Understanding Extrusion: A Comprehensive Exploration
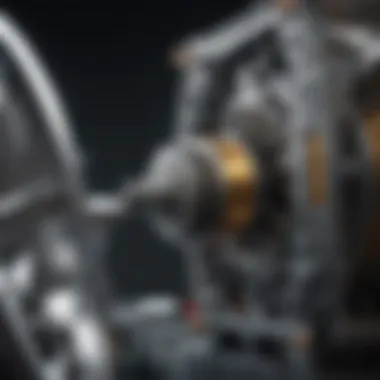
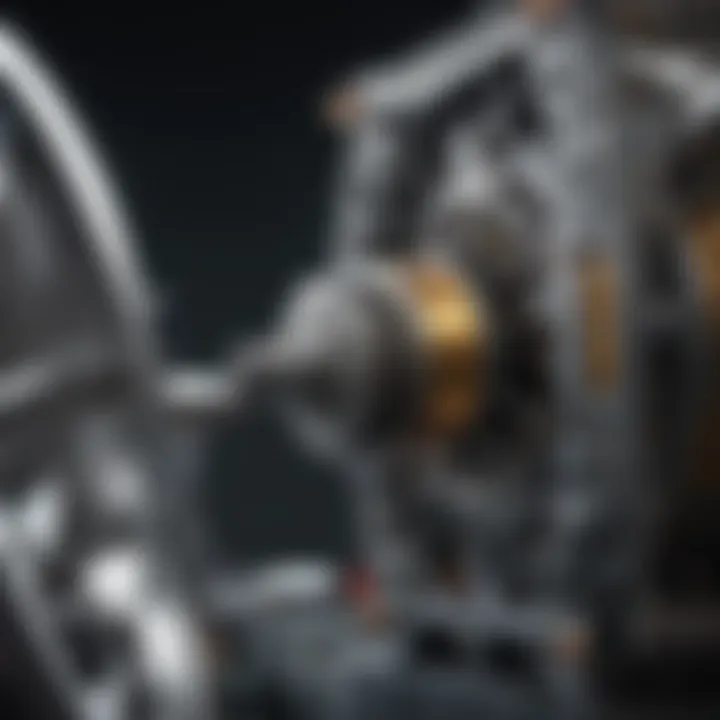
Intro
Extrusion is a significant industrial process with wide-ranging implications across a multitude of sectors, including food processing, manufacturing, and 3D printing. The essence of extrusion lies in its ability to transform raw materials into useful products through the application of heat and pressure. This article will meticulously dissect the detailed mechanics of the extrusion process, drawing attention to the theoretical underpinnings as well as practical applications.
The primary goal here is to delve into the various facets of extrusion, examining its principles, the different methods employed, and the criteria for selecting materials. Moreover, it will analyze how the characteristics of extruded products are influenced by the extrusion process itself. Such a comprehensive exploration provides a critical understanding suitable for students, researchers, educators, and professionals alike.
Extrusion spans numerous industries, impacting everything from the food that we consume to advanced engineering innovations in 3D printing. It serves not just as a method of fabrication but also as a catalyst for innovation, enabling the creation of new materials and products.
Thus, understanding extrusion is not merely an academic exercise; it is vital for advancing both technology and product development. The following sections will lay out the essential components and implications of this vital process.
Prologue to Extrusion
Extrusion is a fascinating and vital manufacturing method used in various industries. This process transforms raw materials into useful shapes and products, showcasing its significance in food processing, manufacturing, and more. Understanding extrusions not only highlights its operational methodologies but also delves into its economic and environmental implications.
One of the key elements of extrusion is its efficiency. The ability to produce complex profiles efficiently makes it an attractive choice for industries looking to optimize production costs. Additionally, the versatility of materials used in extrusion process helps cater to a wide range of applications, from plastic parts to food items.
Definition and Overview
Extrusion refers to a process in which material is pushed through a die to create a specific shape. This can be applied to various materials including plastics, metals, and food products. The procedure involves heating the material until it becomes pliable, at which point it is forced through the die to achieve the desired form. The end product can take on different shapes, such as sheets, tubes, or complex profiles, depending on the application's requirements.
The overall success of extrusion relies heavily on precise control of temperature, pressure, and material properties. Variations in any of these elements can lead to significant changes in the quality and characteristics of the final product.
Historical Context
The roots of extrusion can be traced back to the early 19th century. Initially, it was used primarily for metal forming. Innovations during the industrial revolution, however, paved the way for broader applications, particularly in plastic processing during the mid-20th century.
As plastic became widely adopted, the interest in extruding thermoplastics surged. This led to the development of specialized equipment tailored for different materials, enhancing the capability and efficiency of the extrusion process. From its humble beginnings to its current capabilities, extrusion has evolved significantly, making it a cornerstone of modern manufacturing.
"The evolution of extrusion technology reflects broader trends in manufacturing, emphasizing efficiency and the innovative use of materials."
In summary, understanding extrusion lays the foundation for exploring its principles, types, and applications. It demonstrates the process's importance across various industries, contributing to advancements and efficiencies that shape modern production techniques.
The Principles of Extrusion
Understanding the principles of extrusion is essential as it lays the groundwork for the effective application of this manufacturing process. By grasping the fundamental mechanics, flow dynamics, and the crucial role of temperature and pressure, professionals in the field can optimize their use of extrusion technologies. This section will delve into these core principles to provide clarity and insight into why they matter in the context of production and material performance.
Basic Mechanics of Extrusion
The basic mechanics of extrusion involve forcing a material through a shaped die. This process starts with material, often in pellet or powder form, being fed into a heated barrel. Inside the barrel, a screw or ram moves the material forward, applying both pressure and shear forces. These forces cause the material to melt or become pliable, allowing it to be shaped as it exits the die.
The screw design, the geometry of the die, and the properties of the material govern how effectively the extrusion occurs. Key parameters such as the speed of the screw, the temperature, and the type of material influence the final product's characteristics. Adjusting these factors is critical to achieving desired properties, including strength, flexibility, and finish quality of the extruded product.
Flow Dynamics in Extrusion
Flow dynamics play a pivotal role in the performance of the extrusion process. During extrusion, the material must flow seamlessly through the barrel and die. Understanding how materials behave under different conditions, including viscosity and shear rates, is essential for predicting how effectively they will extrude.
Factors affecting flow dynamics include:
- Material viscosity: Higher viscosity materials tend to resist flow, requiring more energy for extrusion.
- Temperature effects: Increased temperature usually lowers viscosity, allowing for easier flow.
- Pressure and velocity profiles: The relationship between pressure and flow speed can impact the uniformity and consistency of the final product.
By comprehending these dynamics, engineers can fine-tune processes to enhance output efficiency and quality.
Temperature and Pressure Considerations
Temperature and pressure are two fundamental considerations in the extrusion process. The melting point of the material significantly influences these factors. For thermoplastics, the temperature needs to be carefully controlled to ensure the material becomes malleable without degrading. For metals, both temperature and the pressure applied during extrusion can affect the material’s microstructure, thus influencing physical properties.
Maintaining the right balance between temperature and pressure is crucial. Too low of a temperature may result in poor flow, while excessive temperatures can lead to material degradation. Similarly, pressure must be optimized to ensure a homogeneous melt flow through the die.
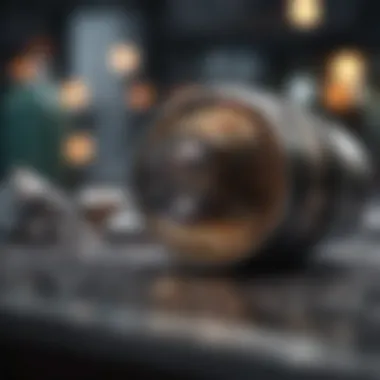
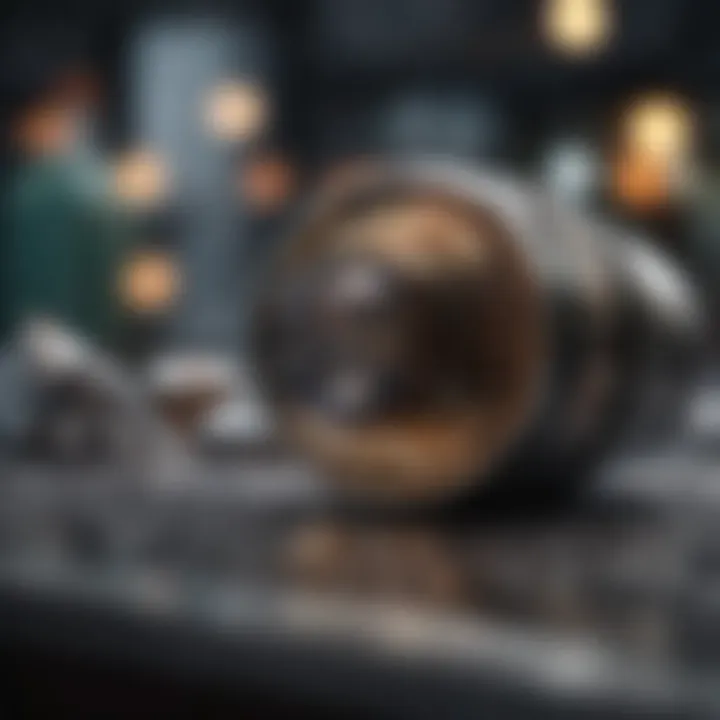
Proper control of temperature and pressure during extrusion is vital to achieving consistent quality and performance in molded products.
Types of Extrusion Processes
The types of extrusion processes play a pivotal role in understanding the extrusion method as a manufacturing technique. Each type serves specific purposes and offers unique benefits and considerations, crucial for selecting the right process for desired applications. It impacts not just the quality of the produced items, but also the efficiency and economics in production. Broadly speaking, the main categories are hot extrusion, cold extrusion, continuous extrusion, and batch extrusion.
Hot vs. Cold Extrusion
Hot extrusion involves heating the material above its recrystallization temperature, allowing it to become more malleable. This process is typically used for metals and certain plastics. The primary advantage of hot extrusion is the ability to shape materials that would otherwise be difficult to deform at room temperature. Additionally, it can lead to enhanced material properties due to grain refinement.
Applications: Hot extrusion is commonly used in the production of aluminum, copper, and brass components. The resulting products often exhibit higher strength and improved ductility.
On the other hand, cold extrusion is performed at or near room temperature. This method is primarily utilized for adding strength and improving surface finish. The advantages here include not requiring heating equipment, which reduces energy costs. Moreover, cold extrusion tends to minimize oxidation and contamination, making it suitable for high-precision applications.
Examples: Cold extrusion is often used for making fasteners, automotive parts, and other small components.
Continuous Extrusion
Continuous extrusion is a process where material is fed into the extruder continuously, allowing for uninterrupted flow. This approach is particularly effective in large-scale manufacturing. It increases throughput and consistency, making it ideal for producing long items like pipes and tubes. Continuous extrusion helps in maintaining uniformity in product dimensions. Manufacturers often prefer this method for its efficiency and reduced labor costs.
Key Points to Consider: While continuous extrusion has its advantages, it requires careful control of parameters like feed rate and temperature to avoid defects. The setup may also involve higher initial costs, but the long-term savings often justify the investment.
Batch Extrusion
In contrast, batch extrusion involves processing discrete amounts of material in cycles. This method is generally used for smaller production runs or testing new materials before moving to continuous processes. It allows for flexibility in material types and can accommodate variations in formulations or recipes.
Considerations: The batch process is less efficient for large volume production compared to continuous extrusion. However, its flexibility makes it suitable for specialty products or experimental initiatives. Companies often choose batch extrusion to explore product innovations or improve quality control without committing to significant capital investment.
In summary, understanding the types of extrusion processes is essential. Each method carries specific characteristics that can significantly influence the manufacturing process, product quality, and overall economic feasibility. Choosing the right approach requires a thoughtful assessment of material properties, production scale, and intended applications.
Materials Used in Extrusion
The choice of materials in the extrusion process is critical as it influences the efficiency, quality, and performance of the extruded products. Different materials have unique properties, which can enhance or limit the application of extrusion in various industries. Understanding these materials allows professionals to make informed decisions, ensuring that the correct material is selected for specific needs. The implications of material properties on the extrusion process are significant. Thus, we will explore three main categories of materials: thermoplastics, metals, and food extrusion materials.
Thermoplastics vs. Thermosetting Plastics
Thermoplastics are perhaps the most commonly used materials in extrusion. These materials become soft when heated and can be molded repeatedly without significant degradation. This characteristic allows for flexibility in manufacturing; products can be reshaped or recycled easily. Some popular thermoplastics include polyethylene, polypropylene, and polyvinyl chloride. Each offers distinct benefits such as durability, chemical resistance, and cost-effectiveness.
In contrast, thermosetting plastics undergo a chemical change when heated. Once set, they cannot be remolded or reshaped. This category includes materials such as epoxies and phenolics. The critical advantage of thermosetting plastics is their thermal stability and resistance to deformation under heat. However, their inability to be reshaped presents a limitation in some applications. It is important for professionals to weigh these properties when selecting the appropriate material for extrusion.
Metals in Extrusion Applications
In the realm of metal extrusion, common materials include aluminum, copper, and brass. These metals are often selected for their strength and lightweight properties. Metal extrusion allows the creation of complex cross-sections and is widely used in automotive and aerospace industries. The extrusion process helps to enhance the mechanical properties of metals, making products not only lighter but also more resistant to various forms of stress.
While metals can incur higher production costs compared to plastics, their strength and durability often justify this expense in many scenarios. Additionally, the extrusion of metals requires careful consideration of extruder design due to the high pressures involved. This attention to detail ensures the material flows as expected during the process, yielding high-quality extruded parts.
Food Extrusion Materials
Food extrusion is a specialized area that involves unique materials distinct from those used in industrial applications. Ingredients like starches, proteins, and moisture content are critical in determining the final product's texture and flavor. For instance, extrusion processing transforms raw grains into puffed snacks or breakfast cereals, providing a distinct texture that appeals to consumers.
The importance of selecting appropriate food materials cannot be overstated. The process parameters, such as temperature and moisture, especially impact the end product's quality. Innovations are continuously improving food extrusion techniques to enhance efficiency and product quality. The integration of natural ingredients and an emphasis on sustainability also shape the future of food extrusion.
Understanding these materials enables manufacturers to innovate and meet diverse consumer needs effectively.
In summary, the materials used in extrusion significantly impact the entire production process and the characteristics of the final product. By comprehensively understanding thermoplastics, metals, and food materials, professionals can improve product design and application in various sectors.
Applications of Extrusion
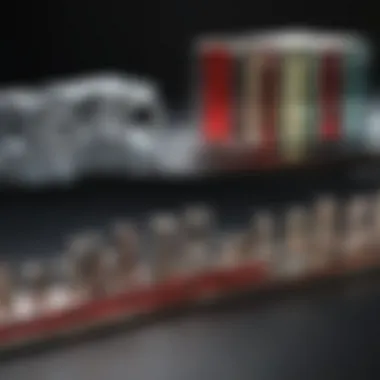
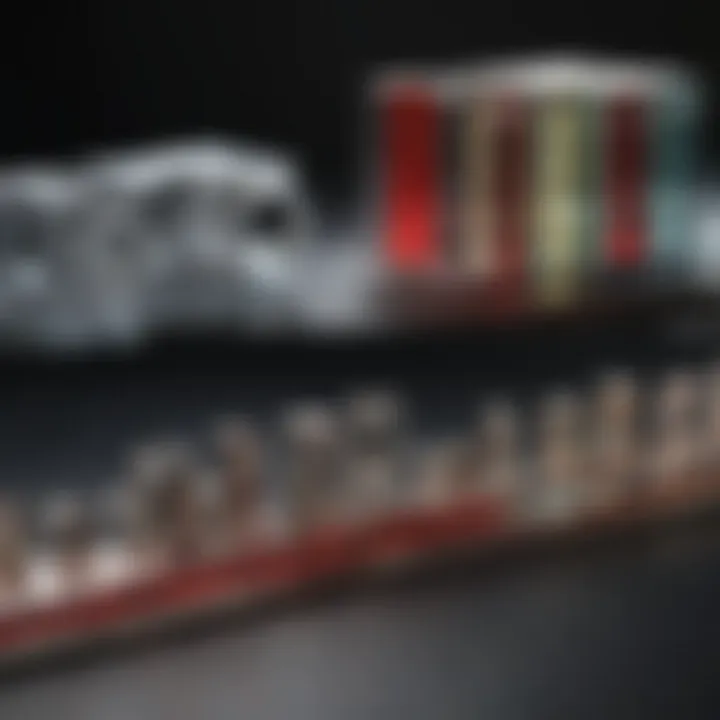
Extrusion serves as a versatile method in various industries, and its applications illustrate its wide parameter of usage. This section explores notable areas where extrusion stands as a critical process. Each application provides unique advantages and poses particular considerations.
Industrial Manufacturing
In the realm of industrial manufacturing, extrusion has established itself as a fundamental technique. This process enables the production of continuous profiles that can be tailored to specific needs. Industries such as automotive, aerospace, and electronics rely heavily on the extrusion of metals and plastics to create components like pipes, tubing, and structural shapes.
One key benefit of industrial extrusion is the enhanced material efficiency it promotes. By minimizing waste during production, companies can achieve substantial cost savings. Moreover, the method can accommodate a wide variety of materials, allowing for flexibility in design and application.
Considerations like precision and surface finish are paramount in industrial sectors. The extrusion process can be closely monitored to maintain quality standards, thus ensuring that parts meet strict specifications. The integration of digital technologies has further enhanced process accuracy.
Food Processing Techniques
Extrusion technology also plays a significant role in food processing. The technique helps in shaping and texturizing food products. Manufacturers use extrusion to create items such as breakfast cereals, snacks, and pasta. During this process, ingredients undergo heating and mixing before being pushed through a die to form the desired shapes.
The benefit of food extrusion lies in its ability to enhance nutritional properties. Extrusion allows for better digestibility and improvements in the texture of food products. Furthermore, the ability to incorporate various ingredients makes it possible to produce fortified and specialized food items.
While food extrusion is efficient, it also poses some challenges. Maintaining precise control over the temperature and moisture content is important to achieve optimal results. Variability in these factors can impact the final product quality significantly.
Construction Use Cases
In the construction industry, extrusion serves a vital role in creating materials such as window frames, siding, and roofing systems. The ability to produce long lengths of consistent profile allows for streamlined construction processes. This efficiency leads to faster project completion and reduces labor costs.
Extruded products in construction exhibit notable durability. Materials such as PVC and aluminum can be formed into robust structures that withstand environmental stresses. Moreover, the decorative capabilities of extrusion allow for customized appearances that enhance building aesthetics.
However, the construction sector must consider environmental regulations when utilizing extrusion. As awareness of sustainability grows, manufacturers are exploring ways to reduce their carbon footprint during production. Total life cycle assessments have become essential to evaluate the environmental impact of extruded products.
In summary, the applications of extrusion across various industries underscore its significance in enhancing product quality, efficiency, and cost-effectiveness. Each sector has specific requirements and challenges, pointing to the need for continued innovations in extrusion technology.
Challenges and Limitations of Extrusion
Extrusion processes play a crucial role in various industries. However, challenges and limitations are present and need consideration. These obstacles can affect efficiency, cost, and product quality. Understanding these issues is as important as knowing the advantages of extrusion. Addressing these limitations allows professionals to make informed decisions about the use of extrusion technology. This section highlights three primary areas of concern: material limitations, process inefficiencies, and environmental considerations.
Material Limitations
The choice of materials is critical in extrusion. Not all materials can be extruded effectively. Each material has unique properties that can affect the extrusion process.
- Thermal Sensitivity: Some materials may degrade under high temperatures. This degradation can lead to a loss of material properties, resulting in inferior products.
- Viscosity Variations: Different materials possess varying viscosity levels. If the viscosity is too high, it can hinder the flow through the die. Conversely, too low viscosity can lead to loss of shape and integrity.
- Composite Materials: The use of composite materials can be challenging. They may require specific conditions for extrusion and may not blend well under typical extrusion conditions.
Process Inefficiencies
Inefficiencies in extrusion can significantly affect productivity. Several factors contribute to these inefficiencies, and recognizing them is essential for optimization.
- Cycle Time: Longer cycle times can reduce throughput. Efficient design and scheduling of the extrusion process are necessary to improve performance.
- Equipment Reliability: Frequent machine downtimes can disrupt production. Regular maintenance is vital to minimize unexpected failures.
- Operator Skills: The skills of machine operators impact the quality and efficiency of the extrusion process. Proper training and experience can lead to better handling of machines and troubleshooting of issues.
Overall, addressing these inefficiencies can lead to enhanced productivity and lower operational costs in extrusion processes.
Environmental Considerations
Environmental sustainability is a growing concern in all industries. Extrusion is no exception and presents some environmental challenges.
- Material Waste: Extrusion processes can produce significant material waste. The development of methods to recycle scraps can lessen environmental impact.
- Energy Consumption: High energy usage is often required for extrusion. This can lead to increased carbon footprints. Innovations in machinery can help reduce energy consumption.
- Emissions: The extrusion process can generate air and noise pollution. Implementing better emission control systems is necessary to mitigate these concerns.
To conclude, environmental considerations demand attention within the extrusion industry to ensure sustainable practices are in place.
Overall, understanding these challenges and limitations is crucial for anyone looking to utilize extrusion processes effectively. By acknowledging the nuances of materials, inefficiencies, and environmental impacts, one can navigate the complexities of extrusion with a more informed perspective.
Innovations in Extrusion Technology
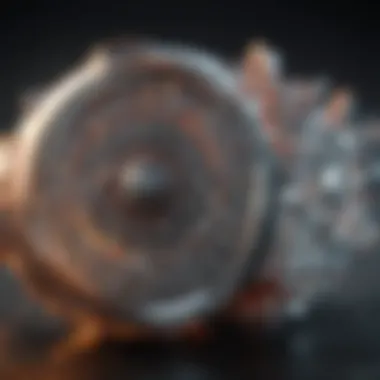
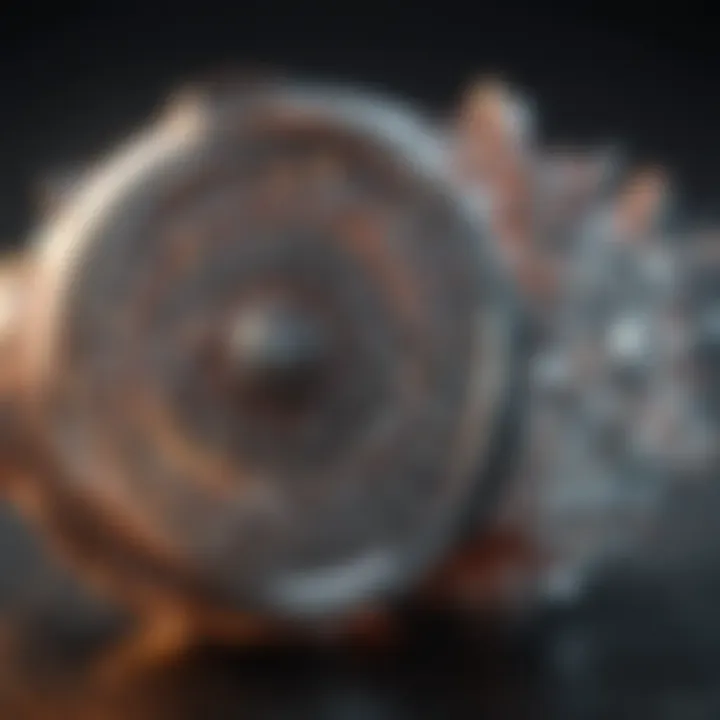
The field of extrusion technology is experiencing rapid evolution. Innovations play a significant role in enhancing productivity, efficiency, and sustainability across various applications. As industries demand higher performance and adaptability, the importance of staying updated with the latest in extrusion technology cannot be overstated. This section outlines the key advancements occurring in the realm of extrusion equipment, process automation, and sustainability efforts.
Advancements in Equipment
Recent years have seen notable advancements in the machinery used for extrusion. Modern extruders feature enhanced designs that allow for better flow dynamics and temperature regulation. Manufacturers are focused on increasing the reliability and performance of their equipment. For instance, twin-screw extruders are now widely employed for complex material compositions. Their design enables superior mixing and processing capabilities, which is crucial for applications demanding high precision.
Moreover, the integration of smart technologies in equipment design cannot be ignored. Specific sensors and monitoring systems are now common, allowing real-time tracking of the extrusion parameters. This leads to better quality control and the ability to make adjustments on the fly. Additionally, modular machinery designs facilitate quick changes in production setups, enabling firms to respond promptly to market demands.
Process Automation
Automation in extrusion processes is another vital area of innovation. The shift towards smart manufacturing includes the adaptation of automated systems to enhance efficiency. These systems minimize human error and optimize throughput by maintaining consistent quality across production runs.
With the Internet of Things (IoT) gaining traction, extrusion processes can now be closely monitored remotely. This allows for predictive maintenance, which mitigates downtime and enhances productivity. Operators can receive alerts when a system is likely to fail, enabling timely interventions. Furthermore, automated feeding systems and inline quality monitoring ensure that materials and finished products meet stringent quality specifications without requiring continuous manual oversight.
Sustainability Efforts
Sustainability is increasingly becoming a focus within the extrusion sector. Industries are urged to adopt practices that reduce waste and energy consumption. Innovations here include the development and utilization of biodegradable materials in extrusion processes. Companies are exploring bioplastics derived from renewable resources, which is a step forward in reducing environmental impact.
Moreover, advancements in recycling technologies are noteworthy. Extrusion processes now incorporate recycled materials more efficiently, thus decreasing dependence on virgin resources. This not only benefits the environment but can also lead to significant cost savings for manufacturers. Encouragingly, industry stakeholders are collaborating to share research and drive forward sustainable practices consistently.
"The advancements in extrusion technology signify a fundamental shift towards efficiency and sustainability, ensuring that industries remain competitive while being mindful of our planet."
Future Trends in Extrusion
The extrusion industry is continuously evolving. Innovations and advancements are shaping its future. Understanding these trends is essential for professionals, researchers, and educators involved in this field. The integration of new technologies, materials, and processes has significant implications, enhancing the capabilities of extrusion to meet modern demands.
3D Printing Integration
3D printing technology has revolutionized manufacturing. It is increasingly integrated with extrusion processes. This integration allows for complex shapes and structures that traditional methods cannot achieve. By using extrusion in 3D printing, manufacturers can produce items swiftly with precise material control. The combination reduces waste and optimizes material usage, which is vital in environmental considerations.
The synergy between these technologies enables customizability in designs, catering to specific needs of consumers or industries. Moreover, large-scale production becomes more feasible. Companies can employ bio-based or recycled materials in 3D printing, aligning with sustainability goals.
Biomaterials in Extrusion
Biomaterials are gaining traction in the extrusion landscape. These materials offer environmental benefits and health safety. The focus has shifted toward sustainable practices, which are crucial for industries like packaging and medicine. Applying biomaterials can significantly decrease plastic waste, a critical concern today.
Extrusion technology is adaptable to various biomaterials, including starches, cellulose, and plant-based polymers. Developing these materials requires extensive research. Understanding their properties and behavior during the extrusion process is essential for optimizing their performance. Increased adoption can lead to innovations that support eco-friendly practices while maintaining product integrity.
Global Market Outlook
The future of the extrusion market looks promising. Driven by globalization and technological advancements, the demand for extruded products is expected to rise. Industries such as automotive, construction, and packaging will likely propel this growth.
According to recent reports, the global extrusion market is projected to expand substantially. Companies should be aware of regional trends and consumer preferences. Adapting to emerging markets will be critical for sustaining competitive advantages.
The evolution of extrusion technology reflects broader shifts in global manufacturing trends, indicating new opportunities for companies engaged in this field.
Ending
The conclusion of this article brings a necessary closure to the intricate world of extrusion. In a landscape where manufacturing processes continuously evolve, understanding extrusion comprehensively becomes crucial. This section emphasizes how vital extrusion is in the broader context of production across several industries such as food processing, manufacturing, and even in emerging fields like 3D printing.
Summary of Key Points
To encapsulate the main themes discussed:
- Definition and Overview: Extrusion is a versatile manufacturing process crucial for shaping materials through generating force and heat. Its applications range across sectors, from food production to industrial manufacturing.
- Principles of Extrusion: The basics of mechanics are essential for appreciating how material flows under various conditions. Temperature and pressure influence the final product’s properties significantly.
- Types of Extrusion Processes: Understanding hot and cold extrusion, as well as continuous and batch methods, reveals the diversity of approaches that can be tailored to specific materials and end products.
- Materials Used: The choice between thermoplastics, thermosetting plastics, and metals affects both the process and performance of the extruded products, each having its unique characteristics.
- Applications: The broad range of applications highlights how integration of extrusion shapes the functions of everyday products. From manufacturing components to unique food processing techniques, the technology is universally applicable.
- Challenges and Innovations: Issues like material limitations and process inefficiencies challenge industry players, but innovations in equipment and methods continuously reshape the landscape, making extrusion more efficient and sustainable.
- Future Trends: Looking forward, areas like 3D printing and the use of biomaterials indicate how extrusion will continue to adapt to meet future demands in sustainability and functionality.
Call for Continued Research
The landscape of extrusion is ever-changing, and ongoing research is essential. As industries strive for enhanced efficiency and sustainability, the need for novel materials and methods is pressing. Continued investigation could lead to breakthroughs in:
- Material Science: Exploring new biomaterials provides opportunities to create more sustainable and eco-friendly products.
- Process Optimization: Research into automation and smart manufacturing techniques can improve productivity and reduce waste.
- Global Trends: The increasing demand for specialized extrusion techniques motivates further scholarly examination and practical experimentation.
In summary, the diverse applications and ongoing innovations present a fertile ground for academic and practical exploration, making continued research not just beneficial but necessary for the evolution of extrusion technology.