Understanding Electrical Insulating Varnish: Key Insights
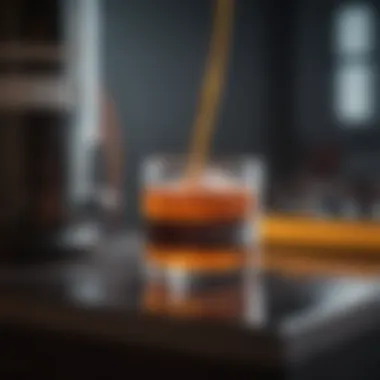
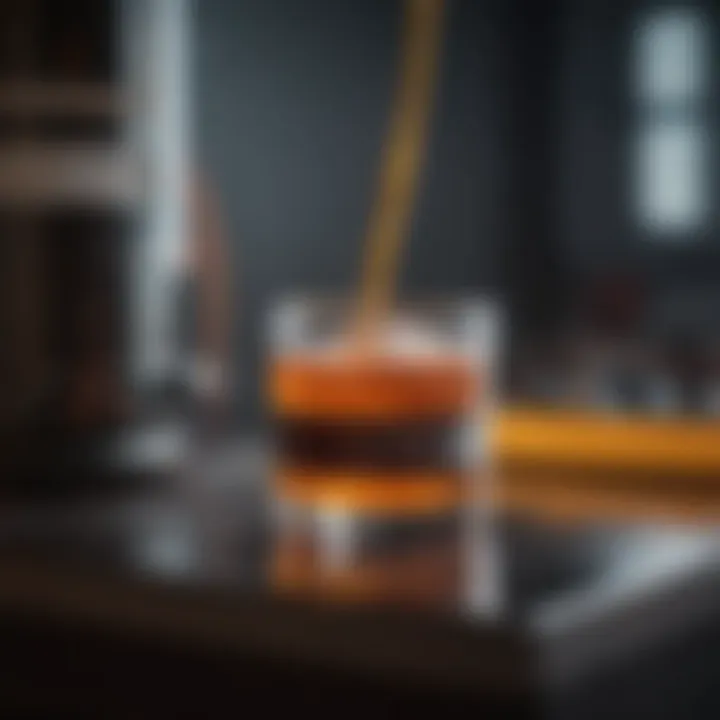
Intro
Electrical insulating varnish serves as a fundamental component within the realm of electrical engineering. As the complexity of electrical devices increases, the materials protecting these systems also require advancements. Insulating varnish not only provides necessary insulation but also enhances the mechanical strength, thermal stability, and protection against moisture and contaminants. This makes an understanding of this material vital for students, researchers, and professionals alike.
Research Overview
Summary of key findings
The exploration of electrical insulating varnish reveals a diverse range of formulations and their specific properties. Different types of varnishes, such as polyurethane, epoxy, and silicone-based varieties, are engineered for unique applications. For instance, polyurethane varnishes exhibit excellent flexibility and are often preferred in motors and transformers.
Beyond just electrical insulation, varnishes contribute to the longevity and performance of electrical components. Each formulation alters the electrical, thermal, and mechanical properties, tailoring the varnish for specific use-cases. Moreover, the recent advancements in varnaging technologies highlight a trend toward more environmentally friendly materials.
Importance of the research in its respective field
Understanding the properties and applications of electrical insulating varnish is essential for ensuring the reliability of electrical and electronic systems. As industries shift towards sustainable practices, recognizing advancements in varnish formulations will help guide manufacturers in making informed choices. This knowledge is particularly relevant as device miniaturization and the push for high-performance materials continue to influence design criteria in the electronics sector.
Current Trends in Electrical Insulating Varnish
- Environmentally Friendly Formulations: With growing concern for environmental impact, there is a shift toward water-based varnishes, which can provide similar performance with reduced harmful emissions.
- Nano-coatings: The incorporation of nanotechnology in varnishes is an emerging trend, enhancing thermal and electrical properties significantly.
- Smart Varnishes: Developments in smart materials have led to varnishes that can monitor their condition and report performance metrics in real-time.
End
In summary, the study of electrical insulating varnish encompasses much more than merely understanding insulation. With the evolving landscape of electronic devices, a comprehensive grasp of varnish properties engages critical insights into future innovations and challenges within this field. As such, tackling compliance with environmental regulations becomes equally important. This dual focus ensures that as we progress, we do so without compromising on safety or sustainability.
"Electrical insulating varnish is not just about insulation; it's a key enabler of reliability and performance in modern electronic systems."
Prolusion to Electrical Insulating Varnish
The study of electrical insulating varnish holds significant value in the context of electrical and electronic applications. This section aims to elucidate the fundamental aspects of insulating varnish, providing a clear understanding of its definition, purpose, and historical context. Many industries rely heavily on effective insulation to prevent electrical failures, which can lead to costly downtimes or even hazardous situations. Therefore, an exploration of insulating varnishes is essential for professionals and students alike who engage with electrical engineering or technology development.
Definition and Purpose
Electrical insulating varnish is a specialized resinous coating applied to various electrical components. Its primary purpose is to insulate and protect these components from moisture, dust, and other detrimental environmental factors. By minimizing the risk of short circuits, varnish plays a crucial role in enhancing the performance and life span of electrical devices.
This varnish acts not only as an insulator but also as a barrier against chemical agents that could degrade the components. The properties of insulating varnish can be tailored to meet specific requirements of different applications, providing flexibility and efficiency in design.
Historical Background
The journey of electrical insulating varnish dates back to the early developments of electrical technology. Historically, engineers relied on natural resins and oils to insulate electrical windings. With the advent of synthetic materials in the mid-20th century, the quality and performance of insulating varnishes improved markedly.
Initially, products such as shellac were commonly used. However, as technology progressed, the industry shifted towards more advanced materials, like epoxy and silicone-based varnishes. These innovations responded to the growing demand for efficiency and reliability in electrical systems. As electrical devices became more sophisticated, the need for more durable and heat-resistant varnishes surged.
Today, the production of electrical insulating varnish embraces both traditional and modern techniques, striving to achieve uncompromised quality while adhering to environmental and industry standards. Understanding the evolution of these varnishes provides insight into their current applications and innovations.
Composition of Electrical Insulating Varnish
The composition of electrical insulating varnish holds significant importance in dictating its performance and application. Understanding the elements that combine to form varnish allows professionals to choose the right varnish for specific electrical and electronic requirements. Each component contributes unique benefits, enhancing the functionality and durability of electrical devices.
Resins and Binders
Resins form the backbone of insulating varnish. They play a crucial role in the varnish's adhesion properties and in setting the overall characteristics of the coating. Common types of resins include epoxy, polyurethane, and silicone. Each resin type brings its own set of advantages:
- Epoxy Resins: Known for their excellent thermal and chemical resistance, epoxy resins create a strong bond and high dielectric strength.
- Polyurethane Resins: These offer flexibility and durability, suitable for applications that experience mechanical stress.
- Silicone Resins: With outstanding thermal stability, silicone resins perform well in high-temperature environments.
Binders blend the resins and fillers together, ensuring consistency in application. Efficient binding is critical, as it affects the varnish's ability to adhere to various substrates.
Fillers and Additives
Fillers and additives enhance the performance of electrical insulating varnish. Fillers, such as silica or calcium carbonate, improve the mechanical properties of varnish. They can also optimize viscosity and ensure uniform dispersion of the varnish during application.
Additives are incorporated to impart specific qualities:
- UV Stabilizers: Protect the varnish from degradation when exposed to sunlight.
- Antimicrobial Agents: Prevent mold or bacteria growth, particularly useful in humid environments.
- Plasticizers: Improve flexibility and workability, essential for applications with temperature variations.
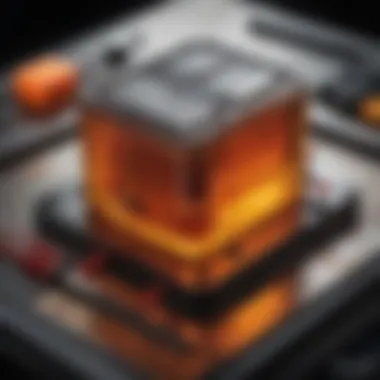
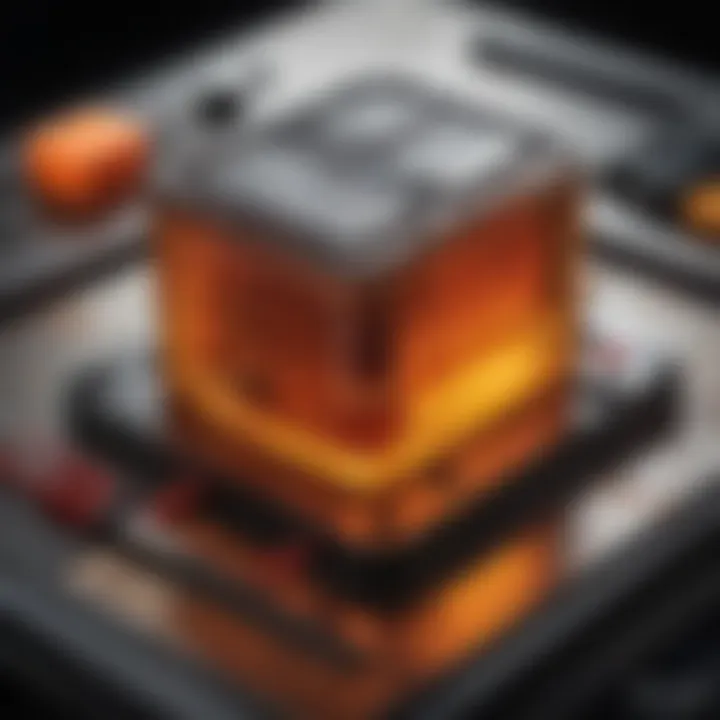
These components ensure that the varnish not only serves the basic insulating purpose but also withstands environmental challenges.
Solvents and Thinners
Solvents and thinners are vital for controlling the consistency and application properties of electrical insulating varnish. They aid in achieving the desired viscosity, facilitating smoother application processes.
Common solvents include xylene and toluene, which evaporate after application, leaving the solid varnish behind. Thinners can be helpful for the following:
- Adjusting Viscosity: Allows the varnish to flow and level better during application.
- Improving Application Properties: Ensures an even coating without clogs or imperfections.
- Cleaning Equipment: Makes it easier to clean brushes and tools used during application.
The choice of solvents and thinners can also affect the curing time and environmental impact, making their selection an important aspect of varnish formulation.
The right composition of electrical insulating varnish is essential for achieving optimal performance in a variety of applications. It is a blend of chemistry that delivers protection, insulation, and longevity to electrical components.
In summary, the composition of electrical insulating varnish is a crucial area of study that influences its effectiveness in practical applications. Understanding resins, fillers, additives, solvents, and thinners helps identify suitable varnish types for specific electrical tasks.
Types of Electrical Insulating Varnish
Understanding the various types of electrical insulating varnish is vital for those involved in electrical and electronic applications. The correct type can greatly impact performance, longevity, and reliability of devices. Each type possesses distinct properties that cater to specific needs in manufacturing and maintenance processes. Factors such as thermal stability, adhesion, and chemical resistance play a crucial role in the selection of varnish types. A diverse array of insulating varnishes allows engineers to tailor solutions to specific applications, minimizing risks associated with operational failures.
Polyurethane Varnishes
Polyurethane varnishes stand out for their excellent combination of flexibility and mechanical strength. They are often used in environments where vibrations and movements are common. This varnish type also exhibits exceptional adhesion properties, ensuring a robust bond to various substrates. Additionally, polyurethane varnishes have good resistance to abrasion, making them suitable for coatings that endure wear and tear. Although the curing process can take time, the finished product proves resilient under diverse conditions. This varnish type is ideal for applications in electric motors and coils where durable protection against external factors is necessary.
Silicone Varnishes
Silicone varnishes are noteworthy for their remarkable heat-resistant qualities, easily withstanding high temperatures without degrading. They offer considerable thermal stability, making them suitable for electrical components exposed to extreme conditions. Furthermore, silicone varnishes yield excellent dielectric properties, ensuring effective insulation. This characteristic is particularly advantageous in applications involving electrical transformers and high-power equipment. The flexibility of silicone varnishes also allows for the accommodation of thermal expansions typical in various industrial settings. Proper application enables the varnish to form a protective layer around circuits, enhancing their longevity.
Epoxy Varnishes
Epoxy varnishes are widely recognized for their superb adhesion and strong chemical resistance. They harden into a rigid structure that effectively shields components from moisture and corrosive elements. Their exceptional dielectric strength makes them suitable for applications that require high insulation, such as printed circuit boards and generator windings. The challenge with epoxy varnishes lies in their relatively longer curing times. Their application requires careful attention, as a poorly applied layer can lead to incomplete curing. Nevertheless, the durability and optimal performance of epoxy varnishes justify their use in demanding scenarios where reliability is crucial.
Acrylic Varnishes
Acrylic varnishes are gaining recognition for their balance between flexibility and hardness. They exhibit good weather resistance, making them suitable for both indoor and outdoor electrical applications. These varnishes dry quickly, reducing downtime during manufacturing processes, and are easier to clean up since they are often water-based. However, their resistance to chemicals is relatively lesser when compared to epoxies and polyurethanes. This may limit their use in harsh environments. They can be an excellent choice when quick turnarounds and moderate protection are needed, such as in consumer electronics or low-voltage applications.
"Each type of electrical insulating varnish serves unique roles in enhancing device reliability and performance. The choice should align with specific application demands."
By understanding these types of varnishes, engineers and technicians can make informed decisions, optimizing the application of electrical insulating varnishes in their respective domains.
Properties of Electrical Insulating Varnish
The properties of electrical insulating varnish play a critical role in determining its functionality and effectiveness in various applications. Understanding these properties is essential for professionals in the electrical and electronic industries. It helps in choosing the right varnish for specific needs, ensuring reliability and longevity of electrical components. Key properties include dielectric strength, thermal stability, chemical resistance, and adhesion as well as cure times. Each of these aspects affects performance under operational conditions and contributes to the overall durability of the varnish.
Dielectric Strength
Dielectric strength refers to the maximum electric field a material can withstand without failure. For electrical insulating varnish, this property is vital. A high dielectric strength ensures that the varnish can effectively prevent electrical breakdown in devices, protecting them from short circuits and other electrical failures. Typical values can range from 10 to 40 kV per millimeter, depending on the varnish formulation.
Moreover, this strength impacts the performance of electric motors and transformers, as it prevents arcing and enhances insulation integrity. When evaluating insulating varnish for a given application, its dielectric strength should be thoroughly assessed against the operating voltage of the device it will encase.
Thermal Stability
Thermal stability is another key property that electrical insulating varnish must possess. It reflects the varnish's ability to maintain its physical and mechanical properties at elevated temperatures. Electrical devices often operate in conditions where heat generation is significant. If a varnish loses its insulating properties under thermal stress, it can lead to failures or reduced performance in the device.
Good thermal stability allows the varnish to remain effective over a range of temperatures, thus extending the lifespan of electrical components. Formulations often incorporate materials that enhance thermal resistance. It is advisable to check the thermal properties of the varnish in alignment with the operating environment, as different applications may have varying heat requirements.
Chemical Resistance
Chemical resistance is vital for insulating varnish, particularly in applications exposed to solvents, oils, and other corrosive substances. A varnish that lacks chemical resistance can degrade quickly, leading to compromised insulation and malfunctions. The ongoing interaction with various substances within electrical environments makes this property crucial.
For instance, in automotive applications, the varnish must withstand engine oils and fuels. Evaluating the compatibility of varnish with potential chemical exposures can significantly influence the decision-making process. Varnishes formulated with additives for improved chemical resistance can offer better protection against harsh environments.
Adhesion and Cure Times
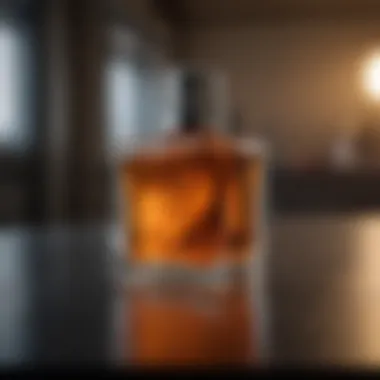
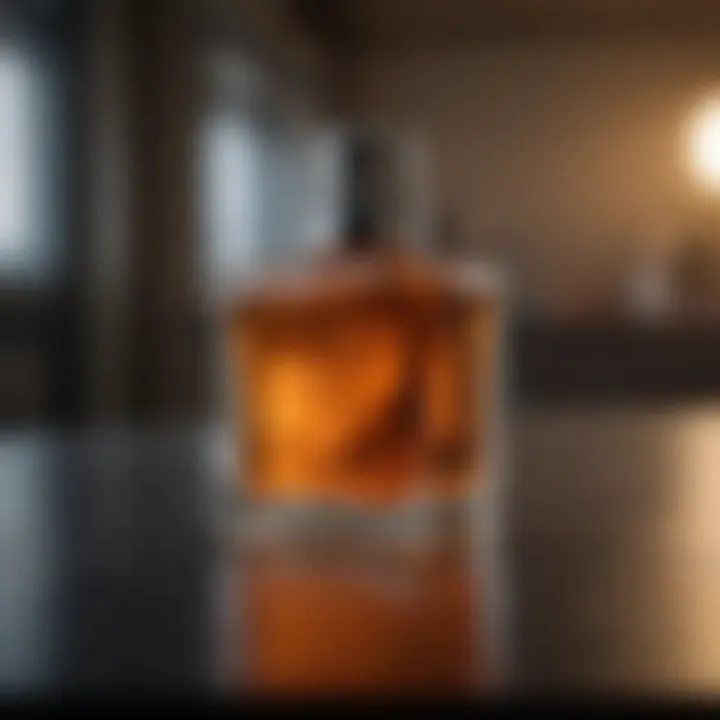
Adhesion refers to how well the varnish adheres to the surface of the materials it is applied to. Strong adhesion is essential for ensuring the complete enveloping of electrical components, preventing moisture ingress, and maintaining system integrity.
Cure times are equally important. They determine how quickly the varnish reaches its optimal performance after application. Fast cure times are beneficial in large-scale manufacturing processes, allowing for quicker assembly of devices. However, the right balance must be found, ensuring that cure speed does not compromise the quality and effectiveness of the insulating layer.
Evaluating both adhesion properties and cure times on different substrates can be essential for manufacturers aiming for high efficiency and durability in their products.
Application Areas of Electrical Insulating Varnish
The application areas of electrical insulating varnish are critical for understanding its role in various electrical and electronic devices. These varnishes play a significant part in safeguarding components against environmental stressors, thus enhancing performance and longevity. It is essential to know where and how these varnishes are utilized, as their properties can highly influence device reliability and functionality.
Electric Motors
Electric motors are ubiquitous in modern machinery, ranging from household appliances to industrial equipment. The use of electrical insulating varnish in electric motors primarily serves to encase windings and prevent short circuits. This insulation ensures that electrical currents flow properly without leakage, which can lead to overheating and eventually, motor failure.
The varnish also enhances moisture resistance, making motors more robust against environmental factors. Customized formulations of insulating varnish can provide adequate thermal stability, which is essential for motors that operate over a wide range of temperatures. As a result, the longevity and efficiency of electric motors increase significantly when the appropriate insulating varnish is applied.
Transformers
Transformers are vital for voltage regulation in electrical systems. The insulation provided by varnish layers is crucial in maintaining dielectric strength. It prevents electrical breakdown between the windings, which can lead to catastrophic failures. The application of electrical insulating varnish helps in reducing losses due to corona discharge and enhances the thermal management of transformers.
Moreover, the varnish protects against chemical exposure, ensuring that the materials remain intact for extended periods. This characteristic is particularly important in outdoor installations where transformers may be subjected to humidity and pollutants. Using high-quality insulating varnish can thus improve safety and maintain operational reliability in electrical networks.
Generator Windings
Generator windings need significant insulation to function safely, especially in power generation settings where high voltages are commonplace. Electrical insulating varnish creates a protective barrier that enhances the dielectric properties of the windings. This barrier is critical in preventing insulation failure, which can lead to significant downtimes and repair costs.
The varnish also plays a role in ensuring that windings remain thermally stable under varying loads. A properly coated winding will better handle temperature fluctuations and maintain optimal performance. The resilience offered by varnish leads to improved generator efficiency and less frequent maintenance.
Printed Circuit Boards
Printed circuit boards (PCBs) are at the heart of most electronic devices today. The application of electrical insulating varnish on PCBs is necessary to provide both electrical insulation and physical protection from moisture and contaminants. A good insulating varnish can enhance the mechanical strength of the PCB, preventing fractures and damage during manufacturing and use.
In addition, the varnish helps in reducing electromagnetic interference, thus improving the overall performance of the electronic device. This is particularly important for high-frequency applications where signal integrity is paramount. Innovations in varnish formulations continue to improve their adhesion and performance on PCBs, making them more effective in protecting delicate electronic components.
"Electrical insulating varnish is the unsung hero in modern electrical design, providing essential protection to machinery and devices across numerous industries."
To summarize, the application areas of electrical insulating varnish are extensive and varied. Whether in electric motors, transformers, generator windings, or printed circuit boards, the protective properties of varnish ensure that devices operate effectively and efficiently. Thus, understanding these applications is crucial for anyone involved in the field.
Innovations in Electrical Insulating Varnish
Electrical insulating varnish plays a pivotal role in the performance and longevity of various electronic and electrical devices. Recent innovations in this field have been significant. They address not only functional and performance aspects but also increasingly prioritize environmental sustainability. These advancements reflect an awareness of the challenges presented by modern manufacturing demands and the strict regulations applied to chemical products.
Eco-friendly Formulations
The push for eco-friendly formulations in electrical insulating varnish reflects broader changes across many industries. Manufacturers are now seeking alternatives that minimize environmental impact. This includes using materials that are less harmful to both the environment and human health.
Eco-friendly varnishes often utilize bio-based resins. These resins can significantly reduce carbon emissions during production. Furthermore, by avoiding toxic solvents, manufacturers contribute to a healthier workplace and ecosystem.
Benefits of eco-friendly formulations include:
- Reduced environmental footprint: These formulations decrease hazardous waste and emissions.
- Improved worker safety: Less exposure to harmful chemicals leads to a healthier workplace.
- Regulatory compliance: Many regions are tightening rules regarding volatile organic compounds (VOCs). Eco-friendly varnishes often meet or exceed these standards.
The transition to sustainable materials is not without challenges. Development time is extended, and testing new formulas against traditional ones can introduce uncertainties in performance. However, the long-term benefits ensure that companies adopting these methods stand out in a competitive market.
Nanotechnology in Varnish
Nanotechnology represents another exciting frontier in the development of electrical insulating varnish. By integrating nanoscale materials into varnishes, manufacturers enhance various properties that are critical for electrical insulation.
Nanoscale additives, such as silica or titanium dioxide, can improve the thermal stability and dielectric properties of varnish. This results in stronger protection against heat and electrical breakdown. The enhanced characteristics provide several advantages:
- Increased durability: Nanomaterials can add robustness to the varnish.
- Enhanced performance: Varnishes with nanotechnology can withstand stress better during operation, reducing the chances of failure.
- Lightweight applications: The addition of nanoparticles can lead to formulations that are effective yet lessened in weight, benefiting applications where weight is a concern.
Nonetheless, utilizing nanotechnology does carry certain risks and considerations. Development and production costs can increase, and regulators are still actively assessing the safety implications of nanomaterials. Ongoing research is crucial to address these concerns and ensure safe implementations.
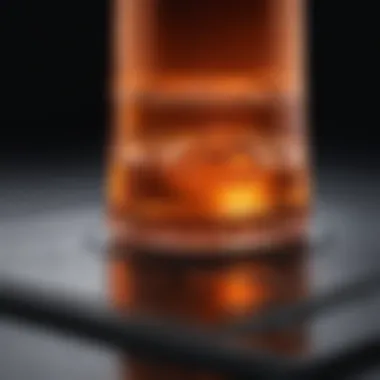
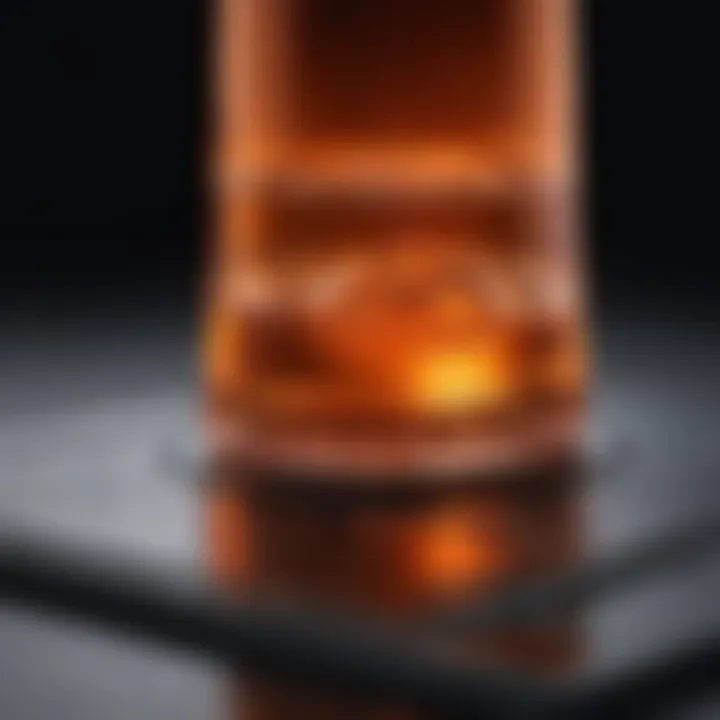
"Innovations in electrical insulating varnish not only improve technical performance but also aim for sustainable practices that resonate with current global priorities."
In summary, innovations in electrical insulating varnish encompass eco-friendly formulations and the implementation of nanotechnology. Both aspects highlight an industry aligned with environmental responsibilities and technological advancements. These innovations not only enhance the performance and durability of varnishes but also ensure compliance with evolving regulations, paving the way for a more sustainable future.
Standards and Regulations
The relevance of standards and regulations in the domain of electrical insulating varnish cannot be overstated. These guidelines ensure safety, performance, and compliance in various applications. Adhering to established standards is crucial as it enhances the reliability and effectiveness of insulating varnishes. Manufacturers must navigate a complex landscape of regulations that govern their products, influencing formulation, quality, and end-use applications.
Global Standards
Global standards for electrical insulating varnish provide a framework that governs their production and application. These standards are developed by international organizations like the International Electrotechnical Commission (IEC) and ASTM International. These entities set measurable benchmarks that varnishes should meet concerning dielectric properties, thermal stability, and chemical resistance.
Following these standards has several benefits:
- Uniformity: Global standards create consistency across products internationally. This ensures that users can expect similar performance regardless of where the varnish was produced.
- Safety: Adhering to safety standards reduces risks associated with electrical failures, which can lead to equipment damage or safety hazards.
- Quality Assurance: Compliance with standards often results in high-quality products. It encourages manufacturers to maintain strict quality control measures.
Non-compliance can lead to significant consequences. Companies may face product recalls, legal penalties, or deteriorated market reputation. Therefore, understanding these standards and integrating them into manufacturing procedures is pivotal for businesses in this sector.
Environmental Compliance
Environmental compliance is another essential aspect of standards and regulations affecting electrical insulating varnish. As global awareness about environmental issues grows, manufacturers are compelled to consider the ecological impacts of their products. Environmental regulations aim to minimize harm caused by chemicals used in varnishes.
This comprises:
- Volatile Organic Compounds (VOCs): Many varnishes release VOCs during application and curing. Regulations limit the amount of VOCs allowed in these products to safeguard air quality.
- Material Sourcing: Compliance often entails using sustainable materials that do not contribute adversely to environmental degradation.
- Recycling and Waste Management: The waste generated from varnish application demands careful management adhering to environmental regulations. Manufacturers must outline protocols for disposal or recycling, enhancing sustainability initiatives.
Challenges in the Application of Electrical Insulating Varnish
Electrical insulating varnish plays a pivotal role in extending the lifespan and improving the reliability of various electrical components. However, its application does come with challenges that need to be addressed to ensure optimal performance. Understanding these challenges is crucial for engineers and manufacturers in making informed decisions when selecting and applying these varnishes. In this section, we will explore two primary challenges: adhesion failure and the impact of temperature fluctuations. Both of these factors significantly influence the effectiveness of electrical insulating varnish in real-world applications.
Adhesion Failure
Adhesion failure is a critical obstacle when it comes to the application of electrical insulating varnish. It refers to the inability of the varnish to adhere properly to the substrate, which can lead to significant problems such as delamination, cracking, or peeling under operational conditions.
Several factors can contribute to adhesion failure:
- Surface Preparation: The surface to which the varnish will be applied must be adequately cleaned and prepared. Any contaminants, such as dust, grease, or moisture, can prevent proper bonding.
- Compatibility of Materials: The varnish must be compatible with the substrate material. Mismatched properties can result in poor adhesion, leading to failures.
- Application Techniques: Improper application methods, such as insufficient thickness or uneven layers, can affect adhesion strength.
To mitigate these issues, strict adherence to manufacturer's recommendations is vital. Regular testing of adhesion, employing surface treatments, and ensuring optimal application conditions can enhance the effectiveness of the varnish. By acknowledging and addressing potential adhesion challenges, manufacturers can improve the longevity and performance of their electrical devices.
Temperature Fluctuations
Temperature fluctuations are another significant challenge in the application of electrical insulating varnish. These variations can lead to changes in the varnish's properties, affecting its insulating capabilities and overall performance. Understanding how temperature influences varnish performance is essential for ensuring reliable applications.
Key considerations related to temperature fluctuations include:
- Thermal Expansion and Contraction: As temperature changes, the varnish and substrate materials expand and contract at different rates. This mismatch can cause stress and eventual failure within the insulating layer.
- Viscosity Changes: High temperatures can reduce the viscosity of the varnish, making it more difficult to control during application. Conversely, low temperatures can make it too thick, leading to poor coverage and adhesion.
- Cure Times: Temperature affects the curing process of the varnish. Higher temperatures typically accelerate curing, while lower temperatures can prolong it, leading to inconsistencies in the final product.
In practice, it is essential for manufacturers to consider the operational environment and select varnishes formulated to withstand specific temperature ranges. Employing temperature-stable insulating varnishes can help safeguard against these fluctuations, ultimately enhancing the reliability and durability of electrical devices.
In summary, addressing adhesion failure and temperature fluctuations is critical for the successful application of electrical insulating varnish. Understanding these challenges can assist manufacturers in making informed choices, ensuring better performance and longevity of electrical components.
Future Directions in Electrical Insulating Varnish Research
The exploration of future directions in electrical insulating varnish research holds significant implications for enhancing the effectiveness and longevity of electrical components. As technological advancements continue to evolve, the demand for high-performance insulating materials becomes ever more critical. This section outlines essential elements, benefits, and considerations that shape the future landscape of electrical insulating varnishes.
Smart Insulating Materials
Smart insulating materials represent the next quantum leap in varnish technology. These materials are designed to adapt to their environment, offering superior performance under various conditions. The primary characteristics that define smart insulating materials include:
- Self-healing capabilities: This feature allows the varnish to repair itself in case of minor damage, maintaining insulation integrity over extended periods.
- Responsive behavior to stimuli: Some materials can change properties in reaction to temperature, pressure, or electric fields, thus providing dynamic insulation that can enhance device reliability.
- Enhanced durability: Advances in resin technology aim to create insulating varnishes that withstand harsh environments, resistant to factors such as moisture and chemicals.
The benefits of integrating smart insulating materials into electrical devices include improved operational efficiency, reduced maintenance costs, and an extended lifespan of components. Furthermore, this evolution can lead to the development of more energy-efficient machines, contributing to sustainability in electrical applications.
Incorporating nanotechnology into smart insulating materials can further enhance the properties of electrical varnishes. Nano-sized fillers can improve mechanical strength and thermal conductivity, while maintaining dielectric performance. As research progresses, the collaboration among materials scientists and electrical engineers will be crucial in inventing novel solutions tailored to specific applications.
"The future of insulating varnish relies on innovative materials that not only protect but also enhance electrical systems' performance."
Ultimately, as researchers delve into smart insulating materials, it will be vital to consider not only the technical limitations but also the environmental impact of these advancements. Developing eco-friendly formulations that still meet performance standards will remain a central challenge. This pursuit of balance will shape the future of electrical insulating varnish, enabling the industry to realize materials that genuinely integrate with the broader goals of modern technology.