Understanding the Friction Coefficient: An Overview
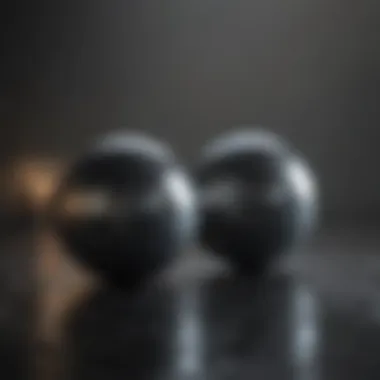
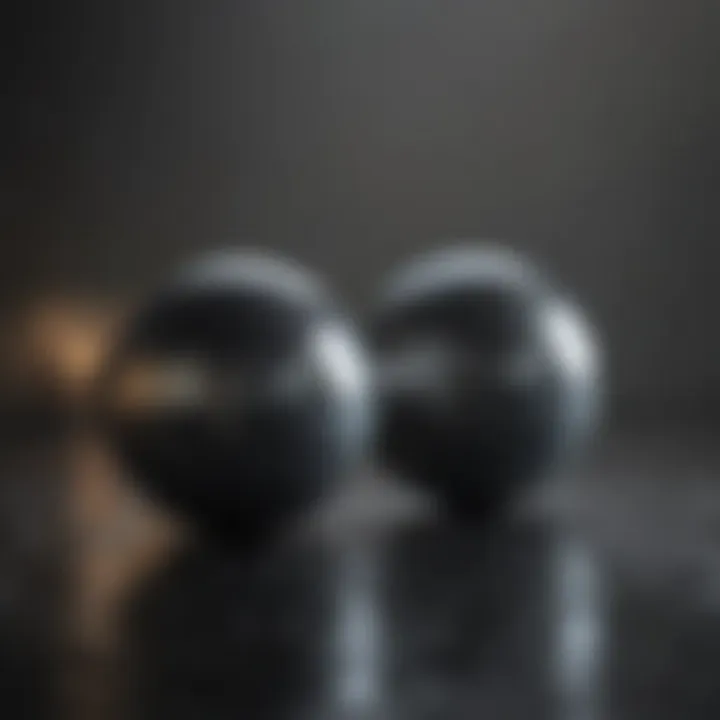
Intro
The study of the friction coefficient holds significant relevance in the fields of physics, engineering, and materials science. It describes the resistance encountered when two surfaces move against each other. A proper understanding of this concept is crucial for optimizing designs in various applications, from automotive components to industrial machinery.
The friction coefficient varies widely among different materials and conditions. This variability has profound implications for performance, safety, and efficiency. Measuring and analyzing the friction coefficient allows engineers and researchers to improve or reduce friction where necessary, enhancing functionality and longevity of products.
In this article, we will analyze the fundamental principles of the friction coefficient, its variations across differing materials, and the importance of this knowledge in practical fields like engineering. Furthermore, we will detail methods used to measure these coefficients effectively and explore recent trends in research aimed at manipulating friction for improved material performance.
Research Overview
Summary of key findings
Friction coefficients are influenced by various factors, such as surface roughness, material properties, and environmental conditions. Studies reveal a simple pattern: rough surfaces generally yield higher friction coefficients, while smoother surfaces tend to exhibit lower values. The coefficient can also change based on the state of contact, either static or kinetic.
Recent research has identified that the friction coefficient is not a constant value, but a function of load and speed. This non-linear behavior is particularly relevant in applications requiring precise control over motion, such as robotics and advanced machinery.
Importance of the research in its respective field
Understanding the friction coefficient is vital for multiple reasons. First, it allows for safer design of systems that rely on mechanical interactions. Second, it aids in energy efficiency, as optimizing friction reduces unnecessary energy loss, prolonging component life. Moreover, insights gleaned from friction studies contribute to innovations in material sciences, leading to the development of advanced composites with tailored friction properties. This adaptation is beneficial especially in the automotive and aerospace industries where performance is paramount.
Methodology
Description of the experimental or analytical methods used
Various methods exist to measure and analyze the friction coefficient. Commonly, pin-on-disk tests are utilized where a pin being tested is pressed against a rotating disk. The frictional force is measured, allowing for calculation of the coefficient under defined conditions. This technique provides valuable insights into how different materials interact under load.
Other methods include tribological tests in controlled environments to simulate real-world conditions. These detailed experiments help in assessing how factors like temperature and humidity impact friction performance.
Sampling criteria and data collection techniques
Selecting materials for study is crucial. Researchers often opt for a range of common materials like steel, aluminum, and polymers, ensuring that the data collected spans various applications and uses. The data collection methods must also be rigorous, employing statistical tools to ensure that results are replicable and valid.
"Studying the friction coefficient leads to the development of materials that can either enhance or reduce friction, impacting the efficiency of machines significantly."
Collectively, these methodologies provide a robust framework for understanding friction. Researchers must also stay updated with emerging technologies, utilizing advanced sensors and data analytics for real-time friction monitoring.
Prologue to Friction Coefficient
Understanding the friction coefficient is crucial in various fields, including engineering, physics, and materials science. It is a fundamental concept that explains how surfaces interact under varying conditions. The implications of studying the friction coefficient are significant. It affects everything from vehicle braking systems to the manufacturing of machines. Knowing the behavior of friction helps in designing safer and more efficient systems.
One of the key benefits of comprehending the friction coefficient is its practical application. Engineers can optimize designs to enhance performance. For instance, in automotive industries, understanding friction leads to better tire designs that improve safety and fuel efficiency. In robotics, friction analysis contributes to more effective motion and control.
There are important considerations when studying the friction coefficient. Among them are the types of friction, which include static, kinetic, and rolling friction. Each type behaves differently based on specific conditions. Understanding these differences allows researchers and professionals to address challenges related to friction in innovative ways.
Moreover, this section will delve into the definition of the friction coefficient, and its historical context, shedding light on how the concept has evolved over time. The friction coefficient functions as a bridge connecting theoretical principles and real-world applications.
"The friction coefficient is not just a number; it represents the forces that govern movement and stability in countless systems."
It is valuable for all stakeholders to grasp this topic. Therefore, a robust understanding of the friction coefficient is integral to advancements across multiple disciplines.
Types of Friction
Understanding the different types of friction is crucial for both theoretical insights and practical applications in various fields. Each type of friction plays a significant role in how objects interact, whether in machinery, transportation, or even biological systems. Knowing the nature of static, kinetic, and rolling friction allows engineers and researchers to design more efficient systems and solve practical problems effectively.
Static Friction
Static friction refers to the force that resists the initiation of sliding motion between two surfaces in contact. It is essential for everyday activities, such as walking or driving, where starting movement is a critical factor. The static friction force acts until a threshold is reached. This threshold is defined as the maximum static friction force, represented by the formula:
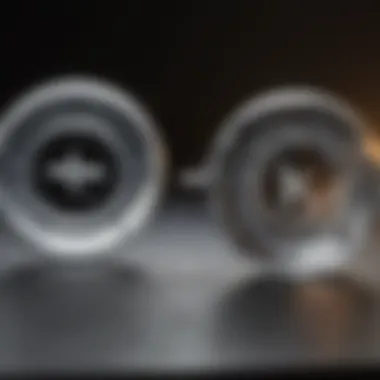
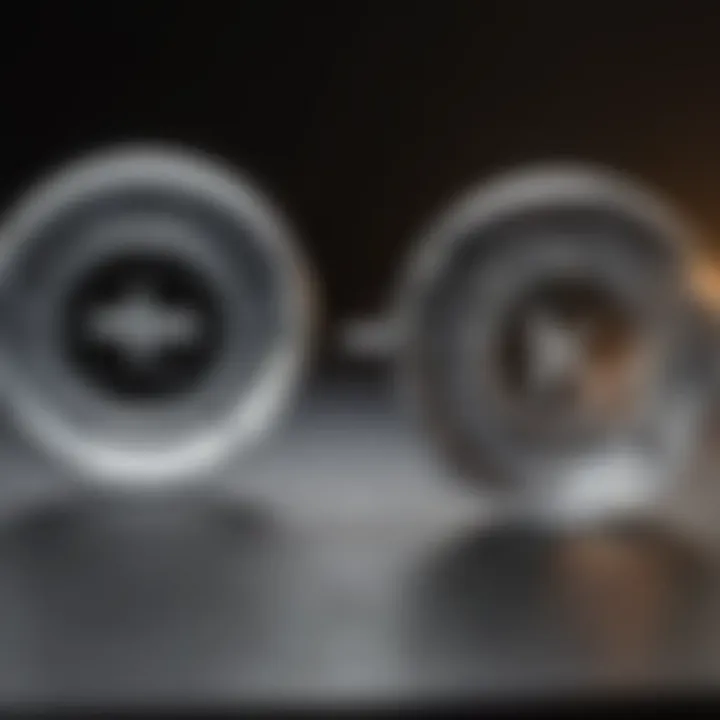
F_s ≤ μ_s * N
Where F_s is the static friction force, μ_s is the coefficient of static friction, and N is the normal force.
The significance of static friction cannot be overstated. It ensures objects remain in place when desired. For instance, a parked vehicle relies entirely on static friction to prevent rolling down a slope. If a car were to move, it would require a force greater than static friction to initiate that motion, emphasizing the friction's role in stability.
Kinetic Friction
Kinetic friction, also known as dynamic friction, comes into play once sliding motion begins between two surfaces. Different from static friction, kinetic friction always has a lower value compared to its static counterpart. It can be defined by the equation:
F_k = μ_k * N
Where F_k is the kinetic friction force, μ_k is the coefficient of kinetic friction, and N is the normal force.
When objects slide against each other, kinetic friction is significant in determining the energy lost due to frictional forces. This type of friction plays a role in many mechanical systems, such as conveyor belts or sliding doors. The design of these systems must take kinetic friction into account to optimize their efficiency. Moreover, understanding kinetic friction helps to enhance performance in sports; for instance, athletes need to manage their sliding movements efficiently.
Rolling Friction
Rolling friction differs distinctly from static and kinetic friction. It occurs when an object rolls over a surface. Rolling friction is generally much less than static or kinetic friction. This lower value is significant for movement efficiency, such as in vehicles and machinery. The formula for rolling friction can be expressed as:
F_r = c * N
Where F_r is the rolling friction force and c is the coefficient of rolling resistance.
The application of rolling friction can be observed in many contexts. For example, the use of wheels reduces the energy needed to move an object, providing a clear advantage in transportation. Additionally, it impacts various engineering designs, including those of roller bearings in machinery, where minimizing friction is crucial for longevity and performance.
In summary, the understanding of these three types of friction—static, kinetic, and rolling—is essential for practical applications in engineering, physics, and beyond. Analyzing the implications of each type allows for improved designs and innovations across diverse fields.
Factors Affecting Friction Coefficient
Understanding the factors affecting the friction coefficient is essential for both theoretical and applied sciences. These factors can influence how materials interact with each other, which plays a critical role in various fields, from engineering design to the study of natural phenomena. The friction coefficient itself is not a constant value; it can vary significantly based on different conditions and characteristics. Therefore, knowing what affects this coefficient helps in accurately predicting frictional behavior in real-world applications.
Material Properties
Surface Roughness
Surface roughness is a critical aspect of material properties that significantly influences the friction coefficient. The roughness describes the texture of a surface—the more irregularities present, the higher the potential for friction. This characteristic can enhance grip and adhesion between surfaces, which may be desirable in applications such as brake systems. However, excessive roughness can lead to increased wear and energy loss due to higher friction. An optimal balance often needs to be struck for specific applications.
Hardness
Hardness is another important material property impacting the friction coefficient. A harder material typically resists deformation better than softer counterparts. This resistance can lead to lower wear rates and longer lifespan in certain applications. For example, materials like tungsten carbide are used in cutting tools due to their high hardness, resulting in less friction when cutting metals. Yet, if the surfaces are too hard, they might trigger brittle failure under certain loads, which requires careful consideration.
Material Composition
The material composition also plays a vital role in determining the friction coefficient. Different materials exhibit distinct behaviors based on their molecular structure and composition. For instance, rubber has a high friction coefficient when in contact with metal, making it valuable in tire manufacturing. Conversely, materials like Teflon serve as effective lubricants due to their low friction properties. Understanding the specific characteristics and applications of materials aids in making informed choices about material selection in engineering and design.
Environmental Conditions
Temperature Effects
Temperature can considerably influence the friction coefficient by altering the physical properties of materials. As temperature increases, materials can expand, changing their microstructure, which may lead to changes in surface roughness or hardness. In settings like automotive braking systems, temperature variations can affect performance and safety. Therefore, understanding how temperature affects the friction coefficient is vital for system design and reliability.
Humidity and Moisture
Humidity and moisture are environmental factors that can modify the friction coefficient in various contexts. For example, wet surfaces tend to reduce friction because water acts as a lubricant, lowering the effectiveness of contact between materials. Conversely, in environments with low humidity, certain surfaces may become prone to increased friction due to dry contact. Recognizing these conditions can guide engineers in designing systems that function reliably across varying environmental scenarios.
Presence of Lubricants
Lubricants are commonly used to reduce friction between sliding surfaces. The presence of lubricants can significantly lower the friction coefficient, which enhances the efficiency of mechanical systems. For instance, oil in engine components reduces heat and wear. However, choosing the right type of lubricant is crucial; some may degrade quickly, leading to increased friction over time. Therefore, understanding lubricants' properties and their impact on friction is vital for achieving optimal performance.
Contact Pressure
Contact pressure refers to the load that one surface exerts on another. This factor is critical in understanding how much friction is generated when surfaces come into contact. Higher contact pressure can lead to increased friction due to a greater area of interaction, potentially causing wear. However, too much pressure might result in material deformation or failure, which needs to be accounted for in system design. Balancing contact pressure is key for optimizing frictional performance while considering material durability and application requirements.
Mathematical Representation of Friction Coefficient
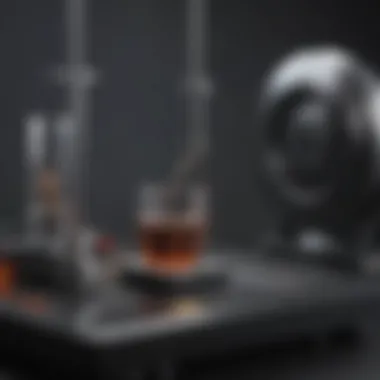
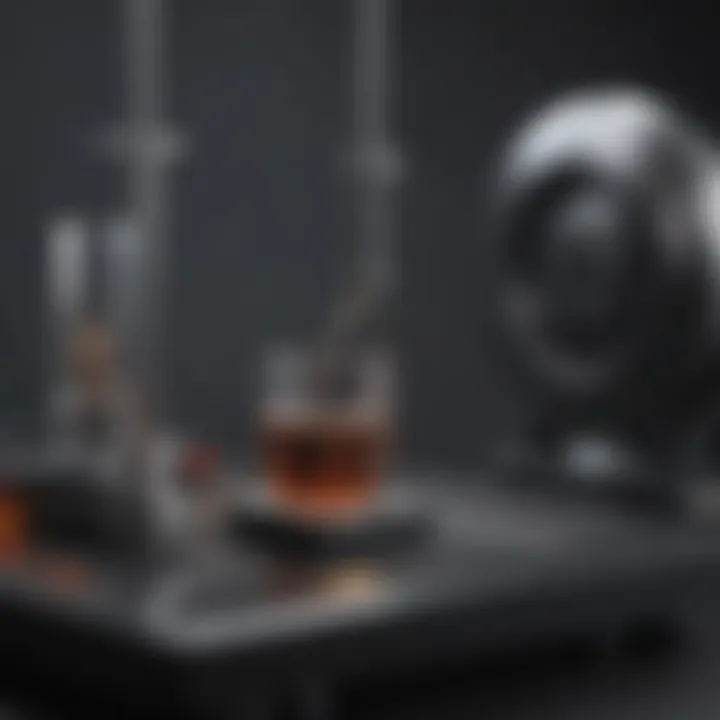
The mathematical representation of the friction coefficient is critical in understanding how friction behaves under various conditions. It provides a framework for analyzing the interactions between surfaces in contact. This section discusses the basic equation and the derivation of the coefficient of friction formula. A clear grasp of these concepts allows engineers, researchers, and students to apply this knowledge practically in their respective fields.
Basic Equation
The primary equation used to express the friction force is:
[ F_f = \mu \cdot F_n ]\
In this equation, ( F_f ) represents the frictional force, ( \mu ) is the coefficient of friction, and ( F_n ) is the normal force acting between the two surfaces. This formula highlights how the frictional force is directly proportional to the normal force. As the normal force increases, the frictional force also increases, assuming the materials and their conditions remain constant.
Mathematically, the coefficient of friction can be categorized into two types: static and kinetic. Static friction occurs when an object is at rest, while kinetic friction applies when the object is in motion. The value of ( \mu ) varies based on material pairs. For instance, rubber on concrete has a value around 0.6 to 0.9, while ice on steel may be significantly lower, around 0.1.
Coefficient of Friction Formula Derivation
Deriving the coefficient of friction formula involves understanding several fundamental principles of physics. The main concepts include:
- Skipping Motion: Initially, when attempting to move an object, the applied force may not overcome static friction, resulting in no motion. The maximum static friction force is the product of the coefficient of static friction and the normal force.
- Transitional Motion: Once the object starts moving, the kinetic friction applies. The frictional force is calculated similarly, but with the coefficient of kinetic friction.
The derivation process can be outlined as follows:
- Start with the definitions: Understand that frictional force is related to the normal force through the coefficient of friction.
- Apply Newton's Second Law: This law states that force equals mass times acceleration. In a friction scenario, when the net force equals zero during static conditions, the applied force equals the maximum static friction force.
- Express the forces: Through equilibrium conditions, we recognize that:
- Isolate the coefficient: Rearranging gives us our coefficient of friction, enabling us to connect theoretical predictions and experimental measurements.
Understanding the mathematical relationships allows for clearer insights into friction and application in technologies such as brakes and tires.
Measurement Techniques for Friction Coefficient
Understanding how to measure the friction coefficient is critical for both theoretical and practical applications. Accurate measurement techniques provide essential data for engineers, researchers, and practitioners who need to understand material behavior in various environments. The selection of the right measurement method can greatly influence the findings, so it is necessary to consider various factors such as the precise requirements of the application, the materials involved, and environmental conditions.
Direct Measurement Methods
Direct measurement methods involve physical tests to determine the friction coefficient. These methods typically measure the force required to initiate or maintain movement between two surfaces.
- Inclined Plane Method: This method relies on placing a material at a specific incline until it starts sliding. By measuring the angle at which sliding occurs, the static friction coefficient can be calculated using trigonometric principles.
- Tribometer Tests: Tribometers are devices designed to enact controlled sliding between different materials. They can provide both static and kinetic friction measurements under varied conditions. This flexibility allows for examining how changes in speed, pressure, and surface modifications affect friction.
- Pin-on-Disk Technique: In this approach, a pin is pressed against a rotating disk. The force required to keep the pin in contact with the disk is measured, providing valuable data on the friction coefficient during relative motion, particularly useful for studying lubricants and surface treatments.
These direct methods are advantageous due to their straightforward application and ability to yield real-time results. However, they can be affected by environmental factors like temperature and humidity, which may influence the friction coefficient significantly.
Indirect Measurement Methods
Indirect measurement techniques provide a means to infer the friction coefficient without directly measuring the forces involved. These methods tend to rely on calculations or deductions based on related measurements.
- Mohr-Coulomb Theory: This theoretical approach posits that friction can be understood in terms of stress and cohesion. By measuring the forces acting on a known surface, engineers can derive the friction coefficient indirectly by analyzing the stress conditions present.
- Mechanical Testing: Techniques such as tensile or compression testing can yield values that, when analyzed, allow for the assessment of friction behavior. The relationships between stress and strain can be correlated with friction measurements, allowing for a comprehensive understanding of material interactions.
- Friction Simulation Models: Advanced computational methods can simulate how materials will interact. These models can predict friction behavior under various conditions, which is particularly valuable in the early stages of design or material selection. Using algorithms, researchers can explore a wide array of scenarios without physical testing.
Each of these indirect methods has its benefits, particularly in their ability to integrate with broader research initiatives or when physical testing is not feasible. However, the reliance on approximations can introduce uncertainties that need careful consideration in application.
Overall, meticulous measurement of the friction coefficient via both direct and indirect methods is vital for advancing materials science and engineering. Understanding the techniques available allows for better decision-making in design and application, leading to improved safety and efficiency in engineering solutions.
Applications of Friction Coefficient
The friction coefficient plays a crucial role in many applications across various fields, impacting performance, safety, and efficiency. Understanding its applications allows engineers, researchers, and practitioners to design systems that optimize friction conditions for specific uses. The importance of this topic lies in its practical relevance in day-to-day situations and advanced technology.
Engineering and Design
Brake Systems
In brake systems, the friction coefficient is essential for transforming kinetic energy into heat. The coefficient determines how effectively the brakes can halt various vehicles. A higher friction coefficient means better stopping ability, which is critical for vehicle safety. Materials like carbon composite are often used due to their ability to withstand high temperatures and maintain reliable friction levels. One significant characteristic is that these materials can provide consistent performance under varying conditions, making them a popular choice for sports cars and heavy vehicles. A notable disadvantage is that higher friction can lead to quicker wear, necessitating frequent replacements.
Tire Design
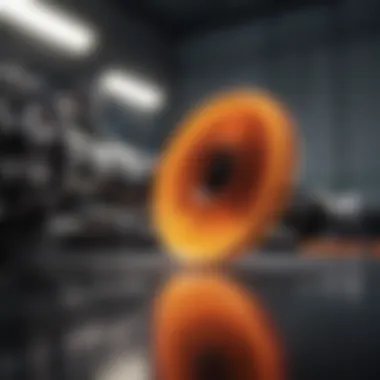
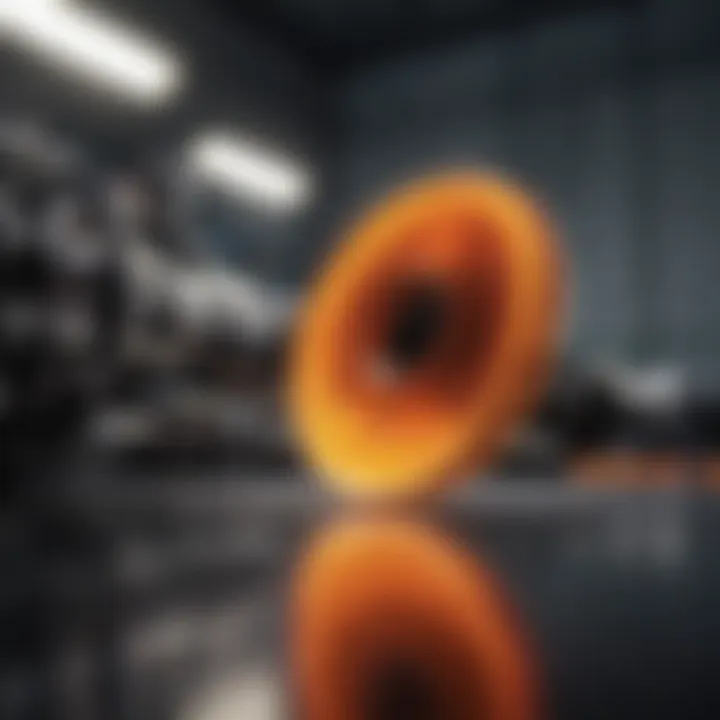
Tire design heavily relies on the friction coefficient to enhance vehicle handling. Tires need to grip the road adequately, and that requires careful consideration of the friction characteristics. Rubber compounds and tread patterns are meticulously engineered to provide the right balance between grip and wear resistance. One of the key characteristics of modern tires is the ability to adapt to different weather conditions, such as wet or icy surfaces. Nonetheless, a drawback is the trade-off between grip and rolling resistance, which can affect fuel efficiency.
Material Selection
Material selection is a fundamental part of engineering, especially when friction is involved. Choosing appropriate materials can significantly improve the performance of various systems. Metal-on-metal contact, for example, involves a specific coefficient of friction, which can influence the overall wear of machinery. One important characteristic of selected materials is their ability to maintain their properties under load and temperature. A beneficial aspect is the enhanced efficiency gained from reduced friction in moving parts. However, the challenge often lies in balancing cost with performance, as advanced materials may incur higher production costs.
Robotics and Automation
In robotics and automation, the friction coefficient is vital for the functionality of robotic joints and mechanisms. Precision in movement relies on understanding how different materials interact under load. For instance, low-friction coatings can enhance the performance of robotic arms, leading to increased efficiency and longer service life. This understanding is not only about performance but also about energy consumption, as reduced friction can lower the energy needed for operation.
Biomimicry
Biomimicry adopts natural designs to solve human challenges, often looking at friction to inspire innovations. Nature has developed ways to minimize drag and maximize grip, observed in the design of gecko feet or fish scales. These natural systems provide insights into how materials can be engineered to achieve desired friction properties. The potential for this knowledge to lead to more efficient systems or reduce wear in industrial applications is significant, opening pathways for future research in material science.
Challenges in Friction Research
Researching the friction coefficient presents several complexities that must be thoroughly understood. These challenges hinder the predictability and manipulation of friction in practical applications. To grasp the significance of this, one must consider how friction affects numerous areas in engineering, robotics, and material science. Addressing these challenges can lead to improvements in product design and operational efficiency.
Complex Interactions
Friction is not merely a product of surface roughness or material selection. It represents a complex interaction of mechanical properties, environmental conditions, and geometric variables. For instance, the behavior of a tire on wet asphalt differs from its performance on a dry surface. This variation stems from the presence of water influencing the contact area and material response. Researchers must account for these interactions when modeling friction behavior.
Another example of this complexity arises in multi-material interfaces. When two different materials interact, the friction behavior can often be unpredictable. This unpredictability emerges from factors such as material hardness, wear characteristics, and surface contamination. Hence, controlling these interactions requires comprehensive experimentation and analytical skills.
Variability in Measurements
Measuring the friction coefficient is fraught with variability, leading to inconsistent results. Such variability can stem from minor changes in environmental factors like temperature and humidity. For example, a slight increase in temperature can reduce the viscosity of lubricants, altering friction even in controlled settings.
Moreover, the techniques used to measure friction add another layer of complexity. Different methods yield different results. For example, using a tribometer may produce varying coefficients due to differences in loading conditions or sliding speed.
The discrepancies in measurement call for standardized procedures, which are often lacking across disciplines. Hence, establishing accepted protocols can not only enhance the reliability of friction measurements but also facilitate comparative studies across different research domains.
"Understanding these challenges allows for a more robust application of friction theories in both practical and theoretical frameworks."
Future of Friction Research
The future of friction research promises to unveil innovative insights that can significantly impact various fields. With rapid advancements in material science and engineering, understanding friction at a quantum level can lead to new applications. Researchers are focused on enhancing or minimizing friction to improve efficiency, reduce wear, and optimize performance in industries ranging from automotive to robotics.
Emerging trends such as nanotechnology and smart materials stand at the forefront of this exploration. These areas not only provide greater control over friction properties but also present unique opportunities for developing smarter systems that respond to their environment. In this light, friction research is set to evolve, potentially leading to revolutionary applications that can change standards in manufacturing and design.
"The true value of friction research lies in its potential to create solutions that enhance productivity while extending the lifespan of various components."
Nanotechnology
Nanotechnology plays a crucial role in the future of friction research. By manipulating materials at the nanoscale, scientists can achieve remarkable changes in surface characteristics. This allows for the creation of surfaces with extremely fine textures and compositions that can lead to better performance in reducing friction. For example, the development of superhydrophobic surfaces can lead to lower friction in aquatic environments.
Researchers are also investigating coatings that incorporate nanoparticles. Such coatings can enhance the durability of surfaces while maintaining low friction levels. The applications of nanotechnology span various sectors, including aerospace, automotive, and biomedical fields. The precision afforded by nanoscale manipulation enables engineers to tailor properties for specific uses, unlocking new possibilities in design and function.
Smart Materials
Smart materials offer additional potential in the study of friction. These materials can change their properties in response to external stimuli, such as temperature or pressure. The integration of smart materials into engineering designs can lead to systems that automatically adapt friction levels based on their operational environment.
For instance, shape memory alloys can return to their original shape after deformation, offering dynamic responses in applications like adaptive braking systems. Similarly, piezoelectric materials can generate electric charge when subjected to mechanical stress, potentially allowing for energy harvesting while simultaneously managing friction.
Overall, the exploration of smart materials is set to refine our understanding of the friction coefficient while presenting innovative solutions to complex engineering challenges.
The End
In the exploration of the friction coefficient, understanding its significance cannot be overstated. This concept serves as a bridge between theoretical physics and practical engineering applications, underlining the relevance of friction across various fields.
The article has detailed critical elements surrounding the friction coefficient, including its types, influencing factors, measurement techniques, and applications. Each of these areas contributes to a broader understanding of how friction operates in real-world scenarios. The interplay between material properties, environmental conditions, and contact pressure shapes the friction coefficient in unique ways. By grasping these nuances, professionals in engineering and other disciplines can make informed decisions.
The exploration of measurement techniques stands out as particularly essential. Knowledge of both direct and indirect methods allows researchers and engineers to obtain accurate friction values, which are paramount for the design and optimization of systems. This practical understanding facilitates advancements in technology and safety.
Considering future trends in friction research adds another layer to its importance. With the rise of nanotechnology and smart materials, the opportunities to manipulate friction present exciting avenues for innovation. As new materials are developed, a deeper grasp of their friction behaviors will enhance their application in various industries.