TPU Adhesive: Properties, Applications, and Insights
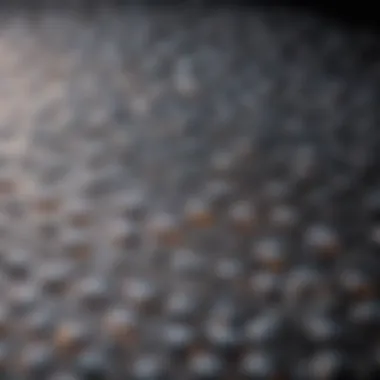
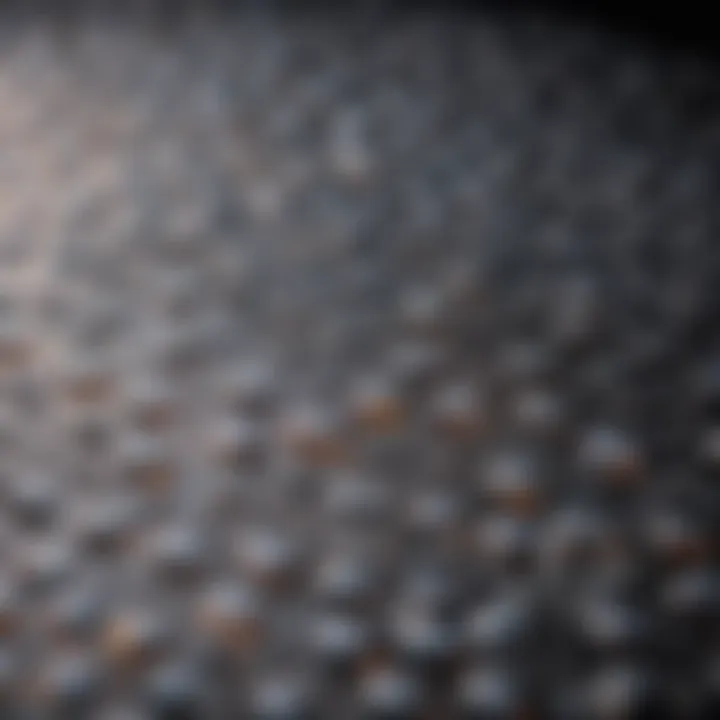
Intro
TPU adhesive has become increasingly significant in various industries due to its impressive mechanical properties and adaptability. This specialized adhesive plays a crucial role in product durability and functionality, which is vital for modern manufacturing processes. Its unique blend of flexibility, resilience, and weather resistance make it a go-to choice for engineers and designers alike. As the landscape of manufacturing evolves, understanding the core aspects of TPU adhesive, including its chemical composition, performance characteristics, and wide-ranging applications, is essential for professionals attempting to harness its potential.
Research Overview
Summary of Key Findings
After investigating the myriad properties and applications of TPU adhesive, several core findings emerge. Firstly, TPU adhesive exhibits exceptional binding strength across various substrates, including metals, plastics, and textiles. This versatility makes it applicable in sectors ranging from automotive to consumer goods. Notably, its ability to maintain its properties under extreme temperatures and conditions sets it apart from traditional adhesives. Additionally, TPU's resistance to wear and tear contributes to its longevity, making it a cost-effective solution in the long run.
Importance of the Research in Its Respective Field
The ongoing research into TPU adhesive is paramount for its application in developing advanced materials and products. As industries aim for more sustainable solutions, the environmental considerations associated with TPU adhesives, such as their recyclability and non-toxicity, significantly enhance their appeal. Understanding these properties not only aids manufacturers in making informed choices but also encourages innovation to meet market demands.
Methodology
Description of the Experimental or Analytical Methods Used
In the exploration of TPU adhesive properties, various analytical techniques have been employed. Mechanical testing helps in assessing the adhesive's strength and durability under different stress conditions. Thermal analysis is another essential aspect, offering insights into its thermal stability. Furthermore, viscosity measurements play a role in understanding application methods and curing behaviors. These experimental setups facilitate a comprehensive understanding of TPU adhesives, paving the way for breakthroughs in their utilization.
Sampling Criteria and Data Collection Techniques
The selection of TPU adhesive samples was systematic, ensuring a range of formulations was analyzed. Different brands and grades were included, allowing for comparative analysis. Data was collected using both qualitative and quantitative approaches, including lab tests and field studies to observe real-world performance. This combination of methodologies provides an accurate depiction of TPU adhesive's capabilities and delivers a rounded perspective on its advantages and limitations.
Prolusion to TPU Adhesive
Understanding TPU adhesive is vital for anyone engaged in diverse industrial applications, from automotive to textiles. This type of adhesive stands out because of its unique properties that merge flexibility and durability. It's not just another glue; TPU adhesives bring versatility to the table, allowing them to bond a multitude of materials effectively. This quality makes them an essential component in various manufacturing processes. Whether you're engineering electronic devices or creating high-performance footwear, TPU adhesive is likely your unsung hero.
Definition and Overview
Thermoplastic polyurethane (TPU) adhesive is a synthetic polymer that combines elements of urethane and plastic. This combination results in a material that is not only sturdy but also flexible, allowing for adaptations in numerous environments and applications. TPU adhesives are characterized by their excellent adhesion to surfaces such as metals, plastics, and even fabrics. These adhesives exhibit high elasticity, meaning they can stretch and flex without losing their bonding strength. Understanding the molecular makeup and the behavior of this adhesive can provide deeper insights into why it excels in so many areas.
In terms of functionality, TPU adhesives are often applied in both hot-melt and solvent-based formulations. Hot-melt TPU adhesives are particularly convenient for on-the-go applications, as they can be heated and applied quickly, making it easier for manufacturers to streamline their processes. The ability to work with these adhesives at varying temperatures adds another layer of versatility that other adhesive types might not offer.
Historical Background
The history of TPU adhesive can be traced back to the early development of polyurethane in the mid-20th century. Initially, polyurethane was primarily used in coatings and elastomers. Over time, as technology advanced and the demand for more versatile materials grew, researchers started to focus on combining polyurethane with thermoplastic materials. This led to the birth of TPU adhesives in the 1970s, marking a significant milestone in adhesive technology.
As industries evolved, so did TPU adhesives. Their exceptional properties caught the attention of aerospace and automotive sectors, where their ability to endure harsh conditions became crucial. By the 1990s, TPU adhesives were widely recognized as one of the best solutions available on the market for demanding applications. The rise of eco-conscious manufacturing also contributed to the development of bio-based TPU adhesives, further enriching the material's historical trajectory. Today, TPU adhesives are not only utilized for bonding but also play an essential role in sustainability efforts, proving the material's adaptability and enduring relevance.
Chemical Composition of TPU Adhesive
The chemical composition of TPU adhesives plays a critical role in determining their properties and suitability for various applications. Understanding the makeup of these adhesives helps in selecting the right type for a specific use. TPU, or thermoplastic polyurethane, combines the robustness of traditional rubber with the versatility of plastics. Knowing the specific components and their functions allows for better material manipulation during processing and end-use performance.
Polyurethane Basics
Polyurethane is a polymer composed of a chain of organic units joined by carbamate links. It has gained significant traction due to its diverse applications. At its core, the polyurethane structure can be adapted to create soft or hard materials, depending on the need. There are two primary forms of polyurethane: thermosetting and thermoplastic. For TPU adhesives, the thermoplastic variant is favored due to its flexibility and ease of processing.
In this chemical family, the isocyanate and polyol react to form a urethane linkage. This reaction can be optimized based on the desired performance characteristics, including factors like hardness, transparency, and resistance to chemicals. Thus, the ability to control these initial reactants allows formulators to tailor TPU adhesives to various applications, making them a go-to solution in many industries.
Components of TPU Adhesives
The composition of TPU adhesives typically consists of three main components:
- Isocyanates: These are the reactive agents responsible for forming the polymer network. Commonly used isocyanates include toluene diisocyanate (TDI) and methylene diphenyl diisocyanate (MDI).
- Polyols: These are alcohols with multiple hydroxyl groups. Polyols used in TPU production can vary in molecular weight and the structure, influencing the final product’s flexibility and hardness. They can be either polyether or polyester-based.
- Chain Extenders: These essentially link polymer segments, enhancing the elastic properties of the TPU. Chain extenders such as butanediol are often utilized to adjust the performance characteristics further.
Their precise ratios and types must be selected carefully to yield the desired flexural strength, elasticity, and thermal stability.
Curing Agents and Additives
Curing agents and additives are crucial for optimizing TPU adhesive formulas. These components modify the physical and chemical characteristics of the adhesive. Key additions can include:
- Curing Agents: These are substances that initiate the crosslinking reaction between the functional groups in the adhesive, leading to a polymer network. Their role is pivotal in enhancing the durability and resilience of the adhesive.
- Fillers: Often added to reduce costs or improve certain properties, fillers can enhance thermal stability and mechanical strength. They can also modify the viscosity of the adhesive, making it easier to apply.
- Plasticizers: These compounds increase the flexibility and workability of TPU. However, care must be taken as they can affect adhesion performance if not selected judiciously.
Each additive needs to be chosen with a clear understanding of its effects on end-use performance; the wrong combination could lead to a loss of adhesive strength or flexibility.
"The success of TPU adhesives heavily relies not just on the primary components but also on the careful selection of additives that complement the overall system."
Thus, the intricate dance of chemical components within TPU adhesives highlights their significant adaptability and performance capabilities across diverse applications.
Properties of TPU Adhesive
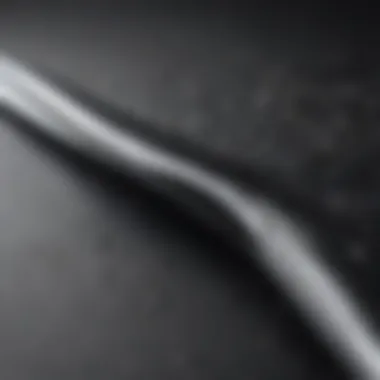
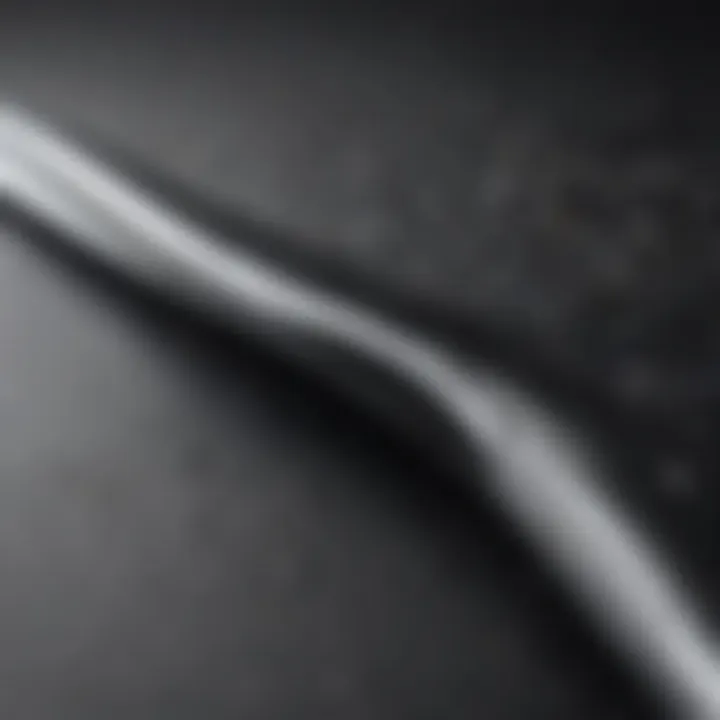
The properties of TPU adhesive hold significant weight in various contexts, from industrial applications to product design. Understanding these properties is crucial not only for scientists and engineers but also for anyone interested in the materials that shape our modern world. By diving into the mechanics of TPU, we can see how it stands out in performance and practicality compared to alternatives. This section explores some of the major attributes of TPU adhesive, including its mechanical properties, thermal stability, chemical resistance, and adhesion properties.
Mechanical Properties
Mechanical properties are central to determining how a material responds to applied forces and its durability under stress. TPU adhesives are known for their impressive tensile strength, which means they can withstand pulling forces without breaking. This strength is particularly vital in automotive applications, where the components are often subjected to significant stress.
Another aspect is flexibility. TPU adhesives can stretch and compress, making them suitable for bonding materials that experience movement. This resilience comes from the unique polymer structure of TPU, which allows for elastic deformation. Whether it's in flexible circuits or footwear, this characteristic greatly enhances performance, helping to absorb shocks and impact.
When it comes to tear resistance, TPU adhesives really shine. They resist tearing forces better than many traditional adhesives. This is essential in products like car interiors, where durability is paramount.
"The remarkable mechanical properties of TPU adhesives make them a dent in industries where performance truly matters."
Thermal Stability
Thermal stability is a significant consideration when evaluating adhesives, especially in industries like automotive and electronics where high temperatures can be the norm. TPU adhesives have excellent thermal stability, meaning they can endure considerable temperature fluctuations without degrading.
The thermal performance of TPU hinges on its composition and structure. In general, TPU can withstand temperatures ranging from -40°C to 80°C without significant loss of properties. This is essential in applications where materials may be exposed to both cold and heat, such as in outdoor products and automotive parts.
Moreover, TPU adhesives often require less specialized storage conditions than some other adhesives, providing more versatility in use. This stability allows manufacturers to save on costs while having confidence in the long-term performance of their adhesive solutions.
Chemical Resistance
In addition to mechanical stability and thermal robustness, TPU adhesives are noted for their chemical resistance. This property is crucial in many environments where adhesives may come into contact with oils, solvents, or acids.
TPU adhesives demonstrate resistance to a wide range of chemicals, making them applicable in the automotive and electrical industries. For instance, in electric connections, they can repel corrosive substances, ensuring longevity and reliability.
It’s also worth mentioning that this resistance can reduce the need for frequent replacements due to chemical degradation, which translates to lower costs and a smaller environmental footprint in the long run.
Adhesion Properties
Adhesion properties are integral to ensuring the effectiveness of any adhesive. TPU adhesive excels in bonding a variety of substrates, including metals, plastics, and fabrics. This versatility allows manufacturers to use TPU for different applications without switching adhesive types, streamlining processes and reducing overhead costs.
The molecular structure of TPU allows for interlocking and chemical bonding with substrates, increasing the bond's strength significantly. One of the critical benefits of TPU adhesion is its quick-setting nature, which enables faster production times. Updated formulations may also enhance these properties, giving manufacturers more options to consider.
In summary, the properties of TPU adhesive play a pivotal role in its widespread use across multiple fields. By leveraging its mechanical strength, thermal stability, chemical resistance, and superior adhesion capabilities, industries can create more reliable and effective products that stand the test of time.
Applications of TPU Adhesive
The significance of TPU adhesive in various sectors cannot be overstated. Its diverse applications stem from its unique properties like flexibility, high adhesive strength, and chemical resistance, which allow it to perform well in challenging environments. This section will delve into some key areas where TPU adhesive shines, highlighting its crucial role and benefits across industries.
In the Automotive Industry
TPU adhesives are crucial in the automotive sector, providing excellent bonding solutions for both interior and exterior applications. They are commonly used for attaching trims, seals, and even structural components due to their strong adhesion and flexibility. The automotive industry demands materials that can withstand a range of temperature variations while maintaining performance, and TPU adhesives rise to the occasion effortlessly. Furthermore, the lightweight nature of TPU contributes to overall vehicle weight reduction, enhancing fuel efficiency—a prime concern in today's market.
Electrical and Electronics
In the realm of electronics, TPU adhesives hold their own, especially for bonding components in devices like smartphones and computers. These adhesives demonstrate impressive dielectric properties, ensuring that they won’t interfere with electrical performance. Crucially, TPU can also resist moisture and chemicals, making it an ideal choice for protection against environmental factors. Therefore, from circuit boards to display screens, the versatility and reliability of TPU adhesives play a significant role in developing durable electronic products.
Footwear and Textile Manufacturing
When it comes to footwear, TPU is a game changer. Its flexibility and durability make it ideal for bonding various materials, from leather to synthetic fibers. Notably, TPU adhesives provide a comfortable fit and enhance the overall flexibility of the shoe without compromising on strength. This is especially beneficial for athletic shoes, where comfort and performance are paramount. Similarly, in textile manufacturing, TPU adhesives allow for innovative designs, facilitating the assembly of textiles with various functional features like waterproofing or breathability that consumers increasingly demand.
Medical Devices and Equipment
TPU adhesives find a formidable application in medical devices, where high sterility and performance standards exist. They are used in assembling parts of devices, such as syringes or diagnostic kits, that must endure exposure to body fluids, chemical disinfectants, and regular wear and tear. The biocompatibility of TPU makes it safer for medical use, ensuring that it does not react adversely when in contact with biological tissues. Given the ongoing advancements in medical technology, the ability to provide strong, durable bonds in this context is indispensable.
Construction and Building Materials
In construction, TPU adhesives are used in various bonding applications, including flooring and panel installations. The strength and flexibility of these adhesives make them well-suited for situations where building materials might expand or contract due to temperature changes. TPU can bond different materials effectively, such as wood, metal, and plastics, making it a popular choice for both structural and aesthetic applications. The durability ensures a longer lifespan for installations, contributing to overall project sustainability—an increasing concern in today's construction practices.
TPU adhesive, with its properties and applications, is indeed a cornerstone material that enhances the functionality and longevity of products across diverse sectors.
The landscape of TPU adhesive applications is expansive and continues to evolve. Its multi-faceted nature not only highlights the advancements in adhesive technology but also reflects on the growing demands of various industries. With constant developments, one can only expect the versatility and importance of TPU adhesive to further progress.
Advantages of TPU Adhesives
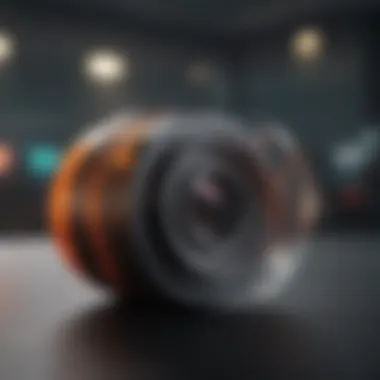
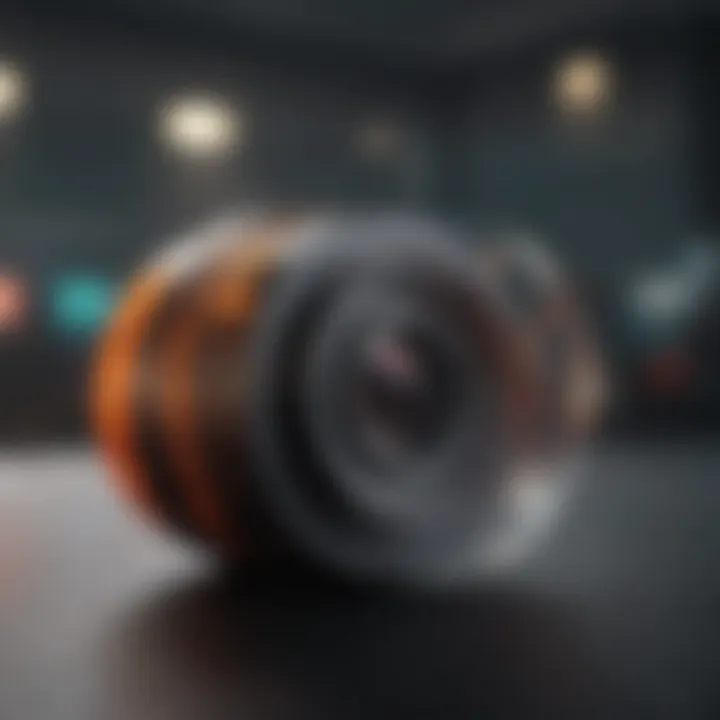
Understanding the advantages of TPU adhesives is crucial for anyone involved in manufacturing, product design, or material selection. These adhesives present a plethora of benefits that makes them stand out not just in theory but also in practical applications. The following key advantages provide a glimpse into why TPU has gained such a strong foothold across various industries.
Versatility and Flexibility
One of the hallmark features of TPU adhesives is their versatility. They can bond diverse materials including plastics, metals, and textiles with remarkable precision. This versatility extends to their flexibility, allowing them to adapt to a range of environmental conditions. For example, TPM adhesives maintain their adhesives properties across temperature fluctuations, making them suitable for both indoor and outdoor applications.
In automotive and construction, this flexibility means they can withstand stress and movement without breaking down. Consider a TPU adhesive used to bond parts of an automotive assembly—during operation, these parts experience vibrations and thermal expansions. A less adaptable adhesive might fail, while a TPU would hold strong.
Another area where versatility shines is in product design. For designers, the ability to use a single type of adhesive for various materials allows for streamlined workflows, resulting in cost and time savings. In a world where mixed-material approaches are more common, TPU adhesives are a practical choice.
Durability and Longevity
The durabality touted by TPU adhesives cannot be overlooked. These materials are notorious for their long-lasting performance and resistance to wear and tear. In industries such as footwear and medical devices, where wear can significantly affect performance and safety, using a reliable adhesive is paramount.
- Adhesion Strength: TPU adhesives consistently provide strong bonding that lasts long-term.
- Resistance to Environment: They can resist moisture, UV rays, and other environmental stresses, ensuring that the bonds remain intact over time.
In many real-world examples, TPU adhesives have endured the test of time. For instance, in the medical field, devices that utilize TPU adhesives tend to face constant exposure to not only handling but also various cleaning agents. A quality TPU adhesive ensures that the device remains safe for use and reduces the need for repairs or replacements.
Environmental Considerations
In an age where sustainability is not just a buzzword but a necessity, the environmental considerations surrounding TPU adhesives deserve attention. While traditional adhesives may involve harsh chemicals and carry significant ecological footprints, TPU adhesives often present a more eco-friendly alternative.
- Low VOC Emissions: Many TPU adhesives are formulated to emit low volatile organic compounds, making them safer for both the user and the environment.
- Recyclability: Certain types of TPU materials can be recycled, significantly reducing waste in manufacturing processes.
"TPU is not only a strong adhesive but also a material that aligns with the growing demand for sustainable practices in modern manufacturing."
Manufacturing Processes of TPU Adhesives
The manufacturing processes of TPU adhesives play a key role in determining their overall performance and suitability for various applications. Understanding these processes is essential for optimizing the properties of TPU adhesives and addressing industry-specific requirements. This section delves into the synthesis methods, formulation techniques, and quality control measures that are crucial for producing high-quality TPU adhesives.
Synthesis Methods
Synthesis methods are fundamental to the production of TPU adhesives. Typically, these adhesives are produced via a step-growth polymerization process, which involves the reaction of isocyanates with polyols. These reactions can be carried out through different pathways:
- One-shot process: Here, all components are mixed together simultaneously, allowing for a more rapid production but often requiring precise control to avoid inconsistencies.
- Prepolymer process: In this method, a prepolymer is formed first by reacting excess isocyanate with polyol. This stage allows better control over the molecular weight and the distribution of the resulting TPU.
The choice of method can greatly impact the properties of the final product. For instance, the one-shot method may yield a softer adhesive, while the prepolymer method usually results in a more durable adhesive. Furthermore, different polyols can be utilized to modify characteristics such as flexibility or hardness.
Formulation Techniques
Once the synthesis method is determined, formulation techniques are employed to tailor the TPU adhesives to specific end-use applications. This stage can involve the addition of various components such as plasticizers, fillers, and curing agents. Each additive alters the physical and chemical properties of the adhesive.
Common considerations in the formulation process include:
- Plasticizers: These are often incorporated to enhance flexibility. By lowering the glass transition temperature, a more pliable product is achieved.
- Fillers: Talc, calcium carbonate, or silica can be added to improve the mechanical strength or thermal stability of the adhesive.
- Curing agents: These are crucial for cross-linking the polymers, affecting the final adhesive's heat resistance, toughness, and overall durability.
The formulation must be carefully balanced. Too many fillers, for instance, can lead to an adhesive that is brittle and lacks adhesion properties.
Quality Control Measures
Quality control is indispensable in the manufacturing of TPU adhesives to ensure consistent quality and performance. Various measures can be instituted throughout the production process:
- Testing raw materials: Ensuring that the polyols and isocyanates used meet the required specifications before processing is essential. Any impurity can significantly affect the final product.
- Process monitoring: Real-time inspections and monitoring of parameters like temperature, humidity, and reaction time are crucial. Deviations can lead to subpar adhesive performance.
- Final product testing: After synthesis and formulation, rigorous testing is conducted to assess mechanical properties, adhesion strength, and thermal stability. This might involve using standardized methods such as ASTM testing protocols.
Quality control ensures that TPU adhesives perform reliably, enhancing their longevity and efficacy in various applications.
In summary, the manufacturing processes of TPU adhesives are integral in defining their properties and performance. By understanding and implementing effective synthesis methods, formulation techniques, and quality control measures, manufacturers can produce superior adhesives tailored to the specific needs of diverse industries.
Safety Considerations in Using TPU Adhesives
When working with TPU adhesives, understanding the associated safety considerations is paramount. These adhesives are utilized across various industries, and while they offer numerous advantages, proper handling and application are essential to mitigate risks. By taking safety seriously, manufacturers and consumers can avoid mishaps and promote a safer work environment. Let's delve into the key hazards and risks involved, as well as the necessary precautions that can safeguard individuals.
Hazards and Risks
TPU adhesives, like any chemical substance, come with their share of hazards. Awareness of these can help individuals act sensibly and minimize accidents. Among the main risks involved are:
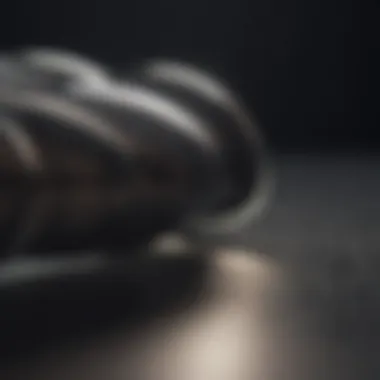
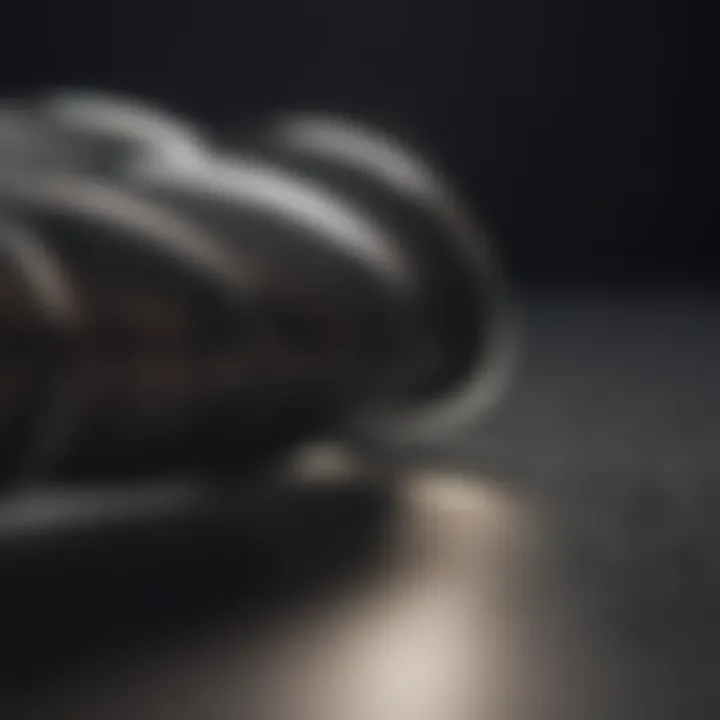
- Skin and Eye Irritation: Direct contact with TPU adhesive can lead to irritation or allergic reactions on the skin. Additionally, splashes into the eyes can result in serious discomfort.
- Fumes and Inhalation Risks: During application and curing processes, some TPU adhesives may emit fumes. Inhaling these can cause respiratory issues or exacerbate underlying conditions.
- Fire Hazards: Certain TPU adhesives are flammable. This risk heightens in environments with open flames or high heat.
"Understanding the hazards is the first step to ensuring safety when using TPU adhesives. It’s not just about what’s being used, but also how it’s being managed."
Recognizing these hazards means users can implement strategies to minimize impact. Proper ventilation, careful handling, and immediate attention to spills are fundamental practices.
Personal Protective Equipment (PPE)
Utilizing appropriate PPE is a crucial preventive measure when working with TPU adhesives. It’s not just an afterthought; it's a necessity. The right gear can make a significant difference in maintaining safety and health. Here’s what should be considered:
- Gloves: Wearing chemical-resistant gloves can protect against skin irritation and absorption of adhesives into the bloodstream.
- Safety Goggles: To safeguard the eyes from splashes, using protective eyewear is essential. This ensures that any accidental contact is mitigated.
- Respirators: In instances where there’s substantial fume generation, respirators are vital. This equipment helps filter harmful particles and gases from the air.
- Protective Clothing: Employing long-sleeve shirts or aprons made of resistant materials can shield the skin and clothing from spills.
It’s also important to always review Material Safety Data Sheets (MSDS) for specific TPU formulations. These documents provide detailed information on hazards, safe use, and emergency protocols.
Future Trends in TPU Adhesives
As we look ahead, it's clear that the world of TPU adhesives is evolving at a breathtaking pace. The importance of this topic can't be overstated, especially for industries relying on cutting-edge materials and innovations. Understanding future trends in TPU adhesives allows professionals to stay ahead of the curve, anticipate changes in demand, and adapt to new developments that may influence market dynamics and applications.
Research and Development Directions
In the realm of TPU adhesive, research and development are crucial for pushing boundaries. A significant focus is on enhancing properties that cater to specialized applications. For instance, ongoing studies delve into developing TPU formulations that offer greater adhesion under extreme conditions, such as high temperatures or fluctuating humidity levels. Researchers are also examining nano-additives that can improve mechanical properties without drastically altering the polymer's overall structure.
In addition, there's a surge in biocompatible TPU adhesives being explored. These factors are particularly relevant in sectors like medical device manufacturing, where safety and performance are paramount.
Moreover, the integration of smart technology—such as sensors and real-time monitoring—is transforming TPU adhesives into intelligent materials. They could offer feedback on environmental conditions or structural integrity, which is a giant leap for sectors focusing on safety and durability.
Sustainability and Eco-friendly Alternatives
Sustainability trends are at the forefront now more than ever, pushing manufacturers to rethink their materials and processes. There's a growing emphasis on using eco-friendly alternatives in producing TPU adhesives. Many producers are now exploring bio-based raw materials that can reduce the carbon footprint associated with traditional petrochemical sources. This switch not only helps in complying with stringent environmental regulations but also appeals to an eco-conscious clientele.
In addition to alternative raw materials, innovations in recycling processes for TPU adhesive waste are gaining traction. Techniques that allow for the reclamation of TPU from end-of-life products for reuse are being researched, promoting a circular economy.
Furthermore, consumers and regulatory bodies alike are pushing for transparency in material sourcing and product lifecycle assessments. This aligns with a broader global movement toward sustainability and responsible manufacturing, encouraging TPU adhesive developers to adopt greener practices.
"The future of TPU adhesives lies in innovation and sustainability. As industries evolve, the need for eco-friendly, high-performing materials becomes imperative."
Case Studies of TPU Adhesive in Practice
Case studies serve as a valuable lens through which one can observe the real-world application of TPU adhesive. By diving deep into specific industries where this adhesive shines, we can highlight its remarkable versatility and performance. These explorations not only underscore the strengths of TPU adhesives but also illustrate how various sectors are leveraging these materials to achieve superior outcomes. Understanding these elements provides critical insights into the economic and functional importance of TPU adhesives in contemporary manufacturing and product design.
Successful Applications in Industry
The success stories of TPU adhesives across various industries are numerous and varied. For instance, in the automotive sector, TPU adhesive is used extensively for bonding components that require flexibility yet maintain integrity under stress. A noteworthy example is its use in bonding windshield assemblies. The unique properties of TPU allow for better shock absorption and provide a water-tight seal, crucial for vehicle safety.
In the electronics industry, the adhesion of connectors and displays relies heavily on TPU. One standout case involved a manufacturer of wearable tech devices. The TPU adhesive used enabled thin, flexible designs while ensuring robust performance in terms of temperature and moisture resistance. The adhesives not only secured the technology in place but also contributed to the overall durability of the products.
Moreover, the footwear industry has seen an uptick in the adoption of TPU adhesives, particularly in the assembly of athletic footwear. Major brands have turned to TPU adhesives for their ability to bond various materials like rubber, leather, and synthetic fabrics. This has resulted in products that are not only lightweight but also offer excellent performance under different conditions, emphasizing TPU’s adaptability.
The application of TPU adhesive is a game changer, showcasing how innovation drives industry standards forward.
Comparative Analysis with Other Adhesives
When considering the wide spectrum of adhesives available today, a comparative analysis reveals TPU's distinct advantages. For example, when pitted against traditional epoxy or cyanoacrylate adhesives, TPU adhesive holds its own when discussing flexibility and elasticity. While epoxies are known for their high strength, they tend to be rigid once cured, which can be a disadvantage in applications requiring movement or expansion.
In contrast, cyanoacrylates, while fast-acting, can become brittle over time, leading to potential failure in dynamic applications. TPU adhesives combine the strengths of both—providing sufficient bond strength while maintaining flexibility, which is vital for applications subject to various stresses.
Furthermore, the long-term durability of TPU adhesives stands out in environments with extreme temperatures and stress factors. In processes like construction and manufacturing, where longevity is key, TPU adhesive meets and often exceeds the performance of its counterparts. This has led many companies to prefer TPU adhesives for critical applications, where reliability and adaptability are non-negotiable.
Through these case studies and comparative insights, it's clear that TPU adhesives not only hold their ground but also redefine possibilities across industries. Such an understanding is paramount for students, researchers, educators, and professionals who seek to navigate the complexities of modern material usage.
End
Drawing to a close, the exploration of TPU adhesive reveals its multifaceted nature and undeniable significance across various industries. The journey through its chemical composition, properties, and applications underscores just how integral TPU has become, bridging gaps in multiple sectors. Its unique characteristics, combining flexibility, durability, and chemical resistance, make it a go-to choice in industries ranging from automotive to electronics.
The benefits of using TPU adhesive are evident. Its versatile formulations allow for customization, catering to specific needs across different applications. Furthermore, the growing emphasis on sustainability has pushed TPU to the forefront, as manufacturers seek eco-friendly solutions without sacrificing product efficacy.
Key Takeaways on TPU Adhesive
- Versatility: TPU adhesives can be tailored for various applications, ensuring optimal performance in different environments and conditions.
- Durability: These adhesives exhibit outstanding longevity, making them suitable for high-demand situations, especially in construction and automotive sectors.
- Safety: Understanding safety considerations when using TPU adhesives is critical. Employing proper PPE can mitigate risks, ensuring a safer working environment.
- Future Potential: Ongoing research and development in the realm of TPU adhesives hints at even broader applications and improvements, particularly regarding sustainability.
"The advancement of TPU technology not only serves the demands of today but also sets the stage for innovations that will shape industries of the future."
In sum, TPU adhesive stands out not merely as an adhesive but as a catalyst for innovation across various fields. Its inherent properties and adaptability ensure it remains a relevant and vital component in modern manufacturing and design.