The Crucial Role of Tribologists in Industry
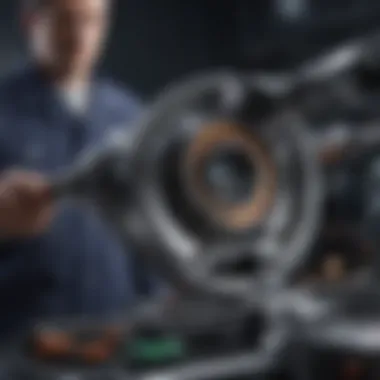
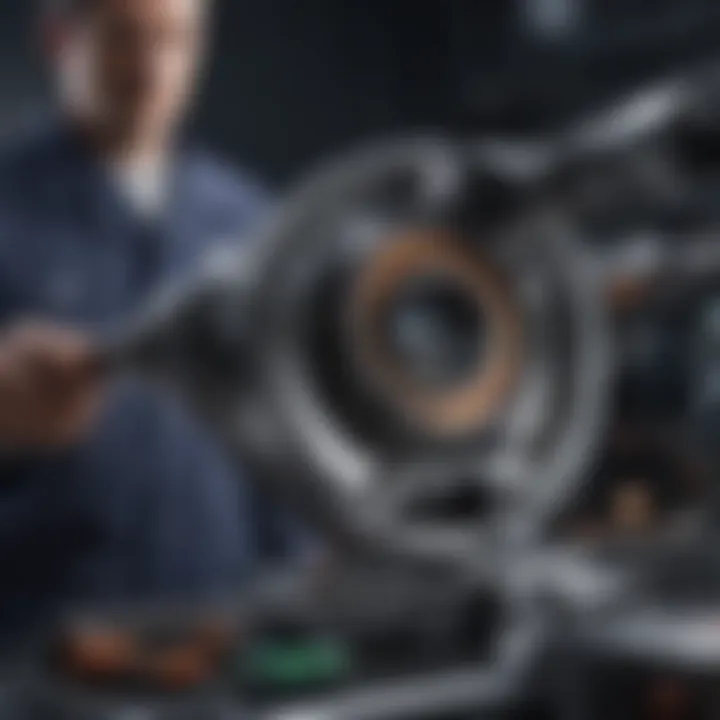
Intro
Tribology serves as a pivotal discipline within materials science and engineering, encompassing the study of friction, wear, and lubrication. It plays an essential role in various industries, from automotive to aerospace. Understanding how tribology impacts a material's performance helps engineers devise solutions that enhance reliability and efficiency. As industries seek to improve process effectiveness and reduce material degradation, tribology emerges as a key area of research and application.
Research Overview
Summary of Key Findings
Research in tribology reveals significant insights that are critical for numerous sectors. Studies have demonstrated that optimized lubrication can dramatically reduce wear rates in mechanical components. Research is continually evolving with novel materials and coatings that enhance durability and performance. In many recent investigations, tribologists are focusing on understanding friction at the nanoscale, which opens up new avenues for reducing energy consumption in machines.
Importance of the Research in Its Respective Field
The importance of tribological research cannot be understated. It not only drives improvements in product lifetime but also enhances overall economic efficiency in manufacturing. Furthermore, advancements in tribology have direct implications for sustainability. By improving material efficiency and reducing waste, tribology contributes to more environmentally friendly practices across manufacturing processes.
Methodology
Description of the Experimental or Analytical Methods Used
Tribological studies utilize a variety of experimental setups to analyze material interactions. Whether it involves tribometers for measuring wear and friction coefficients or advanced imaging techniques like scanning electron microscopy, these methods provide detailed insights. Typical approaches can include
- Pin-on-disk tests: for assessing friction and wear.
- Block-on-block tests: for studying contact effects under varying loads.
Sampling Criteria and Data Collection Techniques
Data collection in tribological research often involves systematic sampling based on material types, surface conditions, and lubrication methods. By collecting data through reproducible tests, researchers can ensure results are comparable across different experiments. This rigorous approach allows for a deeper understanding of how specific conditions influence tribological performance.
"Tribology is not just an academic pursuit; it is a cornerstone of engineering innovation."
By integrating both theoretical and practical aspects, tribologists contribute invaluable knowledge that informs future technological advancements.
Prelude to Tribology
Tribology is a critical area of study that focuses on the phenomena of friction, wear, and lubrication. Understanding tribology is essential for numerous industries where material interactions can greatly affect performance and longevity. This article aims to shed light on the significance of tribology by detailing its principles, methodologies, and applications. The importance of tribology lies in its ability to optimize material use, enhance efficiency, and minimize wear-related failures. Moreover, the relevance of tribology permeates various sectors, informing engineers and scientists about the best practices in material interactions.
Definition and Scope
Tribology derives its name from the Greek word "tribos," meaning to rub. It encompasses the study and application of processes where surfaces interact. The scope of tribology is vast, ranging from fundamental research on surface interactions to practical applications in automotive, aerospace, and manufacturing industries. Tribologists engage in solving complex problems related to wear and friction, which can lead to mechanical failure if not addressed. A proper understanding of tribological principles allows industries to improve product designs and performances. This expertise also contributes to cost savings through reduced maintenance and enhanced durability of mechanical components.
Historical Context
The study of tribology is not a modern pursuit. Early understanding of friction dates back to ancient civilizations, where engineers grappled with the challenges of moving heavy objects. Over the centuries, the field of tribology evolved with advancements in materials science and engineering. Key milestones include the development of lubricants, which became widely recognized in the 19th century. With the rise of industrialization, researchers began to systematically investigate tribological phenomena, leading to the establishment of lubrication theory.
In the latter half of the 20th century, tribology gained formal recognition as a distinct discipline. The establishment of professional societies and conferences focused on tribology solidified its importance in science and industry. Today, tribology is an interdisciplinary field, integrating concepts from physics, chemistry, and engineering, making it crucial for advancing technology and ensuring sustainable practices.
The Science of Friction
Understanding friction is vital in tribology. Friction defines the force resisting the relative motion of solid surfaces. The study of friction helps in predicting how materials will behave under load, improving safety and efficiency across industries. Proper management of friction can enhance machine performance, reduce wear and tear, and extend the lifespan of components. This section covers three main types of friction:
Types of Friction
Static Friction
Static friction is the force that keeps two surfaces at rest relative to each other. Its significance lies in the fact that it prevents the initiation of sliding motion. The primary characteristic of static friction is its ability to adapt to the applied force until a certain threshold is met. It is often seen as a beneficial trait, especially in applications requiring stability. The unique feature of static friction is that it is typically higher than kinetic friction, which means it takes more force to start moving an object from rest than to keep it moving. An advantage of static friction is that it enables grip and traction, critical for applications in automotive and manufacturing sectors. However, one disadvantage is that if improperly managed, it can lead to unexpected failures when the limit is exceeded, causing sudden movement.
Kinetic Friction
Kinetic friction, also known as dynamic friction, occurs when two surfaces slide past one another. Its role is important in determining the energy loss during motion. A key characteristic of kinetic friction is that it generally has a lower coefficient than static friction, allowing for smoother motion once an object starts moving. In this article, kinetic friction is highlighted for its prevalence in moving parts such as gears and bearings. The unique feature of kinetic friction is its consistency, which can be predictable and manageable for engineers. One advantage is that it reduces the likelihood of stalling in machines. However, its disadvantage includes generating heat, which can lead to wear and require effective lubrication to minimize damage.
Rolling Friction
Rolling friction occurs when an object rolls over a surface, as seen in wheels or ball bearings. Its contribution to tribology is crucial, especially in reducing energy loss compared to sliding friction. The primary characteristic of rolling friction is its relatively low coefficient compared to static and kinetic friction, making it an efficient option for transportation and machinery. Rolling friction is particularly beneficial because it provides a way to mobilize heavy loads with minimal energy expenditure. However, one unique feature is that it can be influenced by factors like surface roughness and material properties, which may sometimes lead to instability in very soft materials. Its downside includes limitations in applications that require abrupt stop, as rolling friction does not provide as much grip.
Factors Influencing Friction
Several elements affect the behavior of friction in tribological systems. Factors such as surface roughness, materials compatibility, and lubrication significantly influence the overall coefficient of friction. The relationship of these factors must be carefully considered when designing components for high-performance applications. Among the key influences:
- Surface Characteristics: The texture and finish of surfaces directly affect friction levels. Smoother surfaces may lead to lower friction but may also be prone to wear.
- Materials: Different material combinations exhibit varying frictional properties. Metal on metal behaves differently than rubber on concrete.
- Environmental Conditions: Temperature and humidity can alter friction performance, as lubrication properties change with temperature.
"Managing friction effectively translates into enhanced performance, safety, and longevity of materials in application."
This knowledge base is crucial in pursuing advancements in tribology, opening pathways for innovative research and practical applications.
Wear Mechanisms
Wear mechanisms are central to understanding how materials perform over time under various operating conditions. These mechanisms help in elucidating the processes by which material loss occurs at the surface of interacting solid bodies. Understanding wear is vital for engineers and tribologists as it directly affects the longevity, reliability, and safety of industrial systems. Effective management of wear leads to better performance and reduced operational costs, impacting various fields like automotive engineering and manufacturing.
Types of Wear
Abrasive Wear
Abrasive wear occurs when hard particles or asperities on a surface scrape or grind against another surface. This process can lead to significant material loss over time. The key characteristic of abrasive wear is its reliance on contact pressure and relative motion. This type of wear is popular in environments with high mechanical forces, such as in heavy machinery or vehicles.
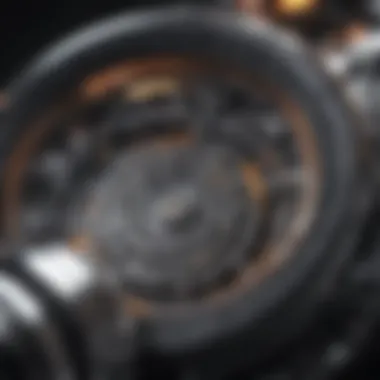
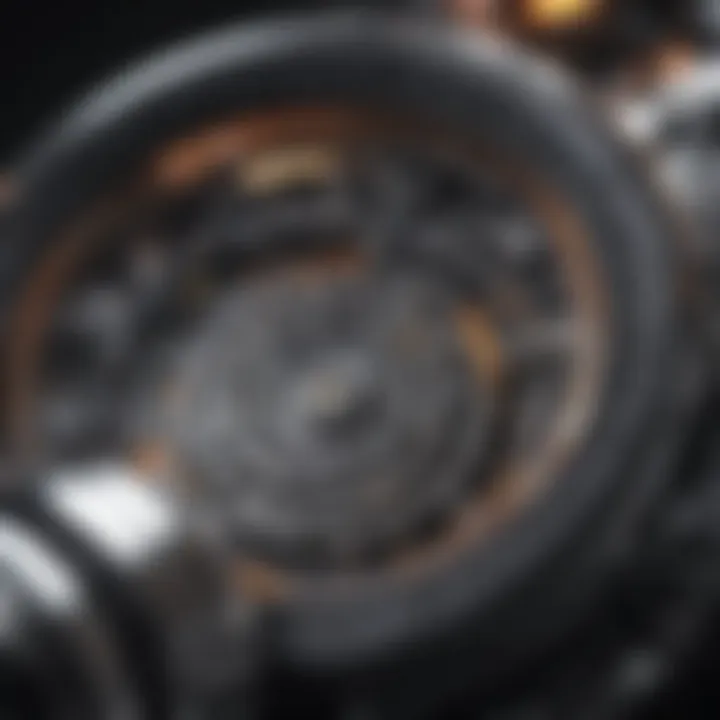
One unique feature of abrasive wear is that it often leads to the production of fine debris, known as wear particles, which can further exacerbate wear if not properly managed. Despite its challenges, recognizing the presence of abrasive wear can lead to informed decisions on material selection and surface treatment. It is beneficial because it helps in developing more wear-resistant materials, which is crucial for enhancing durability in complex assemblies.
Adhesive Wear
Adhesive wear happens when two surfaces adhere to each other at the molecular level and then separate. The key characteristic of adhesive wear is the transfer of material between surfaces. This type of wear is particularly relevant in sliding pairs, where surfaces are in close contact and experience high pressures.
The unique feature of adhesive wear is that it often creates valuable insights into the materials' compatibility in specific applications. Understanding this form of wear can help in selecting appropriate lubricants and surface coatings to minimize wear. While adhesive wear can lead to material deterioration, it also serves a beneficial role in defining the wear characteristics of new materials and surface finishing processes.
Cyclic Fatigue
Cyclic fatigue occurs when materials undergo repeated loading and unloading cycles, leading to the formation of cracks that can ultimately result in failure. A major characteristic of cyclic fatigue is its time-dependent nature, as wear accumulates over many cycles rather than affecting a material instantaneously.
Cyclic fatigue is crucial to consider in applications where components are subject to constant movement, such as in rotating machinery. The unique feature of this wear mechanism is its ability to predict the life span of materials used in critical components, enabling engineers to design systems with appropriate safety factors. Understanding cyclic fatigue also aids in improving manufacturing processes and material selections to extend the lifespan of components.
Impact of Wear on Materials
The impact of wear on materials is profound. Wear leads to microstructural changes, degradation of mechanical properties, and eventual failure. Engineers must consider wear characteristics when designing components to ensure longevity and reliability.
- Microstructural Changes: Wear can alter the surface morphology, changing how materials interact with each other.
- Loss of Material: As wear progresses, materials lose their integrity, leading to decreased performance.
- Economic Impact: Frequent replacements due to wear can result in increased costs for industries.
Understanding wear mechanisms allows for better material choices, enhanced lubrication strategies, and improved overall system performance.
Lubrication Techniques
Lubrication is a crucial aspect of tribology that focuses on reducing friction and wear between surfaces. Effective lubrication techniques enhance the performance and longevity of components, thereby improving the efficiency of machines and systems. Understanding the various lubrication methods is vital for engineers and tribologists to select the right approach for their specific applications. The right lubricant leads to optimal performance, reduced material degradation, and lower energy consumption.
Types of Lubricants
Lubricants can be categorized based on their composition and properties. Here are three primary types:
Synthetic Lubricants
Synthetic lubricants are engineered products designed for specific performance characteristics. They offer superior stability under extreme conditions compared to conventional oils. Some synthetic lubricants can withstand high temperatures without breaking down, making them a popular choice for high-performance engines and applications subject to severe conditions. Additionally, they often provide excellent film strength and corrosion protection.
Key characteristic: The custom formulation of synthetic lubricants allows for tailored viscosity and thermal properties.
Advantages:
- Exceptional temperature resistance
- Reduced volatility
- Longer service life
Disadvantages:
- Higher cost relative to conventional oils.
Mineral Oils
Mineral oils are derived from refining crude oil. They are more traditional lubricants commonly used in many applications due to their availability and cost-effectiveness. Mineral oils serve as the base for numerous lubricants used in the automotive and industrial sectors.
Key characteristic: Mineral oils exhibit a broad range of viscosities, making them suitable for diverse applications.
Advantages:
- Widely available and less expensive than synthetic options.
- Sufficient for many standard applications without specialized requirements.
Disadvantages:
- Lower thermal stability than synthetic lubricants, which can lead to faster degradation under extreme conditions.
Greases
Greases are semi-solid lubricants that combine a thickener with a lubricating oil. They can stay in place longer than liquids, making them effective for applications where liquid lubricants may not be practical. Greases is often used in environments with heavy loads or in conditions where sealing is essential.
Key characteristic: The ability to retain lubricating properties in high-load applications while resisting leakage.
Advantages:
- Extended lubrication intervals due to slow wear out.
- Good sealing properties, which can keep contaminants out of machinery.
Disadvantages:
- Limited ability to dissipate heat compared to oils.
Application of Lubricants
The application of lubricants is determined by several factors, including the type of system in which they will be used, operating conditions, and the expected lifespan of the machinery. Effective selection and application promote efficiency, protect against wear, and ensure optimal performance. Proper lubrication techniques also help in reducing environmental impact, as they can minimize lubricant leakage and waste.
Integration of modern technology, like automatic lubrication systems, allows for precision dosage and timing of lubricant application. This ensures that the right amount of lubricant reaches critical components, reducing risks of wear and enhancing overall machine life.
"The choice of lubricant can make a significant difference in the performance and efficiency of mechanical systems."
Tribological Testing Methods
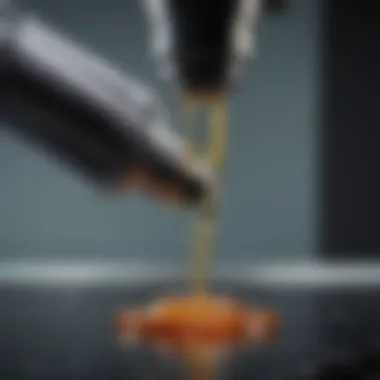
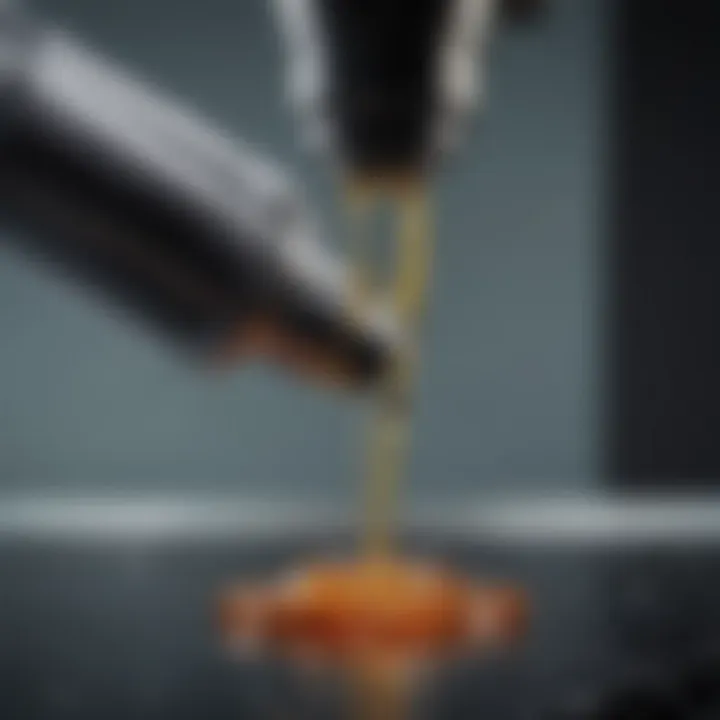
In the realm of tribology, understanding the interaction between surfaces in relative motion is vital. Tribological testing methods are crucial for evaluating the performance and durability of materials under specific conditions. These tests examine friction, wear, and lubrication properties, providing data essential for engineering applications. Without thorough testing, predicting how materials behave in real-world scenarios would be challenging, potentially leading to failure in crucial systems like machinery and vehicles.
The primary benefits of tribological testing methods include:
- Performance Assessment: These tests assess how different materials perform under varying loads and speeds, crucial for selecting materials in product design.
- Failure Analysis: They help in identifying wear mechanisms, allowing engineers to pinpoint causes of premature failure in components.
- Improving Formulations: Testing aids in the development of better lubricants, enhancing their effectiveness in different applications.
In addition, there are considerations to keep in mind when conducting these tests. Environmental factors, such as temperature and humidity, can significantly affect results, and care must be taken to replicate working conditions as closely as possible.
Standard Test Methods
Standard test methods form the foundation of tribological research. They are widely accepted protocols used to ensure consistent and reliable results across various studies. Well-known standards include the ASTM G77 for sliding wear and ASTM D2714 for lubricants.
Utilizing these standardized methods provides several advantages:
- Consistency: Adherence to established protocols allows for reproducibility of results.
- Benchmarking: Standard tests enable researchers and industries to compare materials and products effectively, helping in the selection process.
- Regulatory Compliance: Many industries require compliance with specific standards, ensuring safety and reliability in their applications.
Advanced Testing Techniques
As technology progresses, so do the methods for tribological testing. Advanced testing techniques, like scratch tests and pin-on-disk tests, occur at the nano and micro scales. Effective use of these methods can lead to:
- Enhanced Sensitivity: Advanced methods can detect subtler effects of friction and wear, which may not be apparent with standard tests.
- Realistic Simulations: Tests can simulate extreme environments, helping predict behavior in service conditions.
- Material Innovations: They allow for testing of new materials, facilitating innovation in product design.
In summary, tribological testing methods are indispensable in understanding material interactions and optimizing performance in various applications. Both standard and advanced methods play unique roles in research and industry, contributing to improved product longevity and efficiency.
"The role of tribological testing in predictive maintenance cannot be understated; it provides critical insights that save resources and extend equipment lifespan."
Awareness of testing methods links directly to sustainability goals, emphasizing the importance of selecting and using materials wisely. By employing these testing methods, industries can enhance their understanding of tribological outcomes, ultimately leading to better, more sustainable practices.
Applications of Tribology
The applications of tribology have a far-reaching impact across numerous industries. Successful tribological practices enhance efficiency, reduce wear and tear, and ensure the longevity of materials. Understanding the various applications of tribology allows professionals to harness its principles to optimize performance while minimizing costs. Tribologists analyze and address friction and wear, leading to improved design, manufacturing processes, and sustainability approaches.
In Automotive Industry
The automotive industry heavily relies on tribology for several reasons. Effective lubrication reduces wear on engine components, enhances fuel efficiency, and diminishes the likelihood of mechanical failures. Engine oil, for example, plays a critical role by forming a protective layer that minimizes direct contact between moving parts. Additionally, tribological testing helps in selecting suitable materials for gears and bearings, ensuring that they can withstand the extreme conditions present in automotive operations.
Moreover, advancements in tribology have led to the development of low-friction coatings and innovative lubricants that not only enhance performance but also contribute to energy savings and reduced emissions.
In Aerospace Engineering
In aerospace engineering, tribology is vital for safety and reliability. The high-speed components of aircraft, including engines and landing gears, experience significant stress and must operate under various conditions. Tribologists work on ensuring that lubricants and materials can withstand high-temperature environments and reduce wear efficiently.
Material compatibility is crucial in this sector. Tribological studies help in understanding how different materials interact under load, improving designs for durability. This is particularly important for parts like turbines, where tribological failures can lead to catastrophic results.
In Manufacturing Processes
Tribology plays a key role in manufacturing operations by improving the efficiency of machines and tools. In processes such as machining, cutting and forming, the right lubrication can drastically enhance tool life and surface finish of products.
An effective tribological system in manufacturing leads to:
- Increased productivity by reducing downtime.
- Lower costs associated with material wastage.
- Environmental benefits through the optimization of lubricant use.
Adopting effective tribological practices facilitates competitive advantages in a marketplace where sustainability and efficiency are increasingly demanded.
"The use of advanced tribological techniques in manufacturing not only increases the lifespan of tools but also contributes to the overall quality of the end product."
Through these specific applications, tribology makes an undeniable contribution to the functionality and efficiency of vital industries. Understanding these roles equips engineers and researchers with tools to innovate and improve, aligning with modern sustainability goals.
Recent Advancements in Tribology
Recent advancements in tribology have significantly reshaped our understanding of friction, wear, and lubrication. The integration of innovative technologies and methodologies has opened new avenues for research and practical applications. Analyzing these advancements is crucial, as they not only enhance performance across various industries but also contribute to sustainability efforts. By improving material interactions, these developments address the growing need for efficiency and environmental consciousness in modern engineering.
Nanotribology
Nanotribology is a subfield focusing on the interactions that occur at the nanoscale. This area of study is vital because of how friction and wear operate differently at such small dimensions. For example, traditional wear mechanisms may not apply in the same way when materials are reduced to nanoscale. The unique properties exhibited at this scale can lead to innovative solutions in engineering.
This research can lead to several benefits:
- Improved Material Performance: Understanding nanoscale interactions helps develop materials with enhanced wear resistance and durability.
- Enhanced Coatings: Advanced coatings can be designed to minimize friction and wear at the nanoscale, improving the longevity of various components.
- Energy Efficiency: By optimizing lubrication at nanoscale, we can lower energy loss in machines and engines.
Nanotribology also responds to the need for materials that minimize environmental impact. By developing lighter, more efficient systems, we can contribute to significant energy savings and reduced emissions.
Smart Lubrication Systems
Smart lubrication systems represent another breakthrough in tribology, integrating real-time monitoring with advanced control mechanisms. These systems can adjust the type and quantity of lubricant applied based on operational conditions, ensuring optimal performance. The importance of smart lubrication derives from several factors:
- Adaptability: They can respond to changing conditions, such as temperature and load, ensuring that lubrication remains effective under various scenarios.
- Reduced Consumption: By applying lubricant only when necessary, these systems reduce waste and overall lubricant consumption, contributing to sustainability efforts.
- Enhanced Reliability: With real-time data analysis, maintenance needs can be predicted, preventing breakdowns and extending the life of machinery.
"Smart lubrication systems not only improve efficiency but also represent a crucial step towards sustainable engineering practices."
Tribology and Sustainability
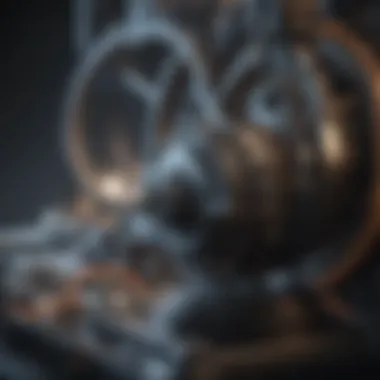
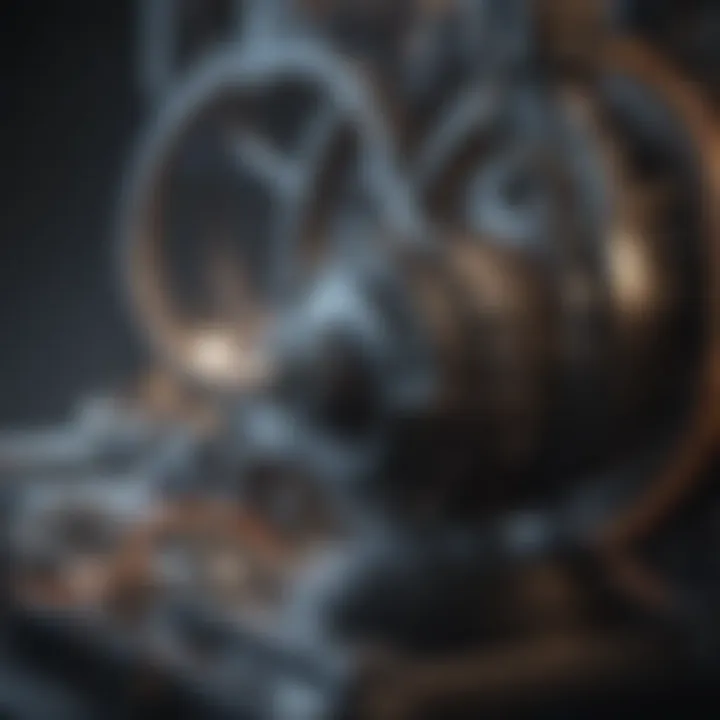
The intersection of tribology and sustainability is an increasingly vital topic in modern research and industry practices. This relationship centers on the reduction of waste and increased efficiency, which are essential for sustainable development. Tribology focuses on friction, wear, and lubrication; understanding these elements can lead to significant environmental benefits. Improved tribological designs not only enhance material performance but also contribute to a sustainable future by minimizing resource consumption and energy usage.
Modern industries face pressures to reduce their environmental footprint while maintaining high levels of performance. Tribologists play a crucial role in developing innovative solutions that align with sustainability goals. By optimizing material interactions and enhancing product life, they enable industries to reduce their reliance on raw materials and decrease waste.
Reducing Material Waste
Reducing material waste is one of the primary benefits facilitated by effective tribological practices. In many industries, the wear of components leads to regular replacements, resulting in substantial waste. Efficient lubrication techniques can minimize wear, extending the life of machinery and components. This not only preserves materials but also reduces the energy-intensive processes involved in producing new components.
- Examples of Tribological Methods
- Use of advanced coatings that provide better wear resistance.
- Implementation of friction-reducing lubricants in machinery.
- Design alterations in components to reduce unnecessary friction.
By actively implementing such practices, organizations report significant savings in material costs and a decrease in operational waste. Reducing waste ultimately supports a circular economy where materials are continuously reused and recycled.
Energy Efficiency in Tribological Applications
Energy efficiency is another critical consideration in the context of tribology and sustainability. The energy consumed in industrial processes can be significantly decreased through improved tribological practices. For example, effective lubrication systems reduce friction between moving parts, which translates to lower energy requirements for the same level of output.
Key factors for enhancing energy efficiency include:
- Optimized Lubrication Techniques: Adopting synthetic or high-performance lubricants can significantly decrease friction.
- Real-time Monitoring: Smart lubrication systems that adjust based on operational conditions help maintain optimal performance and reduce energy waste.
- Material Selection: Choosing materials with favorable tribological properties can enhance efficiency and reduce losses.
"Efficient tribological solutions have the potential to reduce energy expenditure by up to 30% in various industrial applications."
Challenges in Tribological Research
The field of tribology faces many challenges that researchers must navigate in order to advance their understanding of friction, wear, and lubrication. These challenges are critical, as they can profoundly influence material performance and longevity in various applications. Identifying and addressing these challenges is vital for the development of more efficient materials and systems.
Material Limitations
Material limitations represent a significant hurdle in tribological research. Different materials exhibit unique properties when it comes to friction and wear. Researchers must consider factors such as hardness, elasticity, and thermal stability. Each of these properties can drastically affect performance under varying conditions.
For instance, metals may exhibit high wear resistance, but they can also be prone to corrosion. Ceramics, while generally resistant to wear, can be brittle under stress. Polymers may offer flexibility, yet they might not withstand high temperatures or chemical exposure. This variety can complicate the selection of materials for specific applications. Therefore, researchers must conduct extensive testing and evaluation of materials to determine their suitability within tribological contexts.
Some ways to address material limitations include:
- Developing composite materials that combine the positive traits of different substances.
- Utilizing advanced manufacturing techniques, such as additive manufacturing, to create tailored solutions.
- Implementing real-time monitoring systems to collect data on material behavior in operational settings.
Environmental Considerations
Environmental issues present another challenge in tribological research. As industries strive for more sustainable practices, tribologists must consider the ecological impact of their work. The production and disposal of lubricants and materials can result in pollution and significant waste.
To combat these issues, researchers are focusing on:
- Developing biodegradable lubricants that minimize environmental harm while maintaining performance.
- Examining the life cycle of tribological materials to ensure their sustainability from production through disposal.
- Implementing green engineering principles to minimize waste and energy consumption in tribological applications.
Additionally, recent innovations in technology, such as smart lubrication systems, can enhance energy efficiency and reduce resource usage.
"Studies show that improving tribological performance can lead to up to 30% higher energy efficiency in machinery operations."
Future Directions in Tribology
The future of tribology is poised for significant evolution as the demands of modern technology and sustainability shape its trajectory. In an era where efficiency and environmental considerations are increasingly crucial, tribologists will play a vital role in developing innovative solutions that address these challenges. As industries strive to enhance performance, reduce waste, and minimize energy consumption, understanding the future directions in tribology becomes essential. This section delves into innovative research approaches and emphasizes the importance of interdisciplinary collaboration.
Innovative Research Approaches
Innovative research is paramount to drive the field of tribology forward. The blend of new materials and advanced techniques is essential to discover novel solutions. For instance, researchers are exploring coatings that can significantly reduce wear and friction. These coatings can be designed at a molecular level, providing precise control over their properties.
Moreover, the integration of machine learning and data analysis into tribological studies is gaining traction. By using these technologies, tribologists can analyze vast amounts of data to predict wear patterns and optimize lubricant formulations. This predictive capability allows for proactive measures in maintenance, enhancing the lifespan of mechanical systems. The advent of nanotechnology also opens further avenues. Materials engineered at the nanoscale can exhibit unique tribological properties, which can revolutionize tribological applications in automotive and aerospace fields.
Key points regarding innovative research approaches include:
- Development of advanced coatings for reduced wear.
- Application of machine learning to predict wear and optimize lubricants.
- Utilization of nanotechnology for enhanced performance.
Interdisciplinary Collaboration
Interdisciplinary collaboration is increasingly important in advancing tribology. The intersection of tribology with fields such as materials science, mechanical engineering, and environmental science offers unique opportunities for innovation. By working together, experts from various disciplines can approach existing problems with a fresh perspective.
For example, tribologists can benefit from the insights of material scientists in developing new substances for lubrication or wear resistance. Similarly, collaboration with environmental scientists can lead to the creation of sustainable lubricants that minimize ecological impact.
Engaging in cross-disciplinary research not only fosters innovation but also opens avenues for funding and resource sharing. Such collaboration may lead to breakthroughs in knowledge and technology that a single discipline might not achieve alone.
Significant aspects of interdisciplinary collaboration are:
- Combining expertise across different scientific fields.
- Development of sustainable and eco-friendly materials.
- Enhanced innovation through diverse perspectives.
Future Directions in Tribology are marked by innovative research and collaborative efforts, paving the way for a more efficient and sustainable industrial landscape.
Culmination
In examining the role of tribologists in both science and industry, it becomes evident that their contributions are fundamental to improving efficiencies and performances across various sectors. Tribology, which encompasses the study of friction, wear, and lubrication, plays a crucial part in the development and longevity of materials. Without effective tribological solutions, the performance of engines, machinery, and even everyday products would suffer significant degradation.
Summary of Key Insights
The main insights drawn from this exploration include:
- The Interdisciplinary Nature of Tribology: This field intersects multiple disciplines including physics, materials science, and engineering. Understanding its mechanics requires knowledge across various domains, making collaboration between experts vital.
- Technological Advancements: New materials and innovative lubrication techniques have transformed the way industries approach wear and friction. Recent advancements in nanotribology and smart lubrication systems demonstrate how these technologies are informed by high-level research.
- Sustainability Considerations: As environmental concerns rise, tribologists are focusing on optimizing solutions to reduce material waste and enhance energy efficiency. By minimizing frictional losses, significant savings can be found in energy consumption in various applications.
- Industry Applications: The role of tribology extends into numerous industries such as aerospace and automotive. The impact of tribological principles is evidenced in improved reliability of components, leading to enhanced safety and performance.
- Challenges and Future Directions: Material limitations and environmental considerations present ongoing challenges for tribologists. However, innovative research approaches and interdisciplinary collaborations offer a hopeful path for tackling these challenges.