In-Depth Insights on Nickel Diamond Coating Technology
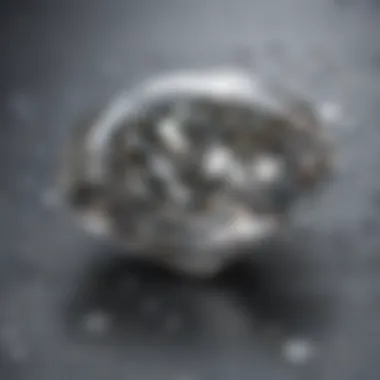
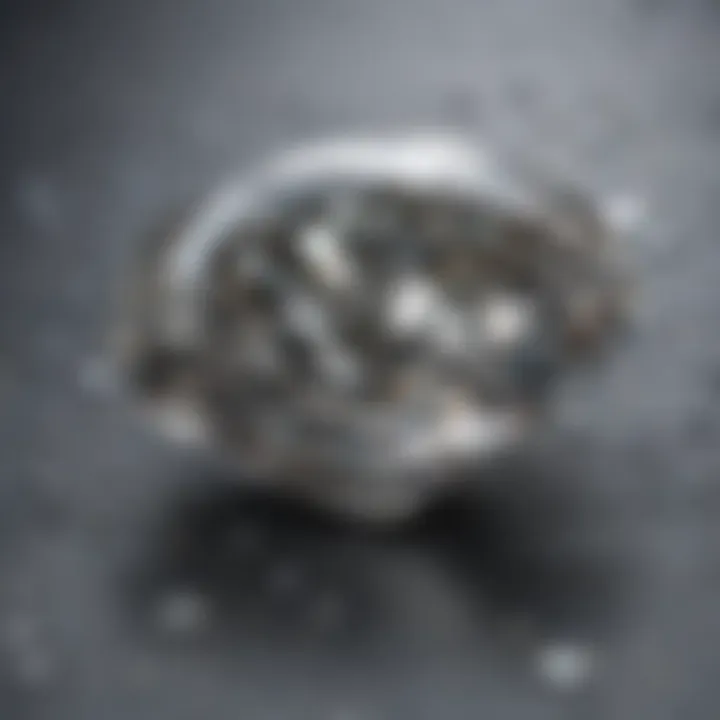
Intro
Nickel diamond coating is a significant technological advancement with applications across a wide range of industries. This composite material combines the toughness of nickel with the hardness of diamond, creating a coating that offers enhanced performance, durability, and resistance to wear and corrosion. Understanding this coating’s material properties, production techniques, advantages, and challenges is essential for professionals and researchers alike.
The blend of nickel and diamond has sparked interest due to its potential to improve the longevity and efficiency of components in manufacturing. Various sectors, including aerospace, automotive, and electronics, stand to benefit from advancements in this area. In this article, we will explore these dimensions comprehensively and examine how current trends and future advancements shape the application of nickel diamond coatings.
Research Overview
Summary of Key Findings
Recent research has revealed several critical insights into nickel diamond coatings. The studies demonstrate that the combination of these two materials results in a superior coating with exceptional hardness, thermal conductivity, and corrosion resistance. Nickel's intrinsic properties allow for good bonding with substrates, while diamond particles enhance the overall performance regarding wear resistance. Overall, the research underscores the effectiveness of nickel diamond coatings in extending component life and reducing maintenance costs.
Importance of the Research in Its Respective Field
The importance of studying nickel diamond coating lies in its potential applications. Industries are continuously seeking ways to optimize materials for better performance. The ability to utilize nickel diamond coatings can lead to improved operational efficiency, reduced downtime, and enhanced safety. Furthermore, this research can drive innovations in coating technologies, impacting how components are designed and used in varied applications.
Methodology
Description of the Experimental or Analytical Methods Used
The methodology in examining nickel diamond coatings often includes a combination of experimental techniques. These may involve physical vapor deposition or chemical vapor deposition to apply diamond particles onto nickel substrates. Analytical methods are then used to assess the coating properties, such as hardness testing, adhesion strength evaluation, and wear resistance.
Sampling Criteria and Data Collection Techniques
Data collection for such research typically involves sampling coatings from various production batches. Standardized testing methods ensure that results are reliable and reproducible. The criteria for sampling might include parameters such as coating thickness, particle size, and the uniformity of application, which are crucial to understanding the performance metrics of nickel diamond coatings.
"Understanding the scientific principles behind nickel diamond coatings is essential for unlocking their full potential in practical applications."
As we delve deeper into this analysis, insights from various studies will guide our understanding of how nickel diamond coatings can revolutionize the manufacturing landscape.
Prelims to Nickel Diamond Coating
The realm of surface coatings has expanded in the last few decades. Among various coatings, nickel diamond stands out due to its distinct properties and applications. Understanding this specific coating is essential, especially considering the increasing demand for materials that enhance durability and performance in various industries. Nickel diamond coating combines the corrosion resistance and strength of nickel with the exceptional hardness of diamond. This combination provides various benefits, such as improved wear resistance and thermal stability.
The significance of nickel diamond coating cannot be understated. It has applications ranging from aerospace components to medical devices. Its ability to withstand harsh environments while maintaining performance adds considerable value. Furthermore, the process of creating and applying this coating is intricate, involving careful scientific and engineering considerations. Professionals and researchers must grasp these details to maximize the coating's functionality.
Definition and Overview
Nickel diamond coating is a composite material that consists of nickel and diamond particles. The nickel acts as a matrix, binding the diamond particles and facilitating the application process. The result is a solid coating that exhibits extraordinary properties, making it ideal for various industrial applications. The coating process typically involves methods such as electroplating or chemical vapor deposition, depending on the desired characteristics.
This coating provides distinct advantages, primarily due to the hardness of diamonds. This feature allows components coated with nickel diamond to endure significant friction and wear, making them suitable for high-stress applications. Additionally, the corrosive resistance of nickel protects the underlying material from environmental degradation, which is crucial in industries like automotive or manufacturing.
Historical Context
The development of nickel diamond coating has evolved over several decades. Initially, surface coatings focused primarily on improving wear resistance through simpler materials. The advent of new technologies enabled the integration of diamond particles, significantly enhancing the performance of coatings.
Early research into diamond coatings predominantly concentrated on natural sources. However, advancements in synthetic diamond technology allowed for more consistent and accessible materials. Today, researchers continue to explore innovative approaches to improve the deposition process and overall effectiveness of the coating. This ongoing research indicates a promising future for nickel diamond coating in various applications, reinforcing its relevance in both industry and academia.
Material Properties of Nickel Diamond Coating
The material properties of nickel diamond coating play a crucial role in its effectiveness and application across various industries. The combination of nickel and diamond creates a material that offers exceptional performance characteristics. Understanding these properties is essential for professionals and researchers aiming to utilize this technology effectively. The discussion will center around the distinct characteristics of nickel and diamond, as well as the synergistic effects of their combination.
Nickel Characteristics
Nickel is a versatile metal that exhibits various beneficial properties. It has a relatively high melting point, which allows it to maintain strength and stability even under elevated temperatures. Nickel coatings are known for their excellent adhesion properties, making them suitable for a range of substrates. Additionally, nickel is known for its good electrical and thermal conductivity, which contributes to its effectiveness in many applications.
Other noteworthy aspects of nickel include its resistance to corrosion and wear. When nickel is used in coating applications, it can significantly enhance the longevity of the surface it protects. Moreover, the ductility of nickel allows it to be easily shaped and applied in various forms, making it suitable for complex geometries. This property is particularly important in precision engineering sectors where component specifications must be exact.
Diamond Characteristics
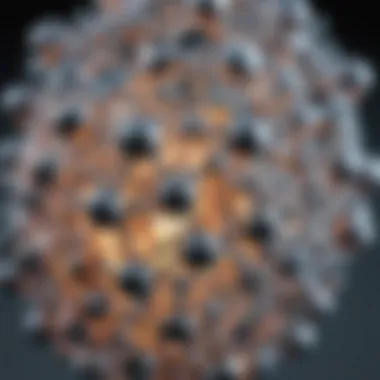
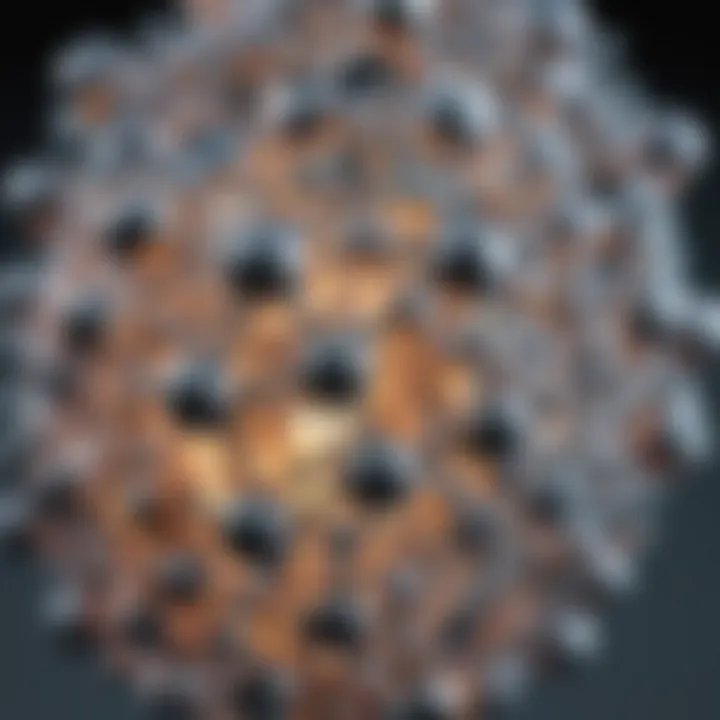
Diamonds, on the other hand, are renowned for their exceptional hardness and wear resistance. In fact, they are one of the hardest known natural materials. This intrinsic hardness translates into superior abrasion resistance when diamond is incorporated into coatings. Furthermore, diamonds possess excellent thermal conductivity, which is an asset in applications where heat dissipation is critical.
The clarity of diamonds also contributes positively to optical applications, where laser processing is required. Another remarkable trait of diamond coatings is their chemical inertness, which means they do not react easily with other substances. This property allows them to be used in aggressive environments without degrading, making diamond-coated tools invaluable in specific industrial applications.
Synergistic Effects
When nickel and diamond are combined, the resulting coating benefits from the unique properties of both materials. The synergistic effects enhance overall performance, making nickel diamond coatings superior in terms of durability and functionality.
- The hardness of diamond complements the wear resistance of nickel, leading to a coating that withstands extensive use and maintains its integrity.
- Nickel’s excellent adhesion enhances the diamond’s stability on various substrates, reducing the risk of delamination or flaking over time.
- Thermal properties are also improved; diamond’s thermal conductivity combined with nickel’s capacity for heat management ensures efficient temperature regulation.
Nickel diamond coatings present a valuable solution, particularly in demanding environments. They are ideal for tools and components that require both strength and longevity in challenging conditions. This synergy not only leads to extended service life but also can improve the overall efficiency of devices, thereby saving costs in the long run.
Application Techniques
In the realm of nickel diamond coating, application techniques play a central role in determining the efficacy and reliability of the coating process. This section assesses various methods through which nickel diamond coatings can be applied. Each technique carries unique attributes that affect the final coating quality, performance, and application context. Understanding these techniques aids in optimizing coatings for specific uses and ensures that desired properties are achieved.
Deposition Methods
Different deposition methods are crucial in establishing the right characteristics of nickel diamond coatings. Each method presents its own set of benefits and limitations that can impact the coating's adherence and overall performance.
Electroplating
Electroplating is a widely used method for applying nickel diamond coatings. This process involves immersing the substrate in an electrolyte solution containing nickel ions, followed by passing an electric current through the solution. The principal benefit of this method is its ability to produce a uniform coating across the substrate surface. Additionally, electroplating is cost-effective and can be easily scaled for various applications, making it a popular choice in large-scale manufacturing. However, one should note that the electroplated layer may require post-treatment to enhance its durability.
Key characteristics:
- Uniform layer distribution.
- Economical for large volumes.
Advantages:
- Good adhesion properties.
- Suitable for intricate designs or shapes.
Disadvantages:
- May require subsequent surface treatments for improved properties.
Chemical Vapor Deposition
Chemical Vapor Deposition (CVD) represents a more complex approach but is favored for its ability to create highly conformal coatings. This process involves introducing gaseous reactants that decompose on the substrate surface, forming a solid film. The primary advantage is that CVD enables precise control over layer composition and thickness. This method is particularly beneficial for applications where high purity and low residual stress in coatings are necessary. Nevertheless, CVD processes tend to be more expensive and require sophisticated equipment, which may limit its accessibility for some industries.
Key characteristics:
- High purity and conformality.
- Strong growth control over process.
Advantages:
- Excellent adhesion to complex geometries.
- Low residual stresses in the coating.
Disadvantages:
- Higher costs due to equipment requirements.
- Longer processing times.
Physical Vapor Deposition
Physical Vapor Deposition (PVD) involves the physical transfer of material from a target source to the substrate through vaporization. This technique can yield dense coatings with excellent hardness. PVD can also achieve specific material properties, leading to diverse applications across industries. A notable aspect of PVD is its versatility; it can be adapted to a range of materials, including metals and ceramics. Although it requires a vacuum environment, the final product demonstrates outstanding mechanical and thermal properties.
Key characteristics:
- High density and hardness levels.
- Versatile in materials used.
Advantages:
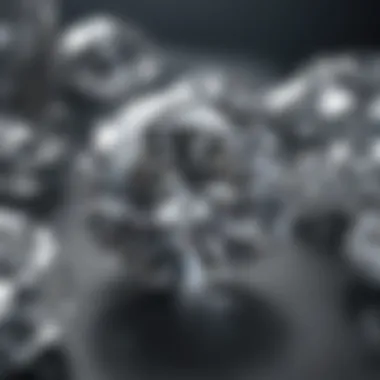
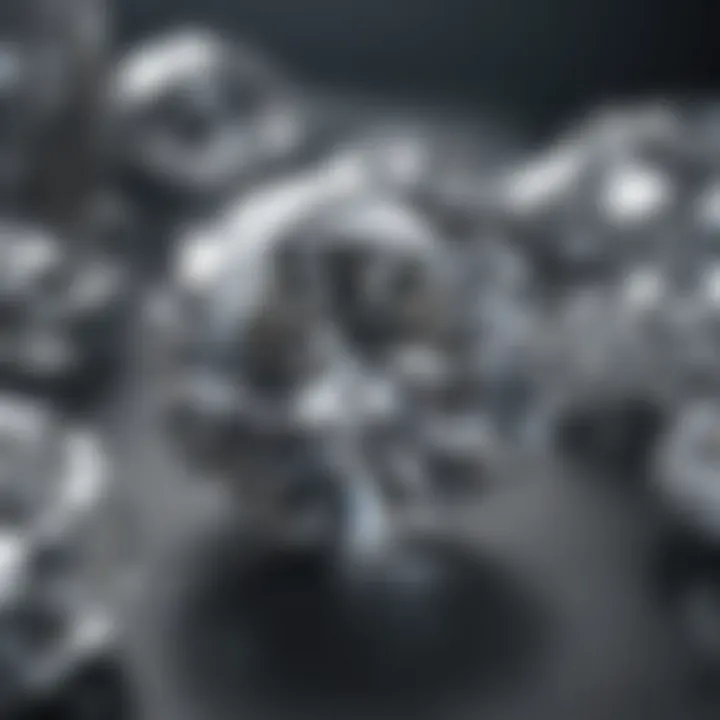
- Good adhesion and toughness.
- Can produce very thin layers without compromising performance.
Disadvantages:
- Requires vacuum equipment and environmental control.
- Slower deposition rates compared to other methods.
Layer Thickness Considerations
The thickness of the nickel diamond coating significantly influences several performance factors, such as wear resistance and thermal conductivity. It is important to choose a thickness that balances these properties with cost-effectiveness. Thin layers may not provide sufficient protection, while overly thick layers can add unnecessary weight and where the performance might not be maximized. Tailoring the layer thickness based on specific applications is essential to achieve the desired balance of durability and functionality.
Surface Preparation Techniques
Surface preparation forms the foundation for a successful application of nickel diamond coating. The substrate must be meticulously prepared to remove contaminants, such as dust and oils, that can hinder adhesion. Techniques like sand blasting, grinding, or chemical cleaning may be employed to create an optimal surface profile for coating adherence. Proper surface preparation not only improves adhesion but also enhances the overall performance of the coating, prolonging its service life.
"The effectiveness of the coating is often directly proportional to the preparation of the substrate."
In summary, the application techniques of nickel diamond coating are critical in defining the performance and longevity of the coating. Choices among deposition methods and considerations of layer thickness and surface preparation can greatly affect the coating's effectiveness in various industrial applications.
Advantages of Nickel Diamond Coating
The advantages of nickel diamond coating are significant in various industrial applications. This coating brings together the unique properties of nickel and diamond to create surfaces that are not only durable but also efficient. Understanding these advantages helps in appreciating why nickel diamond coatings are increasingly used across different sectors.
Increased Hardness and Wear Resistance
Nickel diamond coating exhibits remarkable hardness, primarily due to the presence of diamond particles. These particles lend the coating excellent wear resistance, making it suitable for environments where mechanical wear and tear are prevalent. The inherent hardness of diamond, rated on the Mohs scale, ensures that surfaces coated with this material can withstand significant stress without succumbing to damage. In manufacturing processes, such as cutting and machining, tools coated with nickel diamond can maintain their efficiency over extended periods. This endurance translates into reduced downtime and lower costs of replacing or repairing tools.
Additionally, the combination of nickel with diamond supports adhesion and reduces the likelihood of flaking or peeling. Improved wear properties enhance product longevity, making nickel diamond coatings a good investment in terms of operating costs. The durability provided by this coating can be illustrated in various applications:
- Industrial Tools: Prolonged life span in harsh environments
- Automotive Components: Enhanced performance in friction wear applications
- Aerospace Accessories: Critical for maintaining structural integrity
Thermal Conductivity
Another notable advantage of nickel diamond coatings is their exceptional thermal conductivity. Efficient heat dissipation is crucial in applications involving high temperatures. For instance, electronic components and certain types of machinery require materials that can effectively manage heat to prevent overheating and maintain performance. Nickel diamond coatings provide a reliable solution by conducting heat away quickly. This is particularly beneficial in precision instruments that must operate at specific temperature thresholds to ensure accuracy.
The thermal management qualities also play a significant role in the following areas:
- Electronics: Improved thermal performance for integrated circuits and semiconductor devices
- Manufacturing Equipment: Reduces risk of heat-induced failures
- Medical Devices: Essential in high-precision tools that require stable thermal conditions
Corrosion Resistance
Corrosion resistance is a critical property of nickel diamond coatings, making them suitable for various environments, including those exposed to harsh chemicals or moisture. Nickel itself has inherent corrosion-resistant properties, which, when combined with durable diamond, provides a synergistic effect that enhances overall resistance. This means that components covered with nickel diamond coatings are less likely to experience rust or degradation over time, extending their useful life.
This quality is particularly important in industries such as:
- Marine Applications: Protects components from saltwater exposure
- Chemical Processing: Prevents deterioration in aggressive environments
- Food Processing: Meets hygiene standards while resisting wear and corrosion
In summary, the advantages of nickel diamond coating are multifaceted. From increased hardness and wear resistance to superior thermal conductivity and corrosion resistance, these properties collectively promote efficiency and durability in a wide array of applications. This makes nickel diamond coating a pivotal technology in many advanced industries.
"Nickel diamond coatings represent a convergence of two exceptional materials, leading to superior performance in challenging industrial environments."
By understanding these benefits, professionals can make informed decisions about the incorporation of nickel diamond coatings into their processes, ultimately enhancing the quality and longevity of their products.
Challenges in Nickel Diamond Coating
Understanding the challenges associated with nickel diamond coating is essential in evaluating its practical applications and success in various industries. While the coating offers substantial benefits, such as enhanced hardness and wear resistance, several issues must be addressed to ensure effective implementation. Recognizing these challenges can provide insights into how to optimize the utilization of nickel diamond coatings in different production environments.
Cost-Effectiveness
Cost is a fundamental concern when considering nickel diamond coatings. Although the benefits of increased durability and performance are clear, the upfront investment for the coating process can be significant. Electroplating and advanced deposition techniques often require high-quality materials and specialized equipment. Consequently, the initial costs can deter some companies from adopting this technology.
However, a careful analysis can reveal that the long-term savings might offset these initial costs. When properly implemented, nickel diamond coatings can enhance the lifespan of components, leading to reduced replacement rates and maintenance expenses. Industries such as aerospace and automotive, where precision and durability are critical, might find the investment worthwhile. Therefore, evaluating the total cost of ownership is crucial for enterprises contemplating the adoption of these coatings.
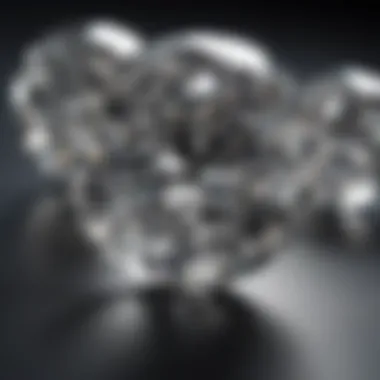
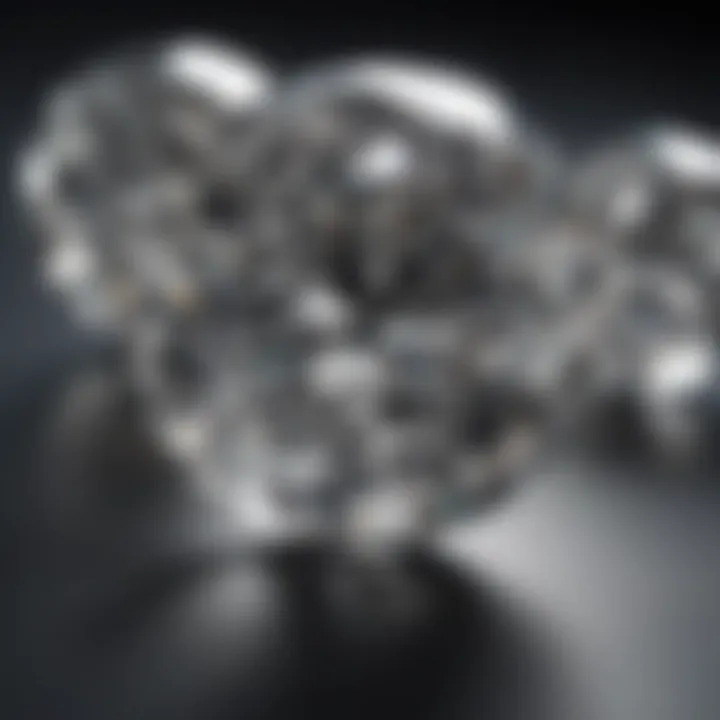
Adhesion Issues
Adhesion is another critical challenge when applying nickel diamond coatings. The effectiveness of the coating relies heavily on its ability to adhere firmly to the substrate. Poor adhesion can lead to chipping or delamination, which compromises the coating's performance and defeats its purpose. Several factors affect adhesion, including the substrate material, surface treatments, and environmental conditions during application.
Surface preparation techniques are vital in ensuring good adhesion. For instance, cleaning the substrate to remove any contaminants is essential. Techniques such as sandblasting or chemical etching often enhance the surface roughness, allowing for better mechanical interlocking with the coating. Researchers are actively exploring new adhesion-promoting methods to mitigate these challenges, and advancements in chemical formulations for binding agents may also play a role.
Environmental Impact
Lastly, the environmental impact of nickel diamond coatings warrants attention. The manufacturing processes involved in creating these coatings can release pollutants if not managed correctly. For example, some deposition methods may utilize hazardous chemicals that pose risks to both health and the environment.
Fortunately, recent advancements have focused on developing more sustainable practices that minimize these risks. Researchers are studying eco-friendly alternatives to traditional coating materials and processes. As industries become more accountable for their environmental footprints, the drive towards greener technologies is essential for the future of nickel diamond coatings. Ensuring compliance with environmental regulations is crucial not only for legal reasons but also for maintaining a positive public perception.
"Addressing these challenges will pave the way for broader adoption of nickel diamond coatings in various industries, enhancing their technological advances."
In summary, understanding the challenges faced in nickel diamond coating, including cost-effectiveness, adhesion issues, and environmental impact, is critical. Each aspect requires careful consideration to optimize the use of these coatings, ultimately improving their acceptance across industries.
Industrial Applications
The section on industrial applications highlights the crucial role nickel diamond coating plays in various sectors. Understanding these applications allows for better insight into how the properties of this coating enhance product performance and longevity across different fields. The benefits of nickel diamond coating can lead to increased efficiency, improved safety, and potential cost savings in manufacturing processes. Each industry presents unique challenges that this coating can address effectively.
Aerospace Industry
In aerospace, nickel diamond coatings are essential for components exposed to extreme conditions. These coatings enhance wear resistance, critical in parts like turbine blades and landing gear. The ability to withstand high temperatures and corrosive environments makes nickel diamond an excellent choice for aerospace applications. Recent research also shows that using nickel diamond coatings can improve fuel efficiency in aircraft by reducing friction, leading to lower operational costs.
Automotive Sector
The automotive industry benefits significantly from nickel diamond coatings, particularly in components such as engine parts and brake systems. The increased hardness prevents wear and tear, extending the lifecycle of these critical parts. Additionally, the thermal conductivity properties of this coating help dissipate heat efficiently, contributing to better performance and safety. As manufacturers strive for sustainability, adopting nickel diamond coatings may reduce the need for frequent replacements, thus promoting a more environmentally friendly approach.
Medical Devices
In the field of medical devices, the application of nickel diamond coatings offers advantages that are particularly relevant for surgical instruments and implants. The antimicrobial properties of diamond, combined with the strength of nickel, provide surfaces that are not only durable but also reduce the risk of infection. This feature is vital for instruments used in surgeries. The coating also enhances biocompatibility, essential for implants, ensuring a safer integration with human tissue. The advancements in medical technology accentuate the need for materials that support both efficacy and patient safety.
Nickel diamond coatings ensure that industries benefit from durability while addressing the unique challenges they face. From aerospace to healthcare, the applications are vast and vital.
Research Trends and Future Prospects
Understanding the research trends and future prospects of nickel diamond coating is essential for advancing its application across various industries. This field is characterized by ongoing developments that not only push the boundaries of current technology but also encourage the exploration of novel materials and approaches. The importance of examining these trends lies in the potential benefits they offer in enhancing the performance characteristics of nickel diamond coatings. Current research aims to optimize coating applications, improve material properties, and address existing challenges, making it highly relevant for manufacturers and researchers alike.
Recent Advances in Coating Technology
Recent advances in coating technology have significantly transformed the capabilities of nickel diamond coatings. Researchers have focused on refining deposition techniques to create thinner, more uniform coatings. For instance, improvements in Chemical Vapor Deposition (CVD) methods allow for better control over the microstructure of the coatings, which can lead to enhanced durability and performance. Additionally, innovations in Electroplating techniques have improved adhesion properties, reducing the likelihood of delamination during operation.
Moreover, advancements in analytic methods, such as high-resolution electron microscopy, enable a better understanding of how coating properties relate to their microstructural characteristics. These insights have also facilitated the development of hybrids, combining nickel diamond coatings with other materials to further enhance their functional performance. Some recent studies have reported promising results in combining nano-coatings, which could enhance specific properties like wear resistance and toughness.
"The intricate relationship between deposition methods and coating structure holds the key to unlocking new performance metrics in nickel diamond coatings."
Future Materials Exploration
As industries demand more from their surface coatings, future materials exploration will play a vital role in evolving nickel diamond coatings. Researchers are currently investigating alternative substrate materials that can further elevate the coating's performance capabilities. This exploration includes materials such as silicon carbide and titanium nitride, which exhibit favorable thermal and mechanical properties.
Another area of interest is the incorporation of advanced ceramics into the coating matrix. Such innovations could potentially enhance the thermal stability and wear resistance of traditional nickel diamond coatings, making them suitable for more extreme environments.
Furthermore, the use of computational modeling is expected to accelerate material discovery. Simulations can predict how different combinations of materials behave under various conditions, reducing the time and cost associated with experimental trials.
There is also a growing focus on sustainable practices in the development of nickel diamond coatings. Researchers are making strides in identifying eco-friendly alternatives to traditional plating materials, which aligns with global trends towards sustainability in manufacturing. Overall, the future of nickel diamond coating appears promising, with a horizon filled with diverse possibilities that could reshape its applications in industry.
Culmination
The conclusion serves as an essential element within this article, encapsulating the critical points discussed throughout the various sections. Summarizing the intricate details about nickel diamond coating offers readers a clear understanding of its significance. The combination of nickel and diamond illustrates a synergy that enhances the overall performance, longevity, and efficiency of coated surfaces.
Summarizing Key Insights
Nickel diamond coating stands out due to its unique material properties. The coating provides substantial wear resistance, thermal conductivity, and corrosion protection. Each of these properties is vital, especially in industrial applications where component failure can lead to expensive downtimes and safety hazards. An important insight gathered from this analysis of nickel diamond coating is its adaptability. It can be applied using various deposition techniques, letting industries tailor it according to specific requirements and challenges. The versatility in thickness, alongside surface preparation options, further strengthens its position as a leading choice in advanced manufacturing.
Implications for Industry and Research
The implications of nickel diamond coating in both industry and research are significant. For manufacturers in the aerospace, automotive, and medical device sectors, utilizing this coating can lead to product innovations and performance improvements. The reduced wear in critical components optimizes operation, thus increasing overall efficiency and safety. Furthermore, the exploration of future materials that build upon the principles of nickel diamond coating can lead to even more innovative solutions. Research trends indicate a growing interest in eco-friendly application methods and the potential for integrating smart technologies with coatings.