Understanding Powder Bed Fusion Techniques and Applications
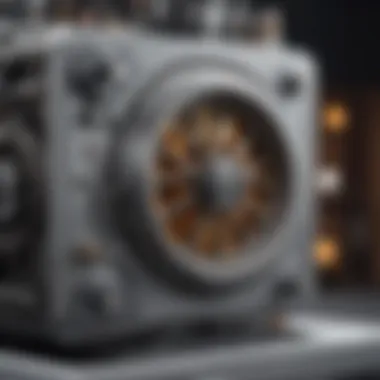
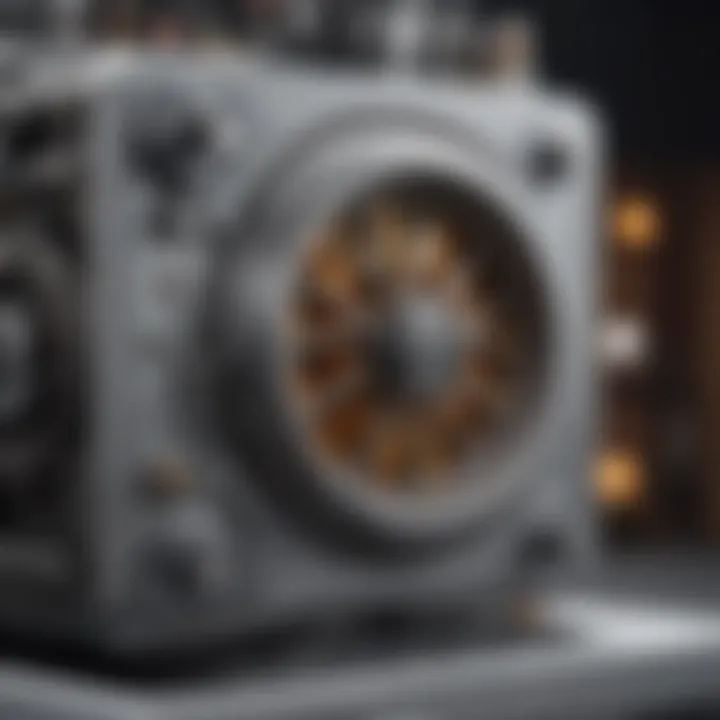
Intro
Powder bed fusion (PBF) is a prominent additive manufacturing process that relies on thermal energy to transform powdered materials into solid structures. This method is gaining traction in numerous industries due to its ability to create complex geometries and customizable designs. The ability to manipulate materials at a granular level opens avenues for innovation and efficiency in manufacturing.
This article aims to explore the various facets of powder bed fusion. It delves into the techniques employed in this process, the applications across multiple sectors, and the ongoing innovations shaping its future. Understanding these components is vital for students, researchers, educators, and professionals as they navigate the evolving landscape of modern manufacturing.
Key topics will include the basic principles underpinning PBF, its advantages and limitations, as well as its significant role in industries like aerospace, medical, and automotive. Addressing challenges in material compatibility and integration will also provide insights into the hurdles that still need to be overcome. As we dive deeper into this subject, we will uncover research findings and methodologies that enhance our grasp of powder bed fusion.
In this discussion, we will emphasize the importance of continual research and development efforts in this field. Such advancements not only improve production techniques but also foster sustainable practices in manufacturing. By the end of this article, readers will have a comprehensive understanding of the potential and limitations of powder bed fusion, enabling informed decisions in their respective domains.
Preamble to Powder Bed Fusion
Powder bed fusion (PBF) represents a significant leap in additive manufacturing. This method utilizes thermal energy to selectively bond powdered materials, creating complex three-dimensional structures. Understanding PBF is essential for anyone interested in modern manufacturing, especially as the demand for highly tailored and efficient production processes increases across various sectors.
The fundamentals of powder bed fusion not only reveal the technology's efficiency but also highlight its transformative potential in industries such as aerospace, medical, and automotive. The capacity to produce parts that are both lightweight and robust opens new avenues for innovation. Moreover, this technique enables the production of geometrically intricate designs that would be impossible or cost-prohibitive with traditional manufacturing methods. As we delve deeper into the techniques and applications of PBF, we will illuminate its benefits, challenges, and the ongoing advancements that shape its future.
Definition and Overview
Powder bed fusion is defined as a collection of additive manufacturing processes that consolidate powdered material using thermal energy. The heat source, typically a laser or an electron beam, selectively fuses the powder particles layer by layer. This process allows for precise control over the microstructures of the final parts. In essence, powder bed fusion can be seen as an intersection of materials science, thermal dynamics, and engineering design.
This technique is particularly notable for its ability to use a broad range of materials, including metals, polymers, and ceramics. As industries continue to explore the capabilities of powder bed fusion, its role in creating prototypes and end-use parts has become indispensable. The continuous evolution of this technology factors significantly into the push for efficiency and customization in manufacturing.
Historical Background
The roots of powder bed fusion can be traced back to the late 1980s. The first patents related to PBF technologies emerged during this period, driven by the need for rapid prototyping solutions that traditional methods could not provide. Initial developments, particularly with Selective Laser Sintering (SLS), paved the way for more advanced applications of the PBF process.
As technologies evolved, major advancements in laser and scanning technologies improved the speed, precision, and material options for PBF. Over the following decades, manufacturers in various sectors began adopting PBF for both prototyping and production. This expansion marked a pivotal shift in manufacturing philosophies and practices, emphasizing the importance of on-demand, flexible manufacturing.
Notable manufacturers, such as 3D Systems and Stratasys, contributed to greater awareness and acceptance of powder bed fusion.
In the past few years, research and innovation have accelerated. New materials are continuously being explored, and the integration of smart technologies is enhancing control over the PBF process. As we proceed through this article, we will examine the mechanisms of powder bed fusion, the materials used, and its wide-ranging applications.
Mechanisms of Powder Bed Fusion
Understanding the mechanisms of powder bed fusion is essential because it lays the groundwork for how this technology can be effectively utilized in various industrial applications. These mechanisms involve both the principles of operation and the types of energy sources used to induce the fusing of powder materials. A deep comprehension of these concepts allows practitioners and researchers to optimize printing parameters, enhance material properties, and refine the overall production process.
Basic Principle of Operation
The basic principle of powder bed fusion revolves around the selective melting of powdered materials using focused thermal energy. The process begins with a thin layer of powder spread across a build platform. An energy source then targets specific areas of the powder bed, causing the powder particles to melt and bond—forming a solid structure. The build platform descends incrementally after each layer, allowing for additional powder to be spread and fused in subsequent steps. This layer-by-layer approach is crucial, as it ensures high precision in producing complex geometries with minimal waste.
In this context, the ability to control temperature and the modulation of energy input play significant roles in defining part accuracy and mechanical properties. An optimized operation can lead to better surface finish and reduced thermal stress in the finished parts.
Types of Energy Sources
Different energy sources can be utilized in powder bed fusion, each offering distinct advantages and characteristics that affect the performance of the process. The primary types are laser-based systems and electron beam systems.
Laser-based systems
Laser-based systems employ focused laser beams to selectively melt the powder. They are often preferred for their high precision and versatility. A significant characteristic of laser-based systems is their ability to work with a wide range of materials, including various metals and polymers. The high concentration of energy from the laser allows for rapid heating and fusion, ensuring that only the designated areas are affected.
A unique feature of laser systems is their adjustability. Operators can modify laser power, speed, and scanning patterns to meet specific requirements, which enhances their adaptability in different applications. However, they may face limitations with reflective materials, which can lead to inefficiencies or lower-quality parts if not properly managed.
Electron beam systems
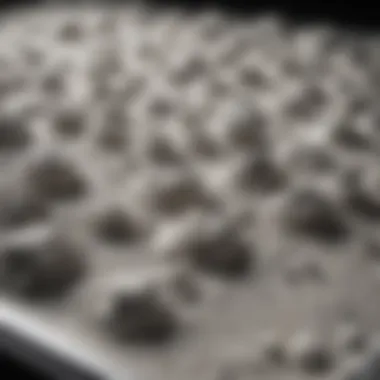
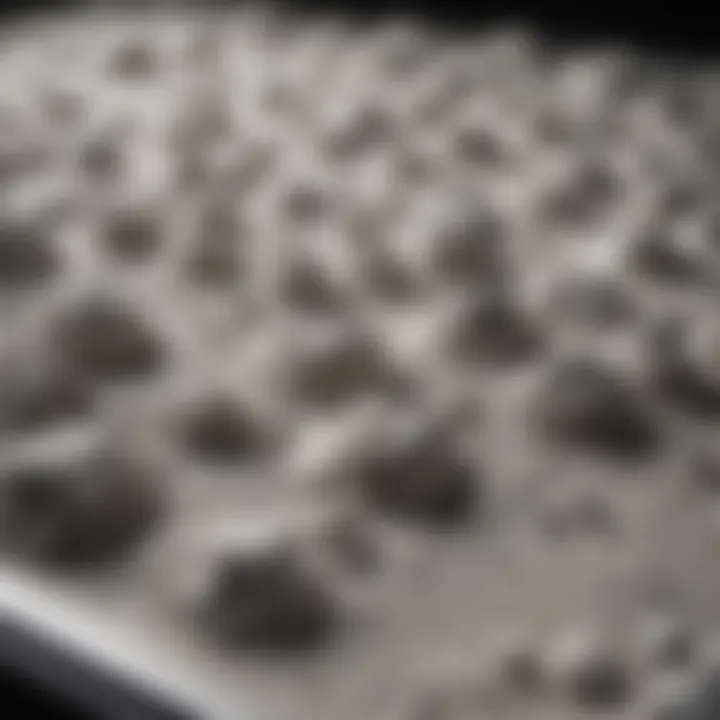
On the other hand, electron beam systems utilize high-energy electron beams for melting powder. This method is particularly advantageous for processing high-density metals. A critical characteristic of electron beam systems is their ability to be used in a vacuum environment, which minimizes oxidation and improves material quality. This feature contributes to enhanced mechanical properties of the final product, making these systems ideal for aerospace and defense applications.
Nevertheless, electron beam systems can be more costly and require more elaborate setups compared to laser systems. They also have a longer build time, which can be a detriment in high-volume production scenarios.
Material Behavior During Fusion
The behavior of materials during the fusion process is complex and significant for achieving the desired properties in the final product. When the thermal energy is applied, the powder particles undergo rapid heating, followed by melting and solidification. How fast this happens, and the resulting microstructure can vary based on the energy input, material characteristics, and environmental conditions from the processing system.
Understanding how different materials react under heat can guide researchers and practitioners in developing better processing strategies. Variability in grain size, porosity, and phase distributions can be controlled, ultimately affecting mechanical properties such as toughness, strength and ductility.
Selecting appropriate materials for specific applications requires not only knowledge of their behavior during fusion but also a strategic management of processing parameters to achieve optimal outcomes. By comprehending these mechanisms, industries can utilize powder bed fusion to create high-performance components that satisfy the demands of modern engineering tasks.
Materials Used in Powder Bed Fusion
The selection of materials in powder bed fusion is critical. The success of this additive manufacturing technique hinges on the properties and behaviors of the materials used. By understanding the various types of materials available and their specific characteristics, practitioners can effectively harness the advantages offered by powder bed fusion. This section examines metals, polymers, and ceramics, detailing their uses, advantages, and considerations.
Metals and Alloys
Metals and alloys are the most common materials utilized in powder bed fusion. Their high melting points and mechanical properties make them suitable for the production of strong and durable components. Materials like titanium, aluminum, and stainless steel are among the most popular in this category.
- Titanium: Known for its strength-to-weight ratio and corrosion resistance, titanium is widely used in aerospace and medical implants.
- Aluminum: This metal offers excellent thermal properties and is popular in the automotive sector for producing lightweight components.
- Stainless Steel: Known for its toughness and ability to resist corrosion, it is often used in consumer products and industrial parts.
The process involves careful management of the thermal energy to ensure precise fusion and preserve the material's desirable properties. However, one must consider factors like powder reusability and post-processing requirements when selecting metals for powder bed fusion.
Polymers and Composites
Polymers represent another important category of materials for powder bed fusion. They are typically used for applications where lightweight and flexibility are critical. Thermoplastics like nylon and thermoplastic elastomers are commonly used.
- Nylon: It is favored for its strength, flexibility, and resistance to abrasion, making it ideal for functional prototypes and end-use parts.
- Thermoplastic Elastomers: These materials are often used for applications requiring soft-touch and rubber-like characteristics. They offer good elongation and energy absorption properties.
Composites, which combine polymers with reinforcing agents, bring added strength and durability. With polymers and composites, it is essential to ensure compatibility with the powder bed fusion process. The build parameters must be adjusted to accommodate the melting characteristics of the selected material.
Ceramics and Other Materials
Ceramics are less common than metals and polymers in powder bed fusion, but they are gaining traction due to their unique properties. Materials like zirconia and alumina are notable for their hardness and heat resistance, which benefit applications in electronics and bio-materials.
- Zirconia: This ceramic is renowned for its high fracture toughness and is commonly used in dental applications.
- Alumina: It finds utility in insulating components in electrical applications thanks to its excellent thermal resistance.
Other materials, such as composite metals and advanced ceramics, are increasingly explored for niche applications. The successful implementation of these materials requires diligent consideration of their thermal properties and the energy source used in powder bed fusion.
"The material choice significantly impacts the mechanical properties, surface finish, and overall performance of the final product in powder bed fusion."
In summary, selecting the appropriate materials for powder bed fusion is vital for achieving specific performance criteria while driving innovation across various industries. As research continues to evolve along with material science, new possibilities will emerge, broadening the scope of powder bed fusion in manufacturing.
Applications of Powder Bed Fusion
The applications of Powder Bed Fusion (PBF) are diverse and impactful. This technique serves various industries by allowing complex geometries and tailored mechanical properties. These applications demonstrate the technology's adaptability and potential for innovation. PBF contributes significantly to efficiency, customization, and performance, making it indispensable in modern manufacturing. As industries seek to refine processes and reduce waste, PBF presents an ecological approach by optimizing material usage.
Aerospace Industry
In the aerospace sector, Powder Bed Fusion is critical. It provides lightweight components that can withstand extreme environments. Airlines and manufacturers can create intricate designs that traditional methods cannot achieve. This feature is essential in achieving fuel efficiency and overall aircraft performance. Parts produced by PBF, such as brackets and turbine blades, often show enhanced durability and reliability. This technology thus helps meet the stringent standards of the aerospace industry and maintains safety without compromising performance.
Medical Applications
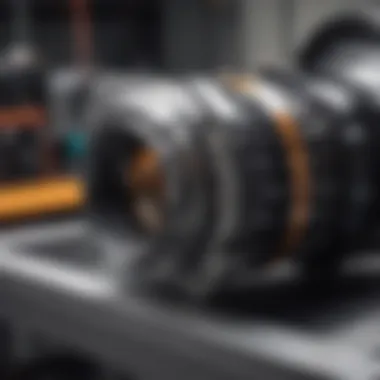
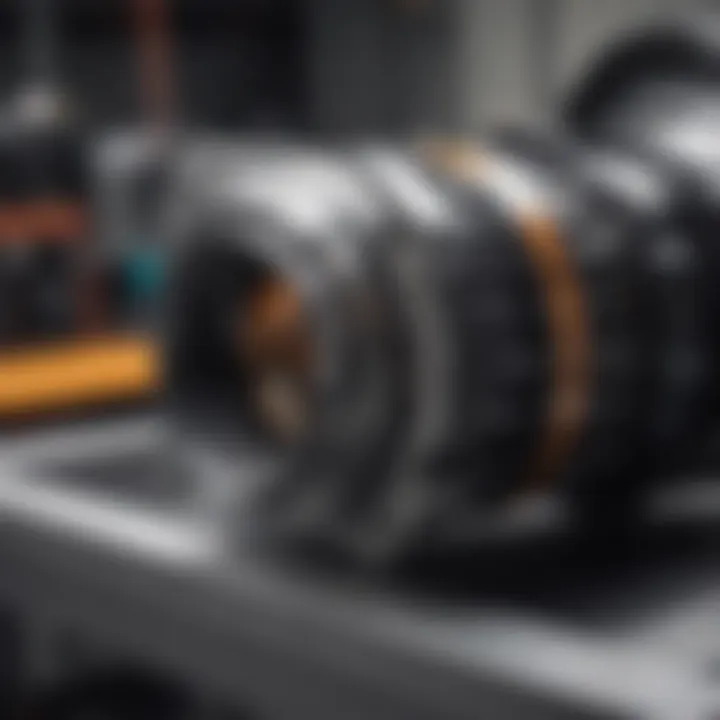
Medical applications of Powder Bed Fusion are equally significant and nuanced. This method allows for the production of highly customized devices tailored to individual patients. The impact is felt in two primary areas: implants and prosthetics.
Implants
Implants made using PBF offer specific characteristics, such as precision fitting and biocompatibility. They can be tailored to integrate seamlessly into the human body. This customization is a major strength, as it improves patient outcomes. For example, dental implants printed through this process can result in faster recovery times and better alignment. However, a challenge remains in ensuring consistent material properties, demanding strict quality control.
Prosthetics
Prosthetics crafted with Powder Bed Fusion represent a breakthrough in design and functionality. At their core, they can be optimized for comfort and performance. One of their notable characteristics is the lightweight design, which enhances user comfort. Customization means that each prosthesis can be designed to meet the unique anatomical needs of the patient. This tailoring enhances usability and satisfaction. While the initial cost may be high, the long-term benefits often justify the investment. Moreover, ongoing advancements in material science promise even better functionality in future applications.
Automotive Sector
In the automotive industry, Powder Bed Fusion is making headway with its ability to produce complex parts. Components that need to be both strong and lightweight can be created with relative ease. This capability helps manufacturers develop innovative designs to improve vehicle performance and safety. This technology also allows for rapid prototyping. Consequently, it can reduce time-to-market for new car models, providing a competitive advantage.
Consumer Goods Manufacturing
The use of Powder Bed Fusion in consumer goods manufacturing is evolving. It enables the production of customized products, from unique gadgets to household items. Such flexibility leads to a significant shift in how items are marketed and developed. Companies can reduce excess inventory by producing items on-demand, navigating through design phases efficiently. This aspect leads to cost savings and a more tailored shopping experience for consumers.
"Powder Bed Fusion transforms industries by enabling designs that blend creativity with engineering precision."
Advantages of Powder Bed Fusion
The advantages of powder bed fusion are noteworthy in the realm of additive manufacturing. These benefits set this technique apart from other fabrication processes. As industries continually seek better methods, understanding these advantages is essential for both academic research and practical applications.
Design Flexibility
One of the significant benefits of powder bed fusion is its design flexibility. This method allows for complex geometries that are not feasible with traditional machining. Designers can create intricate internal structures and shapes that are optimized for weight and performance without worrying about the limitations of subtractive methods. This opens up new horizons in aerospace and medical fields, where customized components and lightweight structures are vital.
For instance, in aerospace, parts can be designed to reduce weight while maintaining strength. Similarly, in the medical industry, custom implants can be tailored to fit individual patient needs precisely. The ability to quickly iterate and modify designs enhances innovation and accelerates the development process.
Material Efficiency
Material efficiency is another crucial advantage of powder bed fusion. This technique minimizes waste since it uses only the required powder. Unused powder can often be recycled and reintroduced into the process, thus further reducing waste. In traditional manufacturing, material loss can be significant, especially in complex geometries where cutting is necessary.
Additionally, because powder bed fusion can precisely target areas for melting, it can produce detailed parts without the need for extensive post-processing. This is particularly beneficial in industries that require high precision and strict material usage. The level of efficiency achieved not only helps in reducing costs but also supports sustainable practices which are increasingly relevant.
Shortened Production Times
Shortened production times is an advantage that gives powder bed fusion an edge over conventional methods. The ability to create parts directly from digital files reduces the time needed for tooling and setup. This allows manufacturers to produce parts more quickly, which is particularly valuable in fast-paced industries like automotive and consumer goods.
Moreover, multiple iterations of a part can be printed simultaneously. This parallel processing capability means that production schedules can be condensed, ensuring quicker delivery times. Customers demand faster lead times, and powder bed fusion meets this requirement effectively.
"The efficiency of powder bed fusion contributes significantly to its appeal in competitive markets where time is critical."
In summary, the advantages of powder bed fusion stem from its inherent properties, including design flexibility, material efficiency, and reduced production times. These benefits enhance the overall value of the manufacturing process, making it an essential consideration for industries aiming to innovate and optimize production. As the market grows, these advantages will likely be pivotal in adopting powder bed fusion more broadly.
Challenges in Powder Bed Fusion
Understanding the challenges in powder bed fusion is essential for the ongoing development and optimization of this manufacturing technique. Despite its various benefits such as design flexibility and material efficiency, the technology faces significant hurdles that can impede its full potential. This section examines the major challenges in powder bed fusion, focusing on technical limitations, material constraints, and cost factors.
Technical Limitations
Technical limitations play a crucial role in the effectiveness of powder bed fusion. One of the foremost issues is the reliance on specific equipment, which must maintain precise temperatures and environmental conditions. Variabilities in the thermal control can lead to defects in the final product.
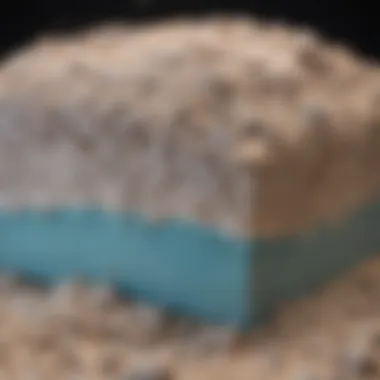
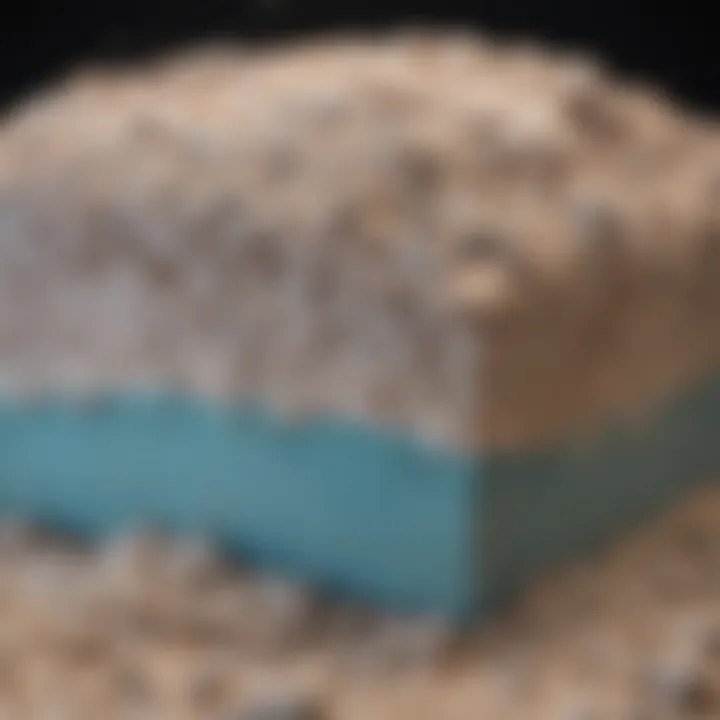
Another technical issue includes the layer adhesion. If the fusion process does not achieve the correct balance of energy input, it can result in weak inter-layer bonding. This weak bonding can compromise the mechanical properties of the printed part.
In addition, build size and complexity can strain the technology. There are limitations on the maximum build volume due to machine specifications. As a result, large components often require multiple prints and assembly, increasing complexity in processing.
Material Limitations
Material limitations present another set of challenges that affect powder bed fusion extensively. The selection of materials is critical, as not all powders respond similarly to the fusion processes. Metals like titanium and aluminum are viable, while others may not achieve the desired properties.
Furthermore, the properties of the powders can change based on their age and storage conditions. Moisture or contamination can lead to inconsistent print quality. This inconsistency hampers reliability, which is particularly concerning in high-stakes industries such as medical and aerospace.
Moreover, the recyclability of powders also raises concerns. Some materials cannot be reused efficiently, leading to waste. Thus, selecting appropriate materials becomes a balancing act of cost, performance, and environmental impact.
Cost Factors
Cost factors are crucial considerations when evaluating the feasibility of powder bed fusion. The initial investment in a powder bed fusion system can be significant. Equipment costs, maintenance, and operational expenses require considerable capital.
In addition, specific materials used in the process often come at a premium. This is particularly true for high-performance alloys and powders designed for specialized applications. If the cost of materials is high, this raises the overall production expenses, making it less accessible for smaller businesses.
Moreover, the operational costs do not end once the machine is running. Post-processing steps to achieve required surface finishes or properties also add to the expenses. This could include machining or other finishing techniques, outpacing the benefits provided by the rapid prototyping and manufacturing capabilities of powder bed fusion.
Overall, addressing these challenges is vital for advancing powder bed fusion technology. By refining processes and material usage, the industry can hope to overcome these hurdles, making powder bed fusion more efficient and accessible for various applications in the future.
Future Directions in Powder Bed Fusion
The future of powder bed fusion is poised to reshape the landscapes of various industries. As technology progresses, understanding the upcoming advancements is essential. Not only does it promise further innovation in additive manufacturing, but it also presents new opportunities for integration with existing processes, enhancing efficiency and capability. This section will outline significant elements in the future of powder bed fusion, including technological advancements, integration with other manufacturing techniques, and the ongoing needs for research and development.
Advancements in Technology
Emerging technologies in powder bed fusion are currently at the forefront of research. This includes improved energy sources, better thermal management, and innovative approaches to material application. For instance, advancements in laser technology now allow for higher precision, which leads to better surface finishes and reduced post-processing time. Additionally, the use of artificial intelligence and machine learning in optimizing printing parameters is gaining traction. These technologies support the creation of complex geometries that were previously unachievable.
Integration with Other Manufacturing Processes
Integrating powder bed fusion with traditional manufacturing processes is an area of interest. Processes such as machining, injection molding, and even subtractive manufacturing can benefit from the unique capabilities of powder bed fusion. For manufacturers, this means improved production workflows. By combining these methods, it is possible to create a hybrid manufacturing system that takes advantage of the strengths of each technique. As businesses explore this integration, they can expect to see enhanced material utilization and less waste.
Research and Development Needs
To advance the field of powder bed fusion, focused research and development initiatives are critical. Current studies are exploring the optimization of existing materials and investigating new alloys that may improve performance. Understanding the mechanical properties of parts produced through powder bed fusion is crucial. This information will enable scientists and engineers to establish performance benchmarks and safety standards. Furthermore, exploring ways to enhance the speed and efficiency of the process remains a priority.
"The future of powder bed fusion demands innovation in both materials and processes to meet industry demands."
In summary, the future directions in powder bed fusion are encouraging and multifaceted. With advancements in technology, integrated approaches, and focused research, the potential for this manufacturing process is considerable. Industries must remain proactive in preparing for these changes to harness the benefits effectively.
Culmination
The conclusion is an essential component of this article, as it encapsulates the significance and implications of powder bed fusion in modern manufacturing. This technique has emerged as a pivotal element in the realm of additive manufacturing, particularly due to its capability to produce complex geometries that traditional methods struggle to achieve. By summarizing the key aspects discussed, it highlights the benefits, challenges, and future directions of this technology, providing a roadmap for its application across various sectors.
Summary of Key Points
A clear understanding of powder bed fusion unfolds several critical points:
- Solidification Process: The technology employs thermal energy to create solid structures from powdered materials, which is fundamental for producing precise components.
- Material Versatility: It supports a range of materials, from metals to polymers, allowing for diverse applications tailored to industry needs.
- Efficiency in Production: Fast production cycles and reduced material waste maximize efficiency, which is increasingly vital in competitive markets.
- Application Diversity: Industries such as aerospace, medical, automotive, and consumer goods leverage this technique to innovate and maintain quality standards.
Final Thoughts on the Impact of Powder Bed Fusion
In summary, powder bed fusion stands at the intersection of innovation and practicality. Its implications extend beyond mere production capabilities; it represents a shift toward smarter manufacturing solutions. As industries evolve, understanding these advancements is crucial for researchers, professionals, and educators alike.
"Powder bed fusion alters the landscape of manufacturing, making it more adaptable, sustainable, and efficient."
It is clear that ongoing research and development will continue to expand its potential. As challenges in material compatibility and integration are addressed, the future of powder bed fusion promises even wider application, fostering ongoing innovation in numerous fields. The technology not only contributes to production efficiency but also inspires new design possibilities.
Thus, a thorough grasp of its principles and applications can lead to transformative advances in manufacturing, driving progress across many domains.