident:
- Improved acceleration due to reduced weight.
- Enhanced handling and stability with a stiffer structure.
- Increased safety during collisions, as the material absorbs impact effectively.
However, the adoption of Kevlar reinforced carbon fiber in automotive design isn't without its hurdles. High manufacturing costs and the complexity of the material pose challenges for mass production. Manufacturers must strike a balance between performance enhancement and cost-effectiveness, ensuring that innovations remain viable for the average consumer.
Culmination and Future Directions
Understanding Kevlar reinforced carbon fiber holds immense significance in various fields, particularly in advancing material science and engineering. As industries increasingly seek lightweight yet robust materials, this composite stands out as a promising solution. Its unique integration of Kevlar’s power with carbon fiber’s featherweight nature not only opens doors for innovative applications but also enhances safety and efficiency.
Summary of Key Findings
Over the course of this analysis, several essential points emerged regarding Kevlar reinforced carbon fiber:
- Strength and Durability: The combination of Kevlar and carbon fiber yields materials that excel in both tensile strength and resistance to impact. This makes them ideal for applications where structural integrity is paramount.
- Weight Efficiency: Lightweight materials contribute to improved performance, particularly in aerospace and automotive sectors, where every gram counts. The weight-to-strength ratio is particularly favorable in these environments.
- Thermal and Chemical Resistance: The resilience of Kevlar reinforced carbon fiber against various environmental extremes adds an additional layer of reliability, especially in harsh industrial applications.
- Application Spectrum: From aircraft components to protective gear, the versatility of this composite material reveals its vast potential across multiple sectors. Each application benefits differently, showcasing the material’s adaptive qualities.
Moreover, considerations about sustainability and recycling challenges serve as reminder of the need for research in this area as industries evolve to meet environmental regulations.
Next Steps in Research
Encouraging advancements in understanding and utilizing Kevlar reinforced carbon fiber suggest several avenues for future research. Some potential areas include:
- Nanotechnology Integration: Exploring how nanocomposites could enhance performance characteristics, especially in improving the material’s damage tolerance and fatigue resistance.
- Smart Material Development: Investigating the incorporation of smart technologies, such as self-repairing capabilities, could vastly improve safety components across various applications.
- Sustainability Practices: Establishing more efficient recycling methods to address environmental concerns and develop more eco-friendly production processes for the composites.
- Long-Term Performance Studies: Performing extensive field studies to better understand the wearing behaviors under different environmental conditions, and how that might affect longevity and functionality.